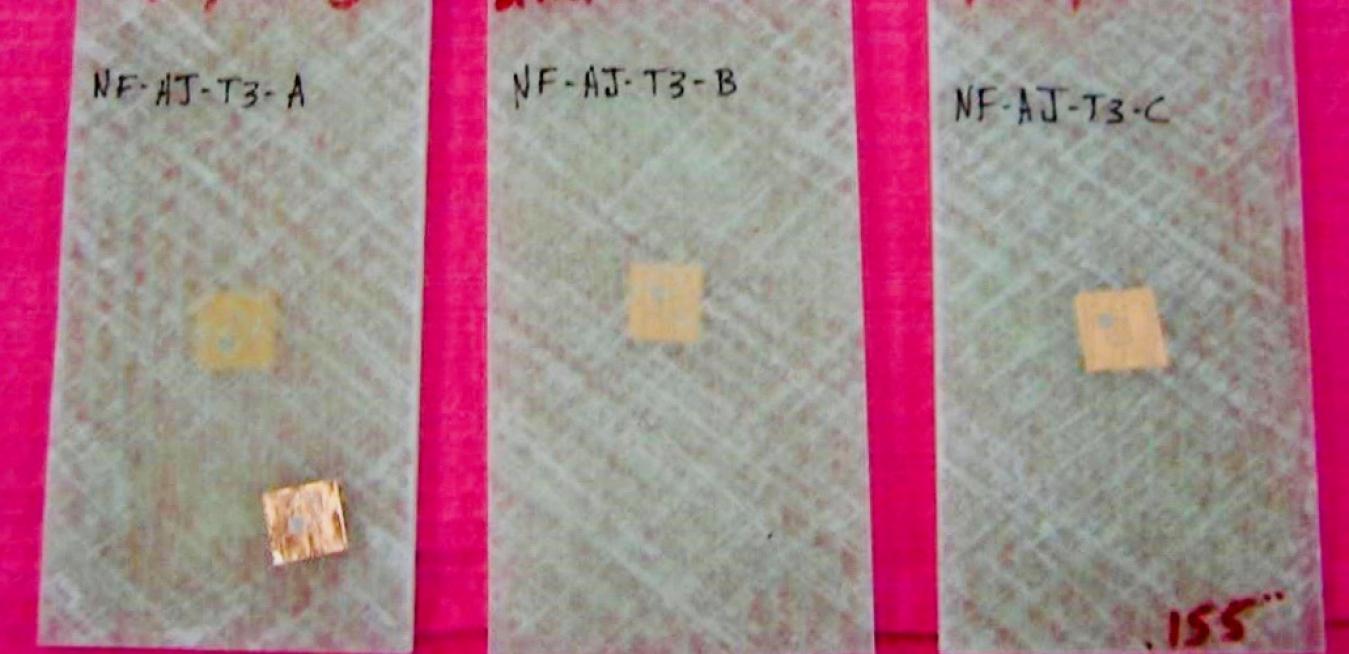
Tiny Sensors Will Keep Tabs On Wind Turbine Blades
Athletes have been wearing electronics that can bend and flex to the shape of their bodies, revealing how many miles they’ve logged, current heart rate and how much energy they burned. They can use the data to constantly improve their training and understand more about how their bodies are reacting to different training regiments.
The research is particularly relevant because wind energy costs for producers have dropped substantially since 2010, in large part because longer turbine blades allow operators to capture more wind energy. GE Renewable Energy subsidiary LM Wind Power unit, for instance, makes the world’s longest blade that measures 107 meters, and blades across the industry have been getting longer at an average of about 3 meters a year, says Nath.
The team, which previously worked on bendable and stretchable sensors that can be attached to clothing, is pursuing this work with a grant from NextFlex, a consortium of companies, universities and the U.S. Department of Defense. The work could expand beyond manufacturing and help service crews keep an eye on wind turbines in the field.
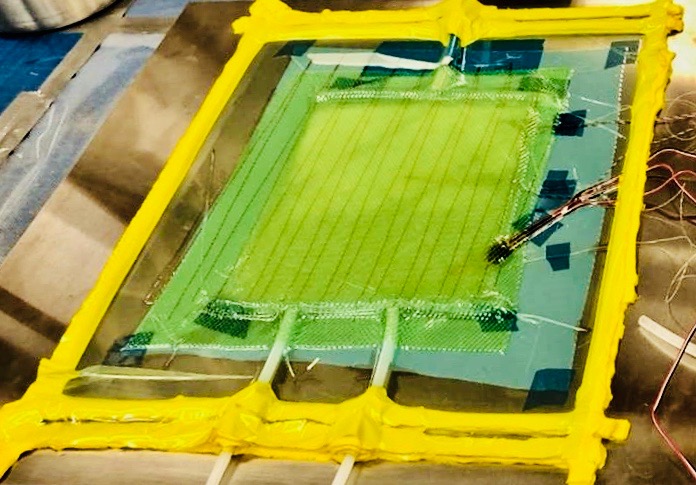
Top image: Three samples showing embedded sensors at different depths of glass fiber composite structures that would be read wirelessly. Above: Test bench for monitoring the resin infusion process in a glass fiber composite. Images credit: GE Research.
That’s more difficult than it sounds. Blades are typically made from a composite of glass fibers, carbon and wood, and sealed together with a resin. Embedding sensors that match the blade’s curve during manufacturing can help engineers know the blade has properly cured and potentially speed up production. But such sensors must be designed as not to interfere with or negatively impact the blade in which they are embedded.
Stoffel’s group will be testing various sensor materials throughout this year with the goal of having a prototype by 2021. “It’s both an electromagnetic challenge and a mechanical, materials challenge,” says Stoffel.
In the future, researchers expect to be able to develop sensors that can transmit information from blades on a working turbine, allowing owners to spot possible problems early, much more regularly and reduce costs of maintenance. Today, operators inspect for signs of wear by sending workers up turbine platforms, using telescopes from the ground or drones from the air. None of these approaches are perfect. “We want a sensor that is wireless and it can be interrogated from two to 10 meters away without interfering with the other things that go around it,” Stoffel says.
Wind turbine blades could be just the start. Partners working with GE on the blade sensor project include researchers from Binghamton University and Georgia Tech as well as helicopter manufacturer Sikorsky. Together they will explore embedded sensors on airframe structures to study damage and wear from flight. If all goes well, these efforts will be just the start of flexible, embedded sensors throughout different kinds of industrial machines.
Says Stoffel: “There are a lot of applications and, in our case, this will help us pursue industrial wearables, where we’re sensing the performance of large rotating machines, or engines or any number of other tools.”