Doctors, nurses and other essential workers have been playing a key part in the battle against the coronavirus epidemic. But computer scientists are also pitching in.
For instance, researchers are using the world’s fastest computer — Summit, at Tennessee’s Oak Ridge National Laboratory (ORNL) — to rapidly simulate how different biological compounds might help prevent infection with COVID-19. It’s part of a project called the COVID-19 High Performance Computing Consortium, which has made more than 25 supercomputers in the U.S. available for free to scientists studying potential treatments or vaccines for the coronavirus. That kind of computational firepower lets them take their scientific work and essentially supercharge it, as ORNL’s Jeremy Smith told NPR: “We could get these calculations done in one day on the supercomputer, whereas a normal computer, it would take a month.”
When they’re not busy solving the world’s most pressing challenges, though, supercomputers are ... well, actually, they’re busy solving pressing problems tied to other global challenges, like climate change. GE is no stranger to the power of supercomputers, and in recent years it’s found increasingly creative ways to harness their computational muscle to help design more efficient airplane engines, faster manufacturing processes and better wind farms — and more.
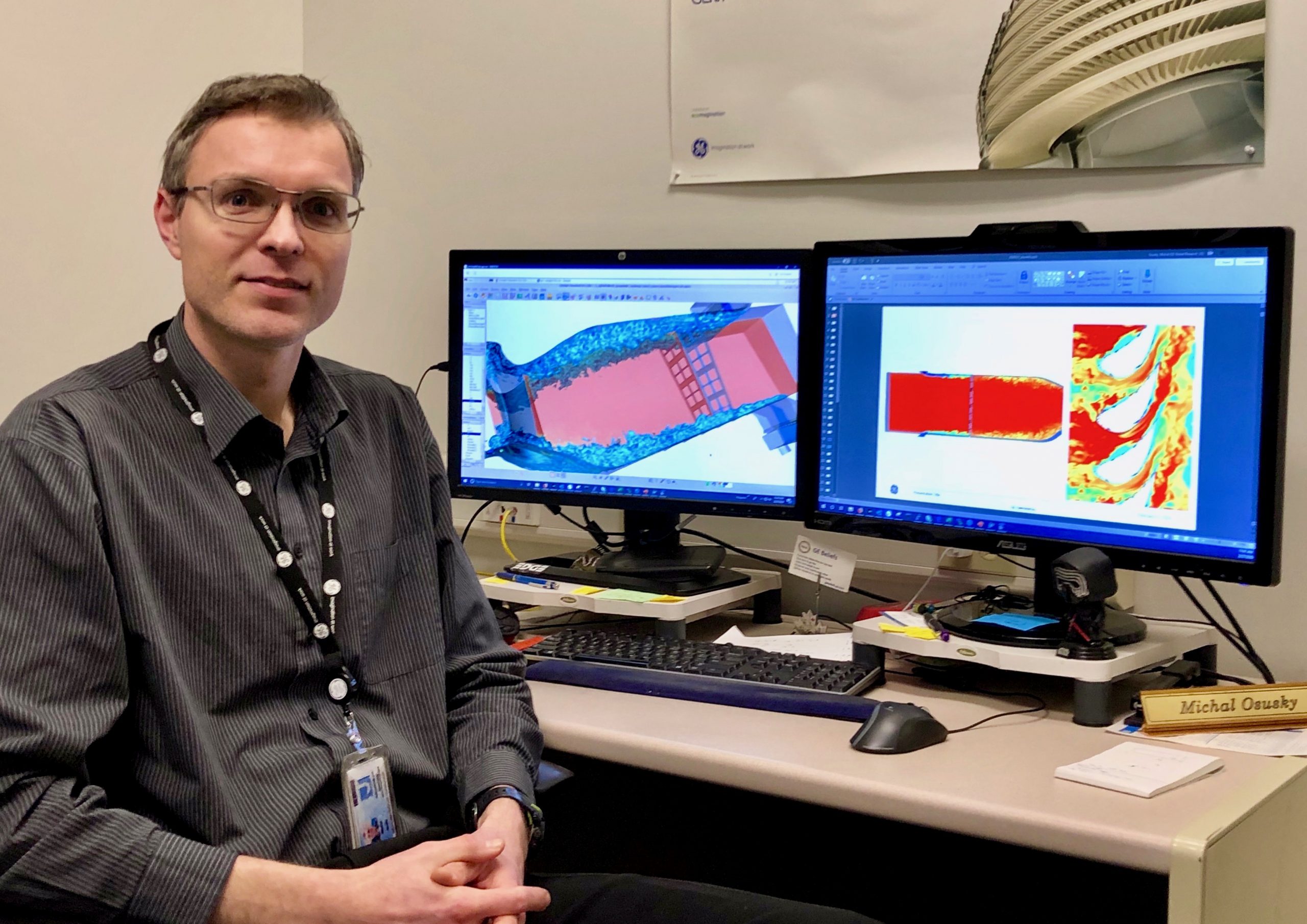
How hot do jet engines run? So hot that scientists have turned to supercomputers to figure out how to cool them without sacrificing the energy the heat can deliver. GE Research recently partnered with the U.S. Department of Energy’s Office of Science on a project that will use the ORNL Summit supercomputer to build simulations of how heat flows inside jet engines, as well as gas turbines inside power plants.
Ordinary computing systems can’t process data fast enough to give an accurate picture of what goes on inside an engine — scientists have previously been forced to rely on estimates. “It opens up a whole new area of predictions we never would have been able to do,” says Michal Osusky, a lead thermosciences engineer at GE Research who is leading a project to improve high-pressure turbine designs. Even tiny improvements in turbine efficiency can translate to reduced fuel consumption and emissions — so even small efficiency gains realized by this project could mean big savings for the global oil and gas industry.
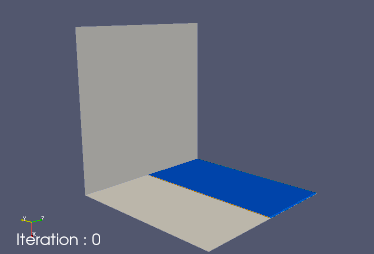
Though 3D printing is still a growing industry, it’s been swiftly embraced by engineers and designers. Also known as additive manufacturing, it is playing a vital role everywhere from aviation to healthcare to art. Precisely because it’s a novel technology, though, there are still problems to be solved. “Additive manufacturing is just a completely different way of manufacturing parts,” says GE Research’s Brent Brunell. “We’re finding that while we have capabilities to build features we never had before, we don’t yet have the design tools to take advantage.” That’s why the U.S. Department of Energy (DOE) Advanced Research Projects Agency has granted $1.3 million to a consortium of GE, ORNL and Xerox’s PARC subsidiary to develop computing tools and standards to accelerate 3D-printing design and prototype development.
GE and its partners intend to compile a database of materials that could be used in 3D printing. They’ll also analyze other attributes like printing speed to find ways to improve prototype quality. The Summit supercomputer, which can complete 200,000 trillion calculations per second, will track the temperatures, stresses and pressures that individual parts experience when being printed. The consortium believes it can cut the timeline for designing and validating 3D-printed components by two-thirds.
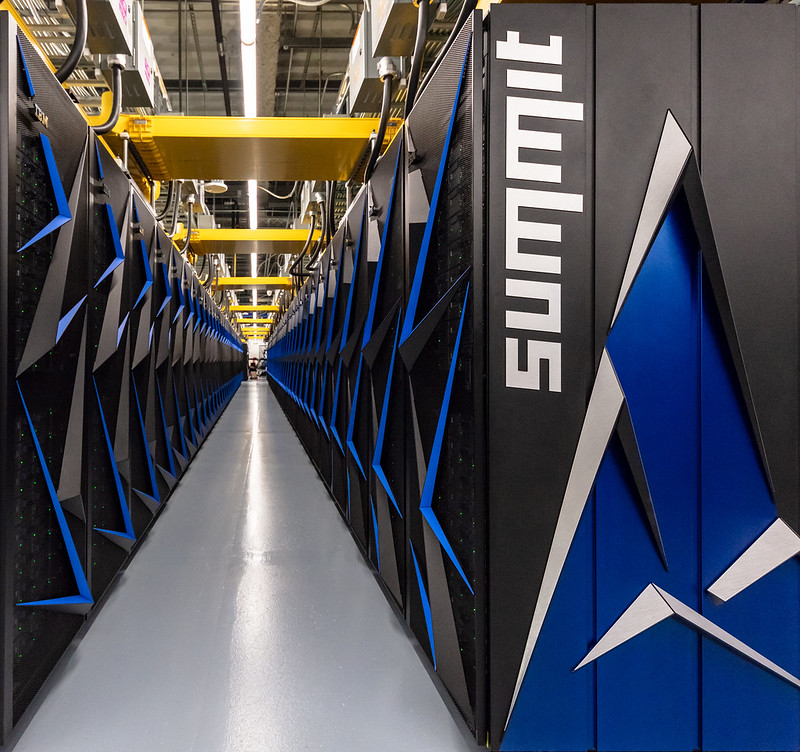
That Summit supercomputer stays busy: In October, GE Additive signed a five-year agreement with ORNL on a project to improve the precision and consistency of 3D-printed products. Many industrial 3D printers build parts by fusing together thin layers of metal power with a laser and even a tiny error could lead to a big problem. The partnership joins two crucial forms of expertise. One is GE’s experience in developing real-world products with 3D-printed parts — like the GE9X and Catalyst turboprop engines, which include a number of 3D-printed parts.
Many 3D printers are outfitted with sensors that collect loads of data from each build that can be analyzed to make the process more efficient and dependable. Traditional computers might take a long time to crunch those numbers; not so the mighty Summit. “That kind of computing power unlocks some exciting potential. We can analyze the data much, much faster,” says Brian Thompson, GE Additive’s manager of design and development.
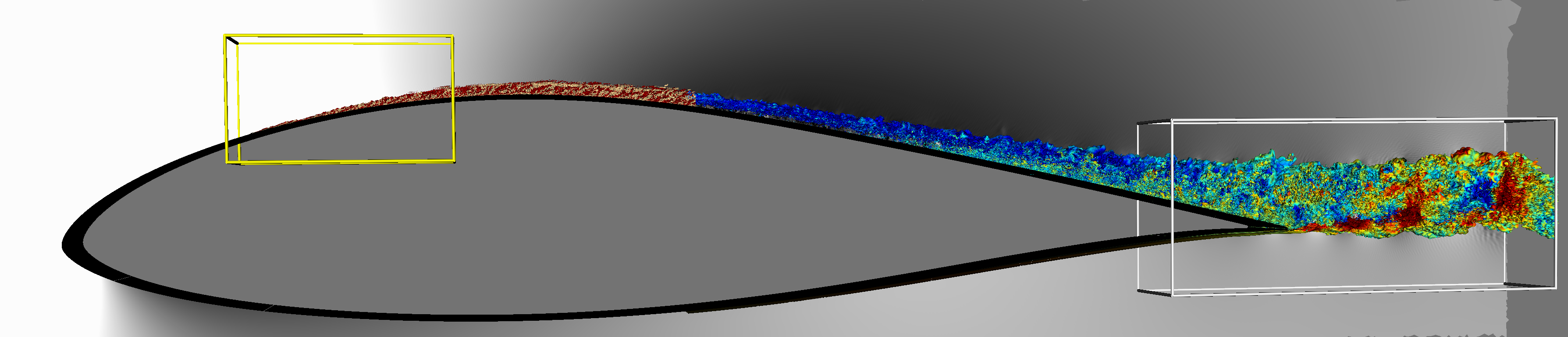
Last year, a paper in the journal Nature Energy found that today’s giant wind turbines can cause decreases in wind speeds that can be felt by other turbines as far as 30 miles away. This so-called wind wake is siphoning away energy and revenue from neighboring wind farms.
So how can wind farms be sure they’re getting the most breeze for their buck? That’s the challenge for engineers at GE Research, who use supercomputers to create detailed models of how wind moves in the real world. With the help of the Cray XC supercomputer, they can precisely model airflow across an entire 5,000-acre territory, which could lead to more efficient turbine and wind farm placement — allowing for a more bountiful energy harvest for less cost.
Making Artificial Intelligence Curious
Intelligence is a virtue, but it’s best when it comes with a little humility. This is true for artificial intelligence as well as for humans. An AI model might constantly adjust a wind turbine, for instance, in order to crank out as much energy as possible at any given moment. But what happens when an unexpected gust goes outside the parameters the model was programmed with? Colin Parris and his team at GE Research have been developing ways to make AI “humble,” so it can, for instance, switch to safe mode when faced with unexpected conditions.
The next step is making AI “curious”: teaching it to identify which data variables are missing and to seek them out. In turn, that can help GE engineers write better software models. One of the most effective ways to sharpen predictive skills is to connect to high-powered simulators, like those at the Energy Department’s Argonne National Laboratory. Parris and his team have partnered with Argonne to gain access to its labs and supercomputers, seeking out more detailed and accurate weather simulations. The more simulations GE Research can run, the smarter the models become. The end goal? Incremental gains in energy production at wind farms — which can add up to big savings.