The problem starts small, with one tiny deviation: a thrust bearing in the steam turbine of a combined cycle power plant changes position, shifting the turbine's axial displacement from -0.29 mm to -0.445mm1. That's a shift equal to the width of a single eyelash and still within safe operating parameters. But steam turbines are subject to extreme temperatures, pressures, and forces and even tiny changes can have large consequences.
Without intervention, the thrust bearing continues to move, and the axial displacement continues to shift. By the time an alarm sounds in the plant control center and the deviation is discovered, the damage has already been done: The turbine will have to be taken offline. Parts will need to be replaced. Power production will be lost. Total cost for the power producer? $245,000.
The Catch
Luckily for the power producer, this is a bill they won't have to pay. The actual thrust bearing never moved, and the turbine's axial displacement never shifted. Engineers at GE Digital's Industrial Managed Services center in Paris observed the deviation using the steam turbine's digital twin—a software representation of the real asset. By running historical and real-time data generated by the actual steam turbine through its digital twin, GE engineers were able to make what they call a “catch”—to predict a future problem, and help the customer take steps to make sure it never happens.
In the words of GE Digital's Afo Adéyè, “This type of catch can be extremely disruptive to operations and fortunately we have the tools to help avoid them.” As Industrial Managed Services Director, Europe, Afo leads a team of 15 engineers as they use predictive analytics to assist customers across the continent. They're part of GE's global effort to monitor the health of thousands of industrial assets in real time, in order to predict failures before they take place. Worldwide, 90 engineers with a combined 1,110 years of experience watch over an average of 7,589 assets every day. These engineers—many of whom have worked for the power producers they now serve—are experts in the management of over 230 equipment types, including both GE and non-GE assets.
All that expertise and years of experience couldn't be put to use without digital twins. Digital twins are at the heart of “everything we do today,” says Afo. “Predictive analytics without the digital twin is not really possible.” But the “catch” detailed above represents the culmination of a months-long process spearheaded by Afo and his team; in order to understand the central role of the digital twin, you have to go back to the beginning.
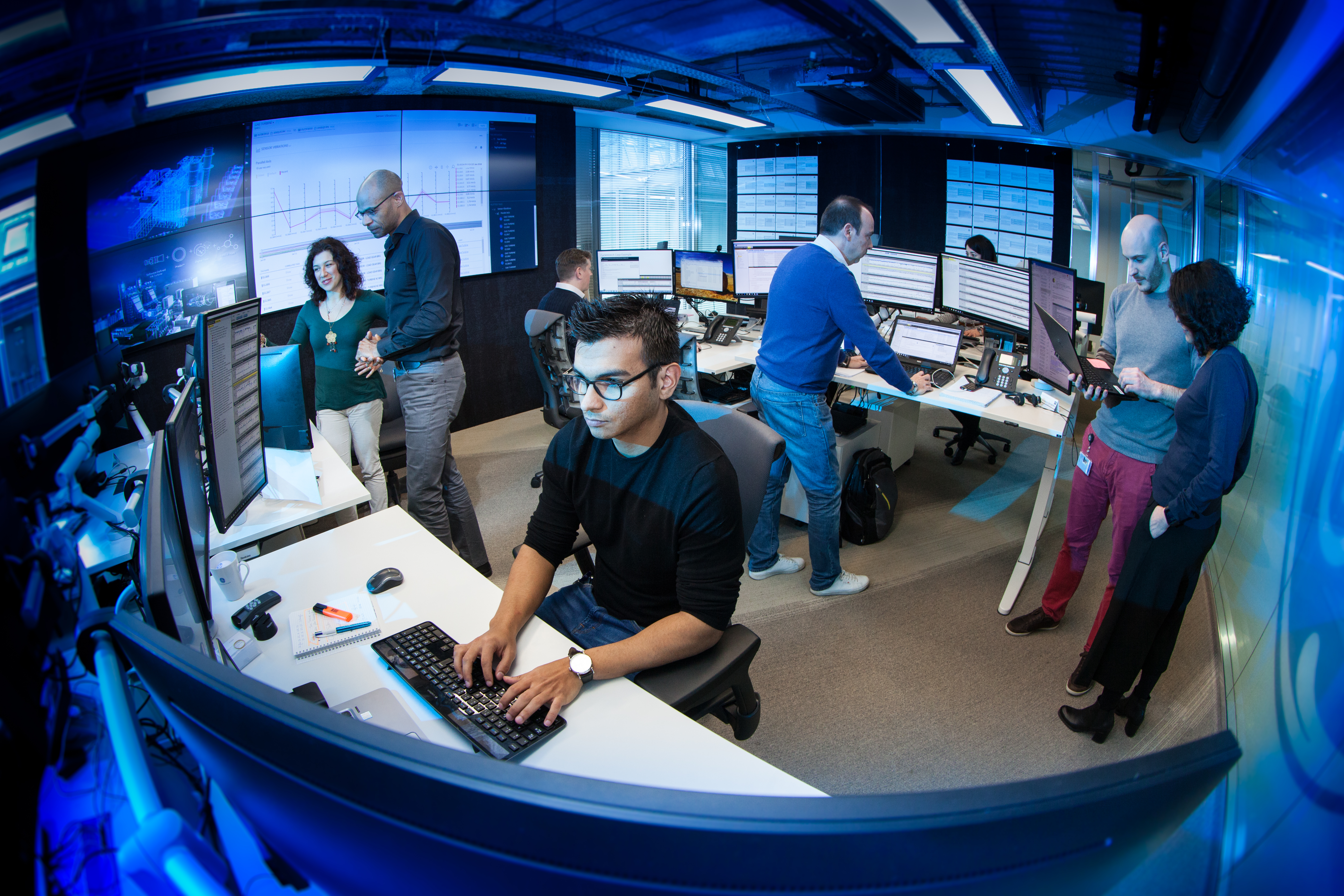
Making the Digital Transformation
Before GE's digital twin was deployed, faults such as these had become unacceptable. In the case of this power plant, the operating team knew that their competitors had already invested in digital solutions that allowed them to see faults before they happened and take proactive actions. They knew there was a solution, but they couldn't see the way forward.
So they went to Afo and GE's Industrial Managed Services team. The team's proposal: Let us take a look at the asset that's giving you trouble. Even though the power producer hadn't taken steps to digitize their assets, the assets themselves—like most industrial equipment built in the last two decades—had been generating and sometimes storing data all along. Afo's team was able to run a year's worth of historical data through an existing digital twin of the asset. Given that GE's cloud contains 1.2 million digital twins across 300,000 different asset types, it's no surprise they already had the twin available. The result: they correctly diagnosed the deviations that led to the fault that convinced the power producer to contact GE—along with a number of other deviations that might lead to future faults.
“Once assets are connected to the cloud, they're constantly updated using real-time data...”
The power producer was sold—and so Afo's team set to work, figuring out how they could generate the most value for their new customer. Within three months, they'd selected which assets to monitor. (The service is scalable, meaning a power producer can choose to monitor a single piece of equipment an individual plant, or every asset they manage.) Once they made sure the correct sensors were in place, Afo's team established a secure link to GE's cloud, and mapped those sensors to their digital twins.
Once assets are connected to the cloud, they're constantly updated using real-time data, as well as new fault patterns observed in similar assets connected to GE's network. When that data indicates a deviation from expected behavior, it's entered into a weekly report that's shared with clients, along with recommended actions. It was one such weekly report that contained the “catch” that saved $245,000.
Looking Toward the Future
“Today, with our digital twins” Afo says, “we can catch more than 80% of existing fault patterns on some equipment.” As more and more assets are brought online and connected to the cloud, that percentage is likely to increase; as more data is collected and the more fault patterns are cataloged, the team's ability to forecast future problems will only improve.
For power producers, predictive knowledge is improving uptime and their ability to deliver reliable, cost-effective power anywhere in the world. For GE, that’s all the more reason to continue innovating. According to Maher Chebbo, Sr Executive & Chief Innovation Officer, GE Power's Digital Energy Solutions, the rationale behind GE's investment in digital twin is simple: “The more projects we do, the more we're learning—the more our digital twins can keep improving and get more and more results.”
Learn more about GE Digital Twin Technology.