Some 20,000 people have descended on Glasgow, Scotland, to attend the United Nations’ 26th Climate Change Conference of Parties (COP26), which runs until Nov. 12. They are discussing ways to emit less carbon and hold the planet’s temperature increase to less than 1.5 degrees Celsius. “As countries begin to recover from the coronavirus pandemic, we must take the historic opportunity to tackle climate change at the same time — to build back better, and greener,” said Alok Sharma, COP president designate. “We can deliver green recoveries across the globe that bring in good jobs, trillions in investment and groundbreaking new technology. And we must.”
GE representatives are among the attendees, and we want to highlight some of the steps GE is taking to make the world more sustainable, help with the energy transition to reduce carbon emissions and decarbonize aviation along with other industries. Innovation is a key component of this effort. Take a look at our list.
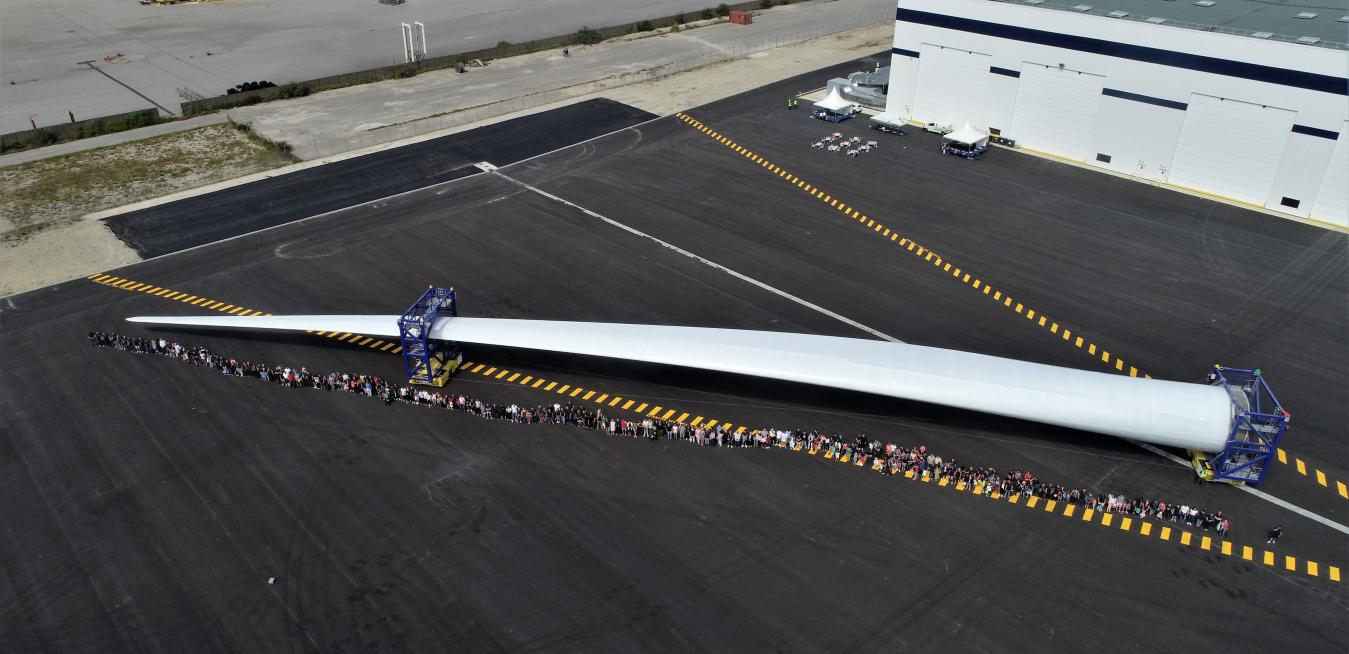
A single blade for the Haliade-X wind turbine is longer than a football field. Top: The nacelle of the Haliade-X wind turbine. Images credit: GE Renewable Energy.
Last year, GE committed to becoming carbon neutral in its operations by 2030. In GE’s 2020 Sustainability Report, released in July, the company is going even further, with an ambition to be net-zero by 2050, including Scope 3 emissions from the use of sold products. GE’s tradition of innovation will play a big role as engineers find new ways to help solve looming challenges like the energy transition to address climate change, precision healthcare that personalizes diagnoses and treatments, and smarter and more efficient flight — while also working to improve the quality of life for people everywhere.
Roger Martella, GE’s chief sustainability officer, who will be in Glasgow, has a better understanding of the size of the problems — and of GE’s potential to help solve them — than most people. Speaking with GE Reports, he said it’s important to remember that there’s no one-size-fits-all solution. Instead, any advances must be tailored to varying socioeconomic conditions, different political systems and geographies. Says Martella, “We know the stakes are high, and we know that we have to succeed.” Read our Q&A with Martella here.
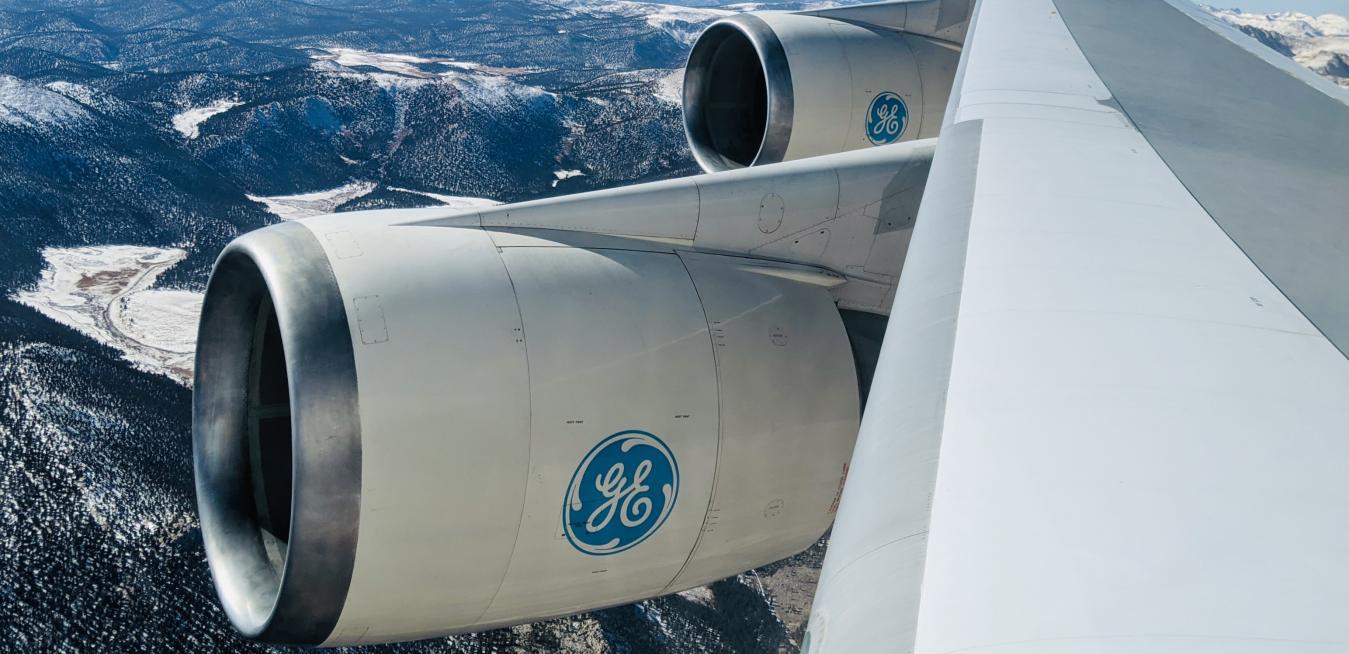
A flight of GE Aviation’s flying testbed in California that used sustainable aviation fuel. “Sustainable fuel is not a research project that we are doing on the side. It is happening,” says Gurhan Andac. Image credit: GE Aviation.
By switching from petroleum to sustainable aviation fuel (SAF), the aviation industry could reduce its carbon contribution from fuel by up to 80%, factoring in the entire life cycle of the fuel. One person who knows a lot about this task is Gurhan Andac, who as GE Aviation’s engineering leader for aviation fuels and additives is working on biofuels and synthetic fuels for engines. “Sustainable fuel is not a research project that we are doing on the side,” Andac says. “It is happening. We are flying today with SAF blends.” Read our story here and find out more about a recent Etihad flight powered by a SAF blend here.
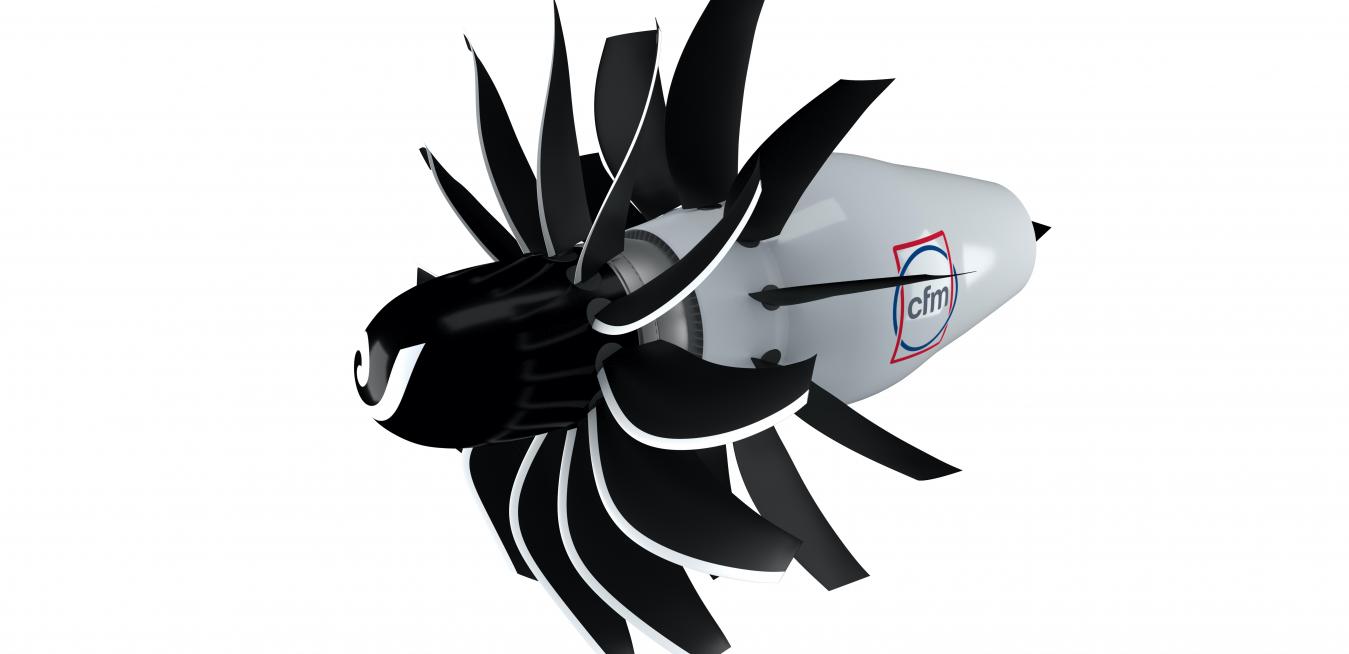
CFM’s open rotor concept. Image credit: CFM International.
In October, the Air Transport Action Group declared the aviation industry’s commitment to a goal of net-zero carbon emissions by 2050. The group’s members include GE Aviation, which invested $1.8 billion in 2020 in aviation research and development, including new advanced materials and technologies that can help cut fuel consumption and even enable hybrid electric design. In June, CFM International, a 50-50 joint company between GE and Safran Aircraft Engines, announced the launch of the Revolutionary Innovation for Sustainable Engines (RISE) Program to demonstrate advanced technologies for the next generation of engines, which could ultimately lead to engines that would use 20% less fuel and produce 20% fewer CO2 emissions than the most efficient jet engines built today. “This technology development program demonstrates the commitment GE and Safran share for achieving ambitious goals for a more sustainable future,” says Travis Harper, GE product manager on the CFM RISE Program. Read more about the declaration here and the RISE Program here.
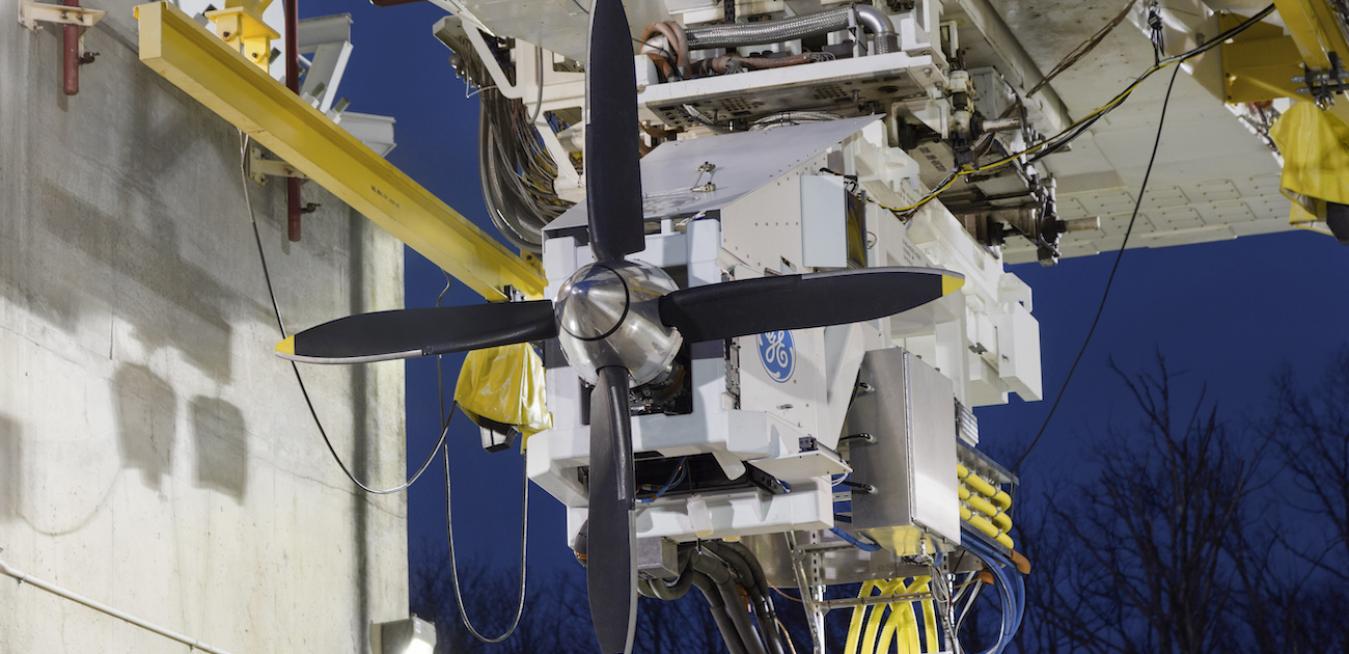
A megawatt-class GE a motor/generator electrically powering an 11-foot diameter propeller on a test stand. Image credit: GE Aviation.
“Decarbonizing aviation is our industry’s moonshot,” GE Aviation president and CEO John Slattery wrote after a visit to NASA in September. Now GE engineers and the U.S. space agency get to work on the moonshot together: NASA recently awarded GE $179 million to help mature electric flight propulsion technologies. Find out more about what that means here.
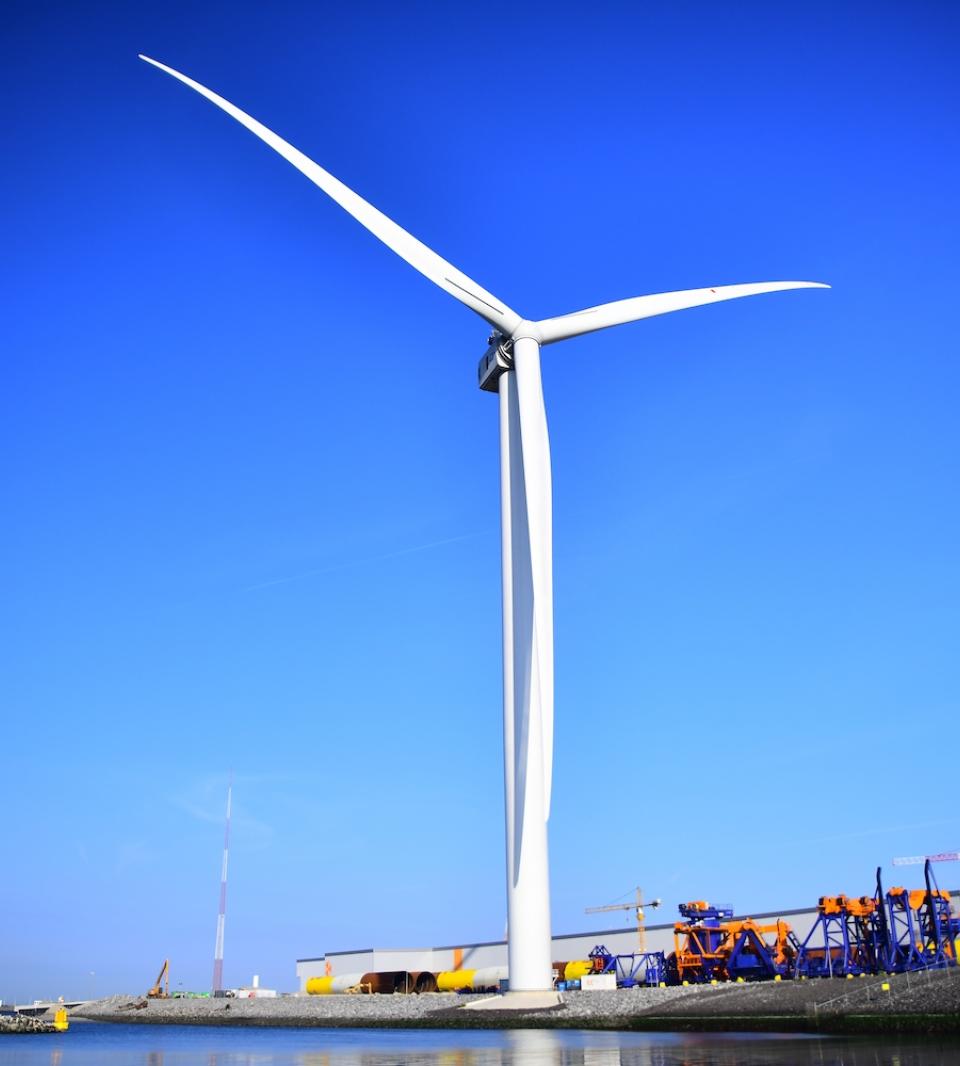
Each Haliade-X turbine can save the equivalent of the emissions generated by 11,000 vehicles in one year. Image credit: GE Renewable Energy.
GE Renewable Energy engineers first tested the Haliade-X, the most powerful wind turbine ever built, in November 2019. Less than two years later, that 12-megawatt model has been optimized to produce 14 MW of electricity. At that level, GE Renewable Energy says, the turbine “can generate up to 74 gigawatt-hours of gross annual energy production, saving up to 52,000 metric tons of CO2, which is the equivalent of the emissions generated by 11,000 vehicles in one year.” Learn more here.
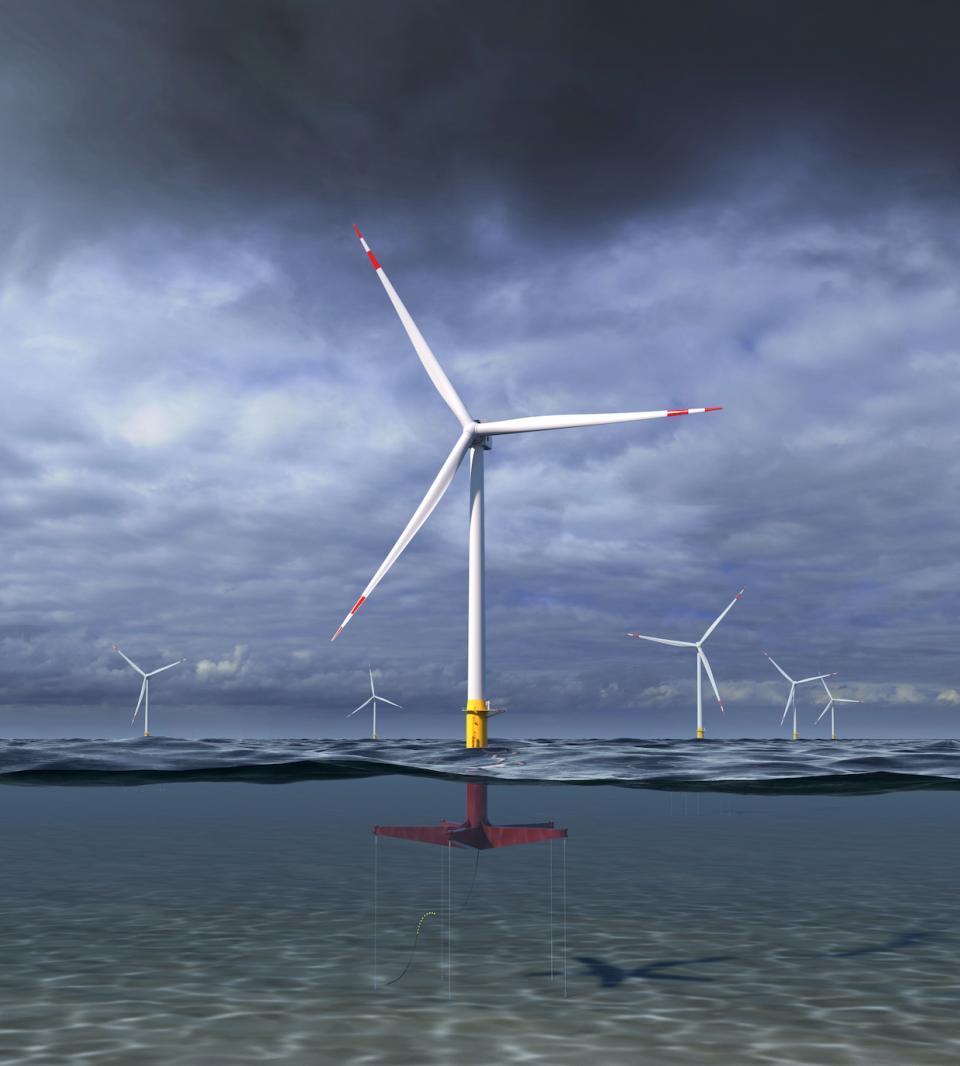
An artist’s rendering of a floating wind farm. Image credit: Glosten.
We know how to build wind farms on land and in relatively shallow waters, but it’s an entirely different story in places where the continental shelf quickly drops off, like parts of the West Coast. A team at GE Research has developed a floating wind turbine concept that expects to make that possible. Unlike fixed-bottom offshore turbines that require depths less than 60 meters (200 feet), the new design includes “active tendons” to keep the platform safely tethered to the seafloor while allowing it to ride big waves and reduce the magnitude of the overall mechanical load.
GE and marine industry innovator Glosten have joined to design a 12-MW floating version of the Haliade-X. The concept calls for turbines that are 853 feet tall, with a rotor diameter of 720 feet, that can each generate 67 gigawatt-hours of electricity a year. Just one such machine could produce enough electricity to power the equivalent of 16,000 American households. The proposal comes with advanced controls that could allow it to be installed in deep coastal waters. The concept is sponsored by the Department of Energy’s Advanced Research Projects Agency-Energy (ARPA-E). The story is here.
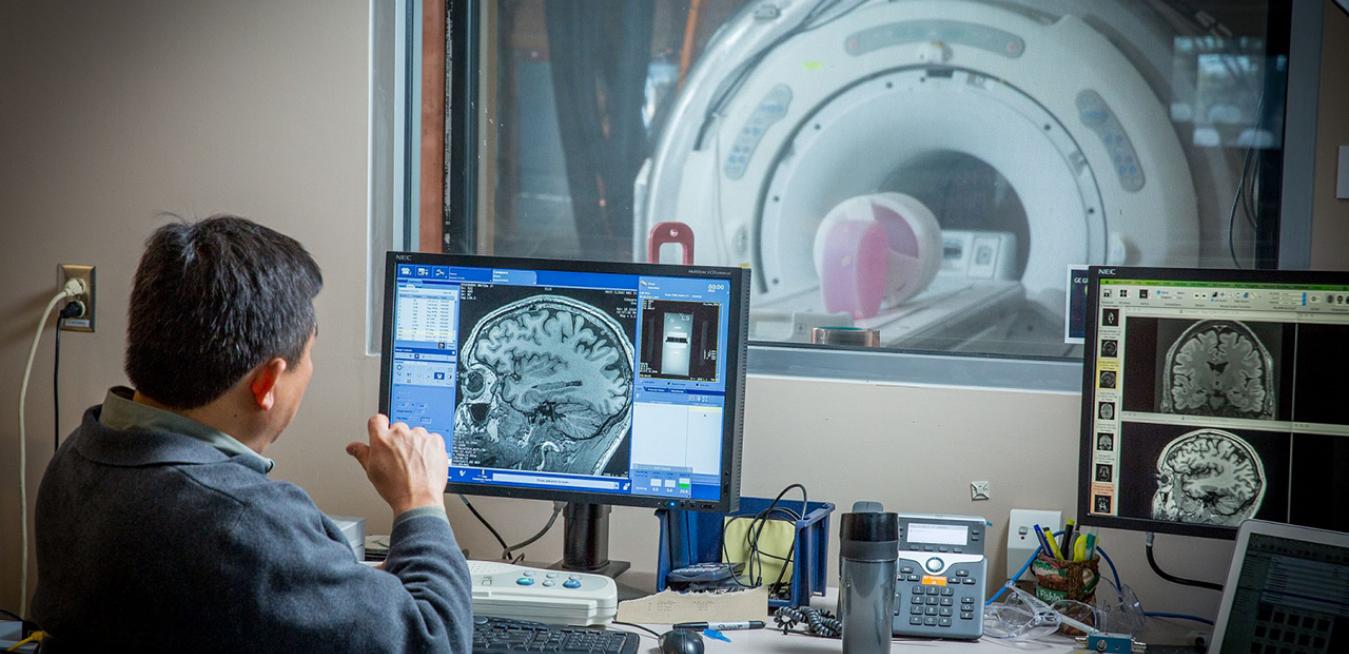
A 3 Tesla MRI system installed in GE Research’s dedicated MRI lab facility on its Niskayuna, New York, campus. Image credit: GE Research.
A discovery made in the coldest cold more than a century ago is heating up GE’s wind turbine research. In 1911, Dutch physicist Heike Kamerlingh Onnes found that electrons, which usually lose energy as they careen around an electrical conductor, met no resistance in a mercury wire cooled to near absolute zero — the lowest possible temperature, minus 459.67 degrees Fahrenheit. That phenomenon, known as superconductivity, can help computer chips run faster, and it enabled magnetic resonance imaging (MRI), among other things. Now superconductivity may be paving the way to more efficient generators for powerful offshore wind turbines.
Backed by a $20.3 million contract from the Department of Energy, GE researchers are looking for ways superconducting generators can help lower wind energy costs, simplify the turbine manufacturing supply chain and support the DOE’s goal of nearly tripling wind power’s share of U.S. energy production to 20% over the next decade. The story is here.
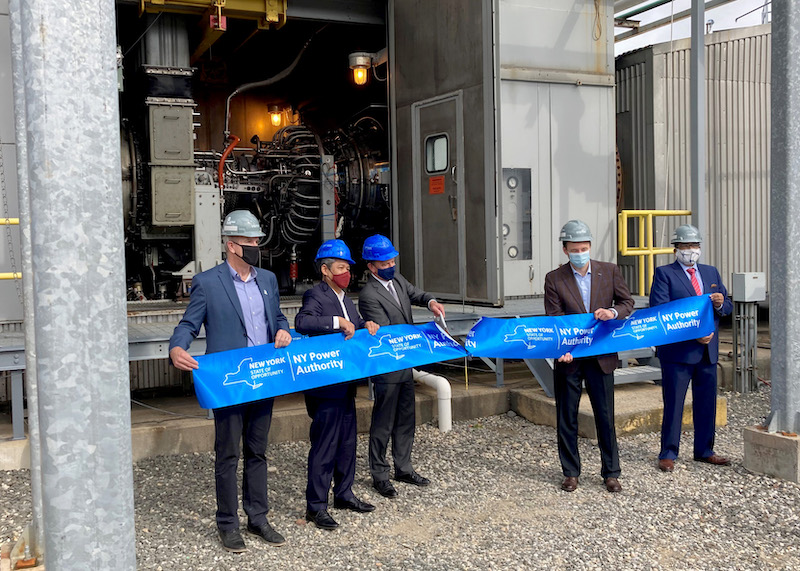
New York Power Authority’s ribbon-cutting ceremony at the Brentwood Power Station on Long Island. Image credit: GE Gas Power.
In early July, New York State decided to bring green hydrogen into the state’s portfolio of sustainable energy solutions — and GE is helping the state to make it happen. This fall, the Brentwood Power Station on Long Island began a demonstration project to test the feasibility of running on a blend of natural gas and green hydrogen, a fuel without carbon. That’s because green hydrogen uses renewable electricity to split water molecules and produce oxygen and hydrogen.
GE Gas Power, whose combustion turbine powers the station, is providing the blending technology and helping execute the project. And this GE unit already has a leadership role in the use of hydrogen in gas turbines. GE turbines have logged more than 6 million operating hours running on blends of hydrogen, and power facilities that will go online in Ohio and Australia will use blends of hydrogen and natural gas. Hydrogen could remove millions of tons of CO2 from the atmosphere by the end of the decade. Green hydrogen specifically uses renewable electricity to split water molecules and produce oxygen and hydrogen.
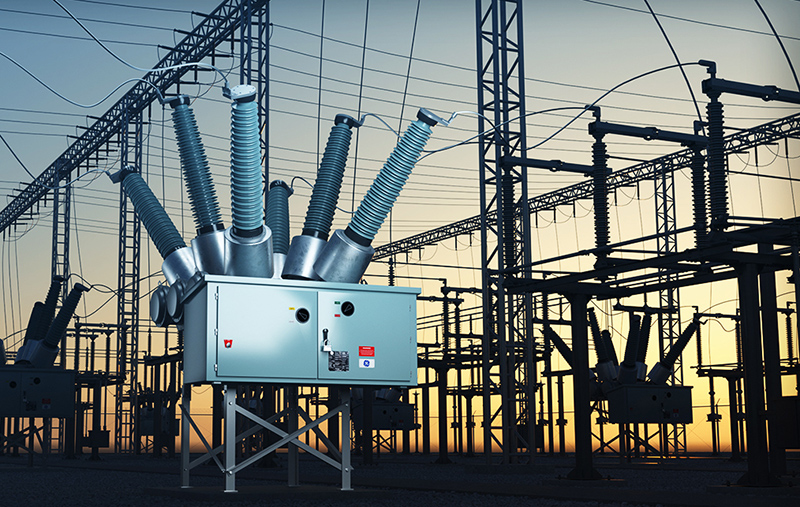
High-voltage electrical substations, which adjust voltage up or down so that electrical power can travel over long distances, have for decades relied on an insulator that is among the world’s most potent greenhouse gases. The new g3 insulating gas reduces the warming potential by 99%. Image credit: GE.
The energy transition to a less carbon-intensive future has many key components. We need wind farms, solar panels, hydropower stations and other sources to generate renewable energy. But we also need an infrastructure with reduced environmental impact to ship electricity to customers.
Take high-voltage electrical substations. These ubiquitous installations, which adjust voltage up or down so that electrical power can travel over long distances and be used in homes and businesses, have for decades relied on a highly effective insulator, sulfur hexafluoride (SF6). The problem is that SF6 is also among the world’s most potent greenhouse gases and can linger in the atmosphere for millennia.
A few years ago, in collaboration with 3M, GE Renewable Energy developed an SF6 replacement known as g³ insulating gas that reduces the warming potential of SF6 by more than 99% while retaining the same insulating qualities. It also allows electric substations to keep the same compact dimensions. And this week, the GE unit received $3.7 million in funding from the U.S. Department of Energy’s Advanced Research Projects Agency-Energy (ARPA-E) for two related projects to help accelerate the decarbonization of the U.S. electrical grid. Read the story here.
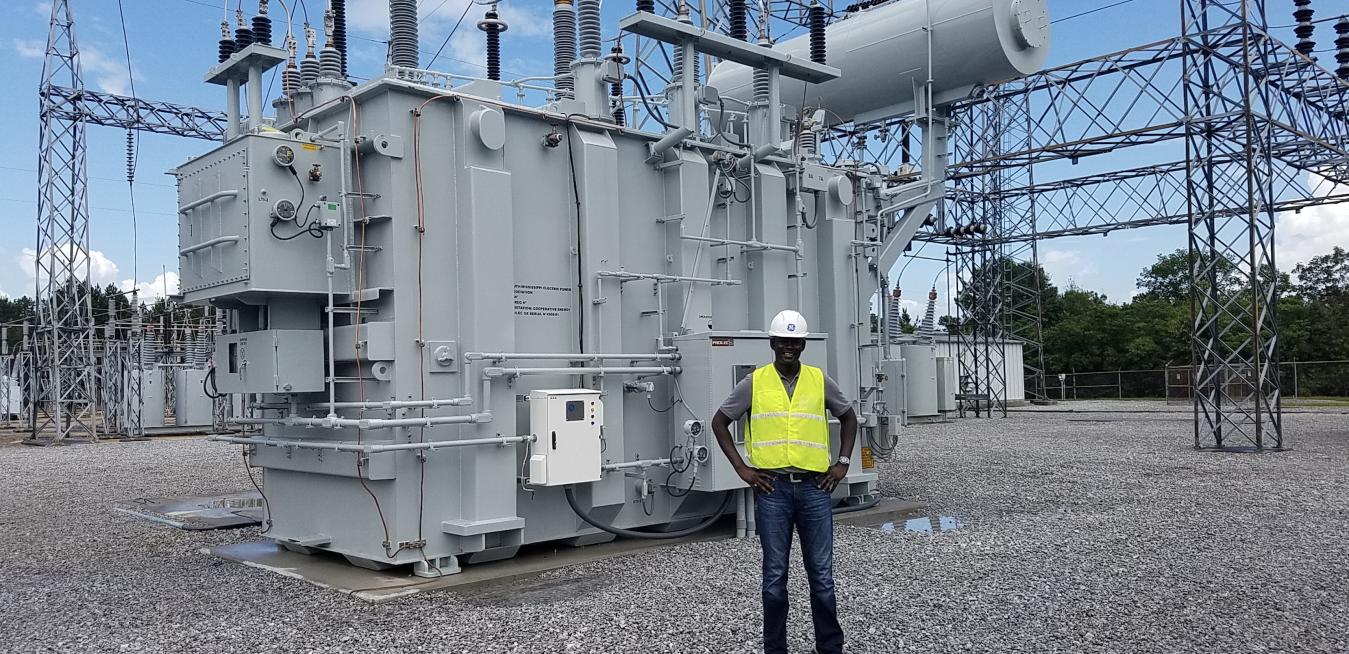
“When you have a lot of renewables, your power can quickly disappear,” says GE’s Ibrahima Ndiaye, an engineer at GE Research. “That’s why you need much faster controls and flexible equipment to work with them. Image credit: GE Research.
“The grid is the largest industrial system built by mankind,” says Vera Silva, chief technology officer at GE Renewable Energy’s Grid Solutions unit. She says the modern grid must “facilitate the access” to all of these sources while ensuring “that the system is working like a Swiss clock.”
Keeping everything in balance and working — in an era when freak weather events can suddenly bring portions of the power system to its knees — is even more impressive when you discover that the technology that forms the grid’s backbone was invented more than a century ago. Now GE and Prolec GE engineers are working to make the jobs of utilities and grid operators easier. They are developing a new kind of “flexible transformer” that could help protect the grid from contingencies like power line failures or extreme weather, help prevent severe outages and restore power faster when they happen, and help operators bring more renewables online. At the same time, it also could make the modern grid cheaper to build and maintain. Read the story here.
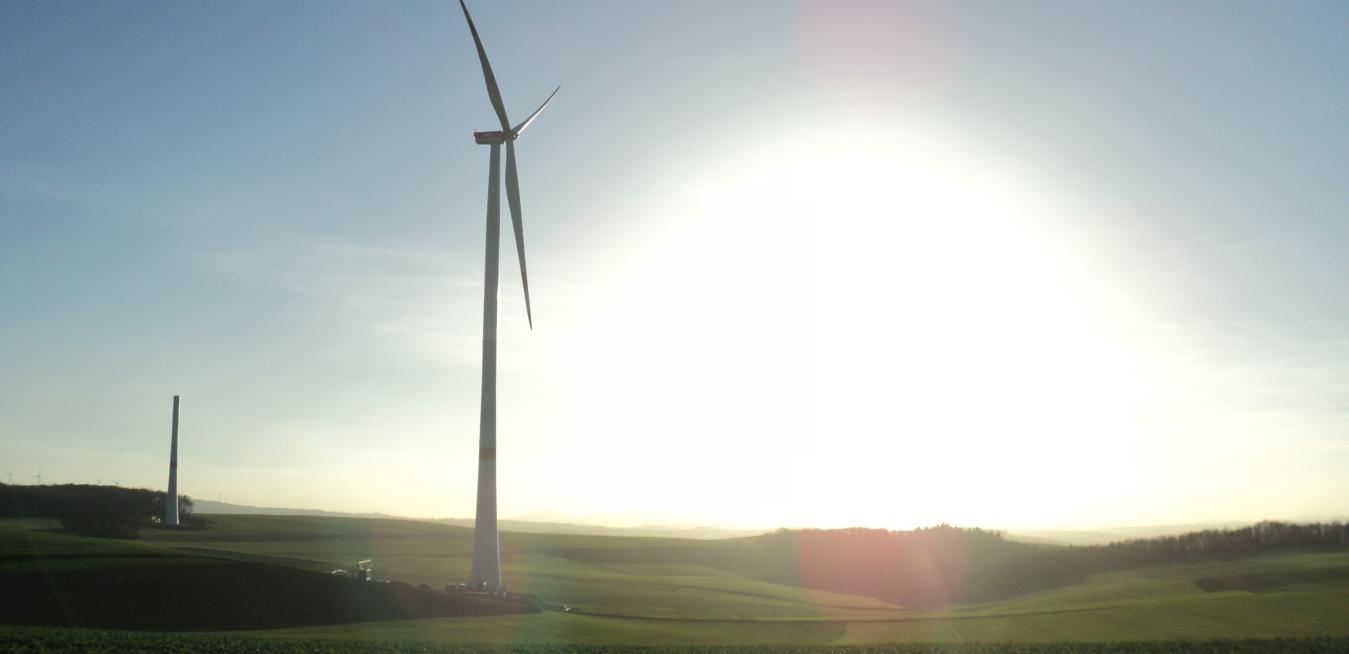
GE Renewable Energy just signed preliminary agreements with German and French-Swiss companies to dismantle, crush and co-process wind turbine blades from some of the continent’s onshore turbines that are approaching the end of their lives. Image credit: GE Renewable Energy.
Wind power is a fast-growing source of renewable energy, but that doesn’t mean the industry isn’t trying to lower its carbon footprint. One way involves lowering emissions in the wind turbine’s entire life cycle, from raw material sourcing to manufacturing processes to component transportation. That’s why GE Renewable Energy signed preliminary agreements in June with German and French-Swiss companies to dismantle, crush and co-process the blades from some of the continent’s onshore turbines that are approaching the end of their life.
The deals come on the heels of a 2020 landmark agreement with Veolia North America to recycle blades removed from its onshore turbines in the United States. GE Renewable Energy’s European partners will follow a similar process: recycling the glass fibers and fillers from the decommissioned blades to be used as raw materials in cement, while recovering the organic materials of the blades as an energy source for the cement manufacturing process. Europe’s cement manufacturers are aiming for net-zero emissions by 2050, and GE says manufacturing cement this way could emit as much as 20% less CO2 compared with conventional processes. Jérôme Pécresse, CEO of GE Renewable Energy, called the deals “a truly exciting next step in our journey to introduce new circular life cycle improvements for the wind industry in Europe.” Read the story here.
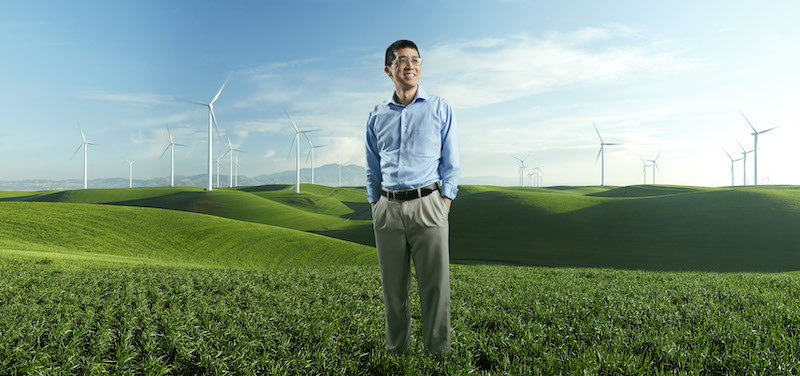
Lawrence Cheung, a lead mechanical engineer at GE Research, specializes in harnessing the computational firepower of modern supercomputers to create elaborate models of how the wind moves in the real world to make the most of its energy. Image credit: GE Research.
Lawrence Cheung, lead mechanical engineer at GE Research, has been using supercomputers to gain an elaborate understanding of how wind farms use wind and affect wind flows. Knowledge like that is increasingly valuable for countries and energy producers seeking the most optimal arrangement of renewable sources of energy.
Cheung’s latest work can model airflow across a wind farm that spans 5,000 acres, or more than 3,780 football fields. Known as computational fluid dynamics simulations, his supercomputer models break wind farms up into hundreds of millions of individual cubic meters for a granular understanding. His goal isn’t to eliminate the wind-wake problem, but to understand the precise impact of the slower air after it passes through a turbine in different wind farm configurations. That way, the cost of reducing wind wake can be weighed against the price of building farms with more widely spaced turbines. With coordinated wind energy development, everybody win(d)s. You can read the story here.
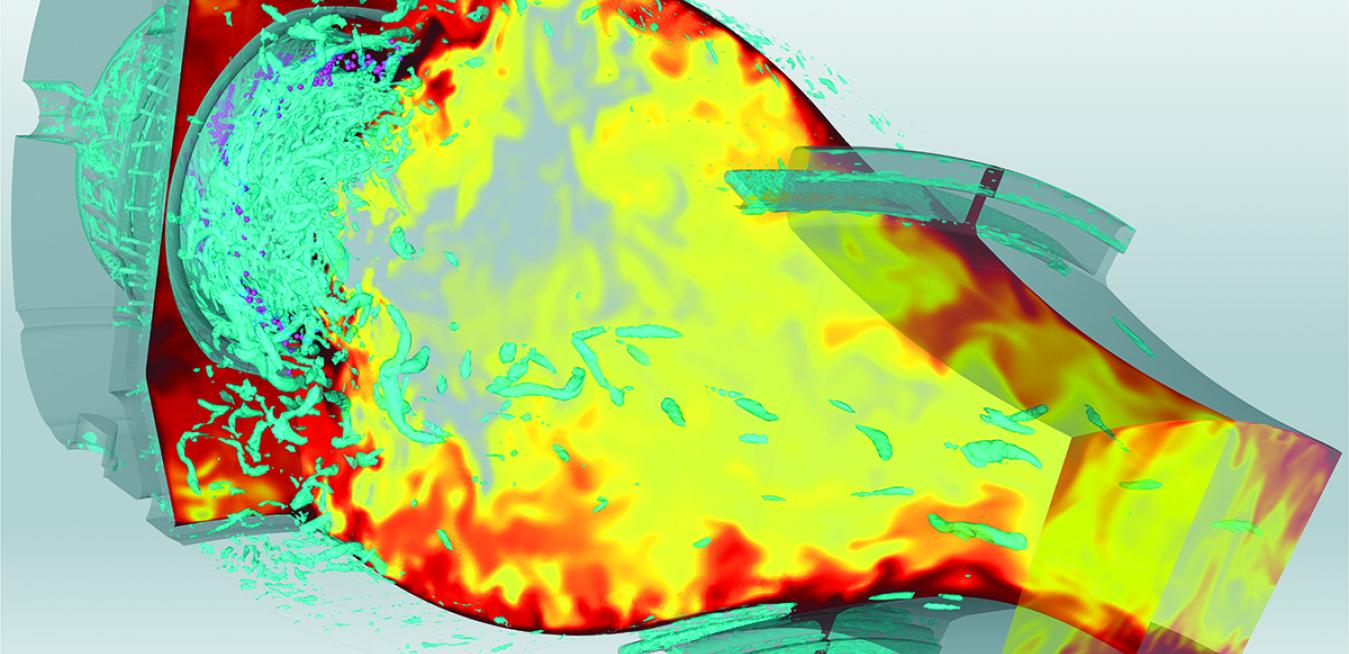
A high-fidelity simulation for predicting turbine temperature and flow fields obtained by a supercomputer. Image credit: GE Research.
Fun fact: Engine turbines, including those in airplane engines, can run hotter than the melting point of their parts — yet the parts don’t melt. That may seem counterintuitive to most of us, but it’s all in a day’s work for engineers at GE Research, who pursue a deep understanding of how heat flows through engine turbines. Why? Because it’s a key element to a broader challenge: Given the central role turbines play in aircraft engines and electrical generation, even tiny tweaks in design could lead to enormous savings in cost and efficiency. Part of that work involves running computer simulations, said GE Research engineer Rick Arthur: “Just like biologists use microscopes or astronomers use telescopes, high-fidelity simulations empower researchers to see what they otherwise could not.” The fidelity’s about to get even higher, as GE Research has been granted the use of one of the world’s most powerful supercomputers, Summit, housed at Oak Ridge National Laboratory in Tennessee. The supercomputer will allow the researchers to create realistic simulations of turbulent heat flows coursing through engines better than they could with older computer models of turbines, which simply couldn’t process the data fast enough. Read the story here.
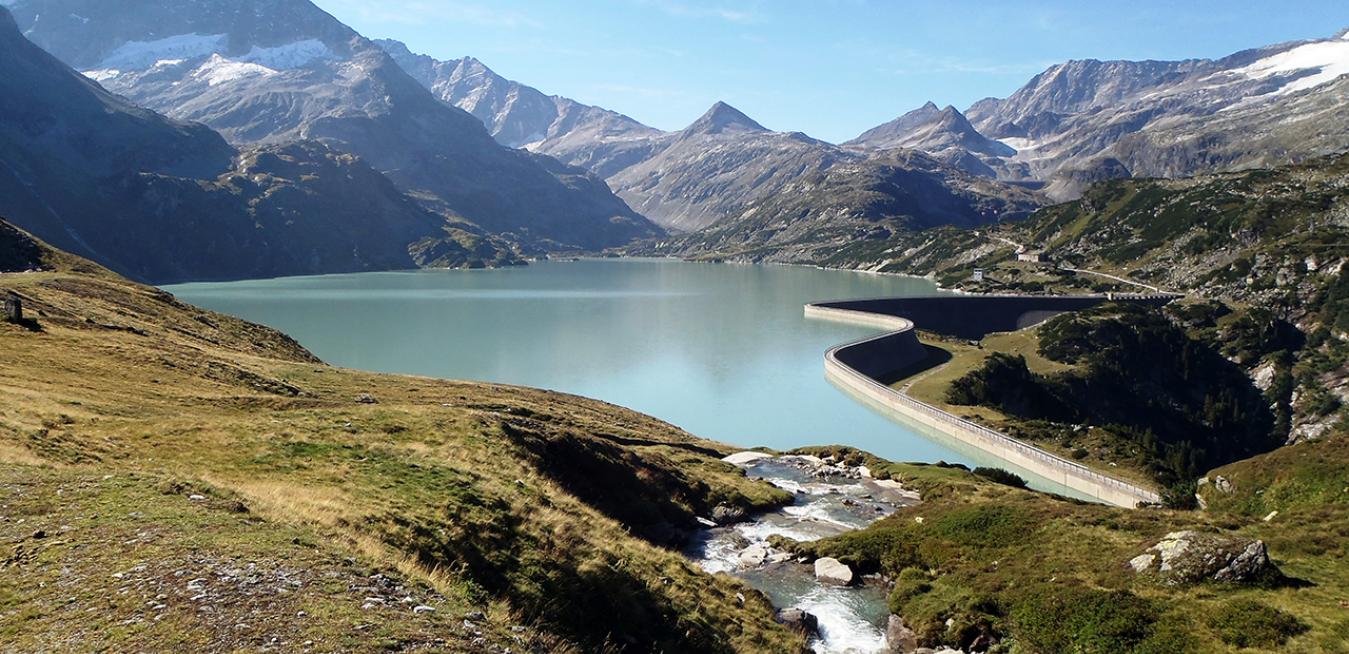
Tauernmoos, a 170-megawatt Austrian plant scheduled to come online in 2025, will utilize low-cost surplus power from Austria’s grid to push water uphill and store it in a lake. When the plant wants to generate electricity, the water will reverse its course, running downhill through the same pump turbine. Image credit: ÖBB.
Austria is a longtime hydropower pioneer, and the nation’s energy transition is moving mountains — by moving water. ÖBB, the country’s main railway operator, is taking Austria’s electrified railway system to a new level by adding variable-speed pumped hydro storage to the mix and essentially building a giant battery high up in the mountains. Scheduled to come online in 2025, ÖBB’s 170-megawatt Tauernmoos plant is expected to operate in two modes. In pump mode, it will utilize low-cost surplus power from Austria’s grid to push water by as much as 260 meters uphill and store it in a lake. In turbine mode, the water will reverse course, running downhill through the same pump turbine to produce electricity. The plant will then be able to dispatch that power to the grid to help smooth any gaps in supply from other renewable energy sources.
Tauernmoos will be much more than a powerful source of on-demand renewable power for the country’s trains. Pumped storage also underpins Austria’s goal of power generation from a 100% renewables-based grid by 2030. And in a world first for a variable-speed pumped storage plant, a single original equipment manufacturer — GE Renewable Energy — is not only designing, building and installing Tauernmoos’ two 85-MW pump and turbine generator units, it will also be responsible for integrating the power transformers and frequency converters that will help ensure smooth, flexible and synchronized electricity transfer between the plant, the network and the grid. Find out how here
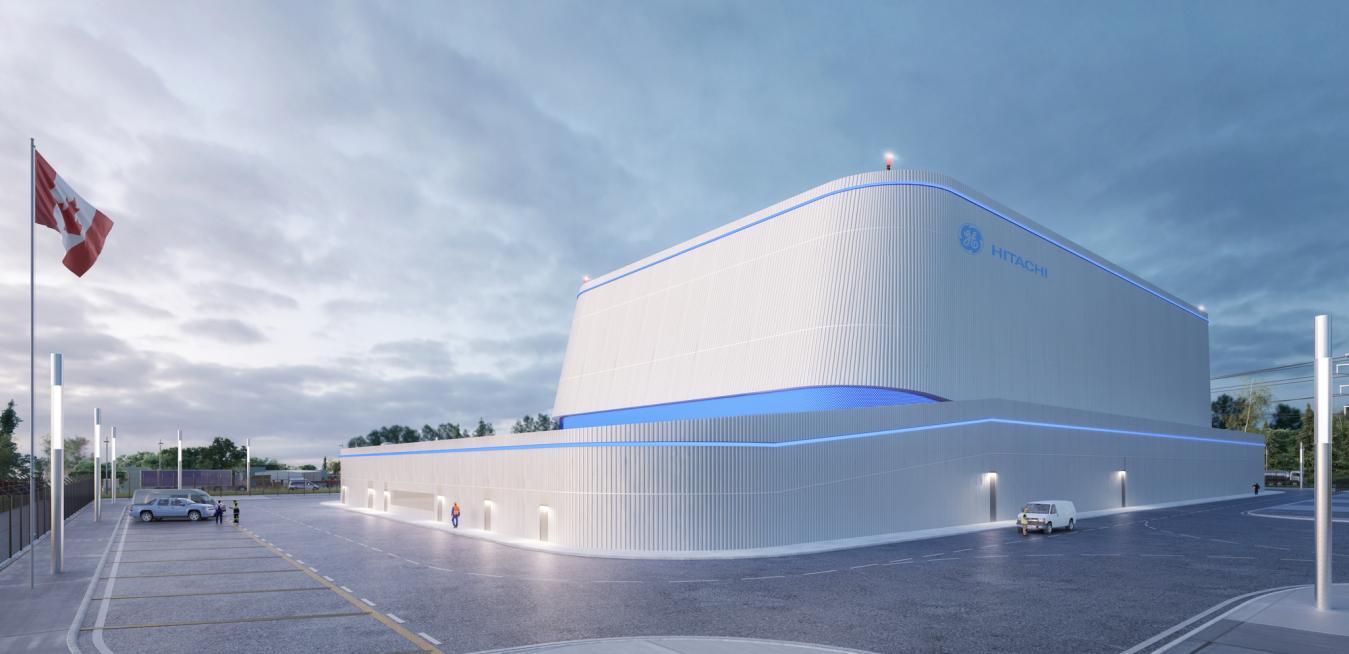
A rendering of a facility using GE Hitachi’s BWRX-300 reactor. Image credit: GE Hitachi.
Workers at GE Hitachi Nuclear Energy in Wilmington, North Carolina, are developing a new generation of nuclear reactors called small modular reactors (SMRs) that produce carbon-free electricity while they are in operation and promise to play an important role in tomorrow’s energy ecosystem. When the wind isn’t blowing and the sun isn’t shining, SMRs will be able to step up and pump out large amounts of energy.
Canada aims to be a global leader in this technology. In September, a memorandum of understanding between GE Hitachi Nuclear Energy, which develops SMR technology, and partners in Poland and Canada paved the way for those two countries to collaborate on a fuel supply chain for reactors in Poland. Learn more here.