The company has spent the last several years developing technologies ranging from data analysis to machine monitoring and preventive maintenance to get 3D printing ready for production prime time. “We need to have systems in place that anticipate a failure before it happens,” says Steve Rengers, principal engineer for additive manufacturing at GE Aviation. “This has not been done before.”
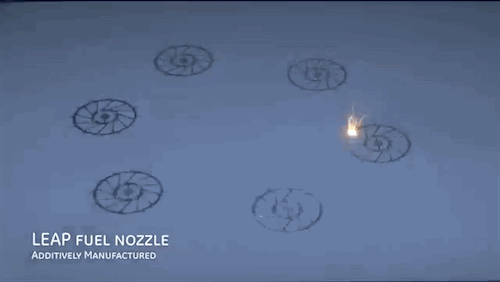
A high power laser prints fuel nozzles from layers of fine metal powder. Top Image: The nozzles supply fuel to the jet engine and keep it lit. Here a GEnx engine is powering through a water ingestion test.
When it opens in 2015, the Auburn plant will be producing fuel nozzles for the next-generation LEAP jet engine, which was developed by CFM International, a joint venture between France’s Snecma (Safran) and GE Aviation.
The engine has benefited from GE’s $1 billion annual investment in jet propulsion R&D. Each engine will have nearly twenty 3D-printed fuel nozzles, as well as fan blades made from fourth-generation carbon-fiber composite blades and a hot section that includes parts from groundbreaking ceramic matrix composites (CMCs).
The nozzles are five times more durable than the previous model. 3D printing allowed engineers to design them as one part rather than 20 individual parts, reducing the number of brazes and welds that would have been necessary using traditional methods.
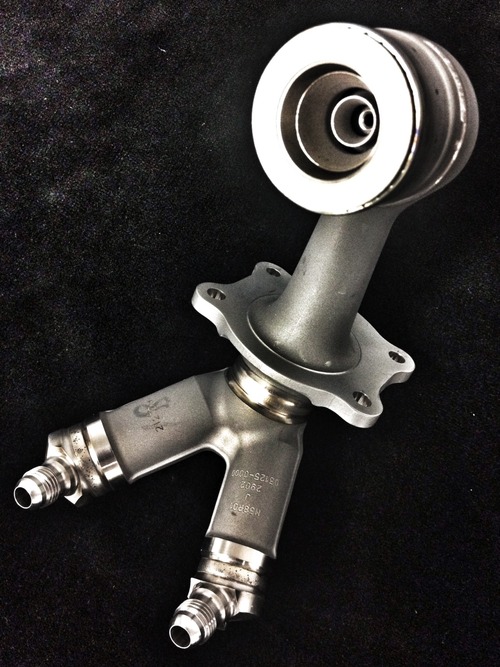
The 3D-printed nozzles are five times more durable than the previous model.
GE is also developing 3D-printed parts for the GE9X engine, the world’s largest jet engine which will be installed on the next-generation Boeing 777X long-haul passenger jet.
With more than 6,700 orders from 20 countries, adding up to nearly $96 billion (U.S. list price), the LEAP is GE Aviation’s best-selling engine in history. Over the weekend at the Farnborough Airshow, EasyJet and American Airlines placed new multi-billion orders for the engines. Emirates airlines signed a services agreement for the GE9X valued at $13 billion.
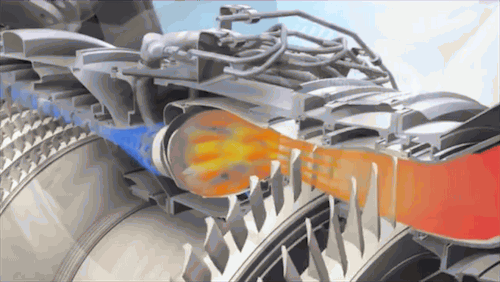
The nozzles pipe fuel into the jet engine’s combustion chamber.
The new plant will be using a 3D-printing method called direct metal laser melting (DMLM). The method grows parts directly from a 3D computer drawing by melting together thin layers of fine metal powder with a high-powered laser.
The machines deposit the powder in layers that are as thin as 20 microns– a fifth of the thickness of a human hair. They generate the whole part by adding one layer on top of another- sort of like rebuilding a loaf of bread from individual slices and joining them together.
Monitoring quality throughout the entire build process is crucial, since it can take days or weeks to print a part, depending on its complexity. “We are really pushing the envelope on process monitoring,” Rengers says. “By using sensors to collect data, we can determine the mechanical properties of the part.”
The $50 million plant will operate several additive manufacturing machines simultaneously to meet demand, while employing approximately 300 workers at full capacity.
Subscribe to GE Reports to follow news from the Farnborough airshow.