Industrial CT technology is similar to the large scanners hospitals use to check for brain problems and other potential medical concerns in the human body, but far more powerful. It has to be in order to look deep into the microstructure of the parts, analyze the shape of the tiny patterns inside, and identify foreign materials and impurities.
GE’s 120-year-old Inspection Technologies’ business was the first company in the world to deploy X-rays in an industrial setting. Now part of Baker Hughes, a GE company, with headquarters in Germany and 700 employees locally, the unit makes radiographic devices and solutions, plus a broad range of ultrasonic, remote visual and eddy current inspection equipment.
Some of the world’s biggest consumer electronics, automotive and aviation manufacturers rely on Inspection Technologies’ offerings to scrutinize their products — smartphone battery casings and car engine pistons, for example — to ensure their integrity before they go to market.
But things are changing. When Henry Ford first tried his Model T assembly line in 1913, the assemblers were adding the nuts and bolts of the cars’ chassis as it was winched across the floor with a rope. The line started a manufacturing revolution, but now many experts believe that 3D printing is poised to disrupt design and production in a similar way. Quality assurance will be crucial. “They print them, and we inspect them,”says Holger Laubenthal, CEO of Inspection Technologies. “There’s an important role for us to play in terms of adoption rate. I think this is a great opportunity to drive the additive revolution.”
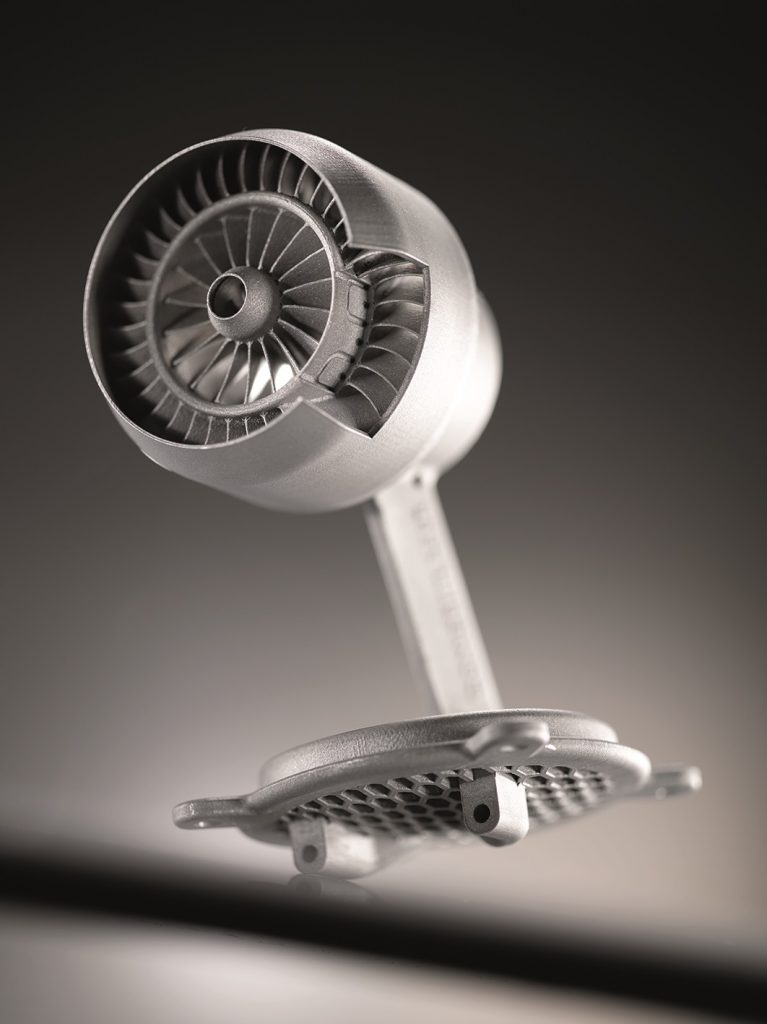
3D printing — or additive layer manufacturing — is a relatively new technology that allows engineers to design products that were expensive or impossible to make before. Some large, complex parts can take several days to complete, and manufacturers need to be confident that when it’s all done, they do not contain any flaws. This is important because GE is using 3D printing not just for prototyping but also for mass production. For example, GE Aviation is already printing complex fuel nozzles for jet engines, and the unit recently started testing the GE Catalyst, a turboprop engine with more than a third of its part printed from metal.
With traditional manufacturing techniques, companies might only inspect one in a thousand products, says Jason Oliver, who heads GE Additive, the GE unit that makes 3D printers, and the metal powders used for printing. (It also runs the learning centers where GE partners and customers can test and master additive manufacturing technologies.) He says that with 3D printing, “there needs to be massive amounts of inspection to make sure everyone is comfortable.” That’s especially the case with aviation, “where the level of requirement for inspection for parts is off the charts,” he says.
Oliver says that non-destructive inspections, like those involving CT, will help people trust 3D printing. “It’s a lot further along than people think,” Oliver says. “Talk to the average person about an airplane with 3D-printed parts, and people will say, ‘What?’” When clients walk into a GE additive facility, many can’t believe what they’re seeing, Oliver adds. “They have no idea that metal additive printing has come that far.”