Câu chuyện chuyển mình của nhà máy GE Gas Power tại Greenville, Nam Carolina trong suốt nửa thế kỷ qua được khắc họa rõ nét và đầy đủ, cho thấy vai trò của một yếu tố quan trọng mang tính chất “chìa khóa”, giúp nhà máy vượt khỏi thăng trầm của thời kỳ suy thoái theo chu kỳ: Tinh gọn.
Trong suốt nửa thế kỷ, nhà máy GE Gas Power tại Greenville, Nam Carolina đã trải qua nhiều thăng trầm. Thành phố Greenville được xây dựng vào khoảng 200 năm trước bên bờ sông Reedy, là điểm nóng của ngành dệt và một biểu tượng của lòng hiếu khách phương Nam. Đến những năm 1970, trung tâm của thành phố chuyển mình: nhà máy, khách sạn đóng cửa, tiếng của những chiếc xe điện ồn ào chở người đi mua sắm và gặp gỡ bàn chuyện kinh doanh cũng ngưng lại.
Khoảng 20 năm trước, các nhà lãnh đạo và doanh nghiệp bắt đầu bắt tay với nhau để thực hiện một cuộc cải tổ. Họ phá con đường cao tốc bốn làn bắc ngang qua thác nước biểu tượng của thành phố, xây một công viên xinh đẹp bên bờ sông và khôi phục vẻ quyến rũ đang dần mất đi của khu vực trung tâm.
Tuy nhiên, năm 2017, ngay khi tạp chí Vogue viết về sự phát triển của nền ẩm thực tại thành phố đang hồi sinh này, những công nhân tại nhà máy GE – nằm cách trung tâm thành phố không xa – nhận thấy họ sắp phải đối mặt với sự suy thoái của chính mình.
Chu kỳ suy thoái
Năm 1969, GE chuyển tới Greenville để sản xuất các dòng tuabin khổng lồ cho nhà máy điện sử dụng khí đốt tự nhiên. Đây là một công việc đòi hỏi chuyên môn cao. Những cỗ máy này có thể nặng tới 500 tấn và các bộ phận bên trong của chúng được lắp tỉ mỉ, khớp với nhau như những chiếc bánh răng trong một chiếc đồng hồ. Năm 2015, nhà máy được mở rộng lên tới hơn 450.000m2, lớn gấp 26 lần sân bóng bầu dục và có khả năng tạo ra hơn 420 MW điện – đủ để phục vụ hơn 400.000 hộ gia đình ở Mỹ. Tuabin được sử dụng trong nhà máy là dòng tuabin mới nhất của GE, đã từng được công nhận trong sách kỷ lục Guinness về hiệu suất vào năm 2016.
Tuy nhiên, đến năm 2017, khi nhu cầu sản xuất tuabin mới dần ít đi, nhiều bộ phận linh kiện với giá trị lên đến hàng triệu USD trong nhà máy bị tồn lại và không được sử dụng đến. Jon Boucher, người chịu trách nhiệm cho các dự án và sáng kiến đặc biệt của GE Gas Power cho biết: “Chúng tôi đáng lẽ có thể đầu tư nhiều hơn cho việc cải tiến với khoản chi phí đó”.
Suy thoái theo chu kỳ xuất hiện, ảnh hưởng đến thị trường và gây tổn thất cho GE. Trước đó, công ty đã mất hơn 1,5 năm để tạo ra chiếc tuabin khí phá kỷ lục thế giới mang tên HA. Vì nhiều bộ phận của tuabin này quá đặc biệt, chỉ có rất ít nhà máy trên thế giới có thể sản xuất được nên GE đã phải đặt trước từ rất lâu. ”Việc đặt vật liệu và linh kiện sẽ dựa trên dự đoán về số đơn đặt hàng tuabin nhưng thực tế không như kỳ vọng. Chúng tôi tích trữ linh kiện trong khi nhu cầu đối với chúng không có thật trong bối cảnh thị trường bị suy thoái” – Boucher cho biết. Vì nhiều bộ phận được sản xuất dựa trên yêu cầu cụ thể của khách hàng nên chúng không thể tái sử dụng được nữa và dần trở nên lỗi thời. “Điều này làm chúng tôi tổn thất rất lớn,” Boucher nói.
Không lãng phí
Khái niệm tinh gọn được ra đời dựa trên ý tưởng của W. Edwards Deming – một kỹ sư và nhà thống kê người Mỹ. Lý thuyết của ông đã được áp dụng rộng rãi ở Nhật Bản thời kỳ hậu chiến, nơi kỹ sư Toyota Taiichi Ohno áp dụng “tinh gọn” để thiết lập Hệ thống sản xuất Toyota huyền thoại. Hệ thống này là một bộ các nguyên tắc quản lý, tập trung vào việc thúc đẩy hiệu quả sản xuất, giảm thiểu chất thải và tạo ra nhiều giá trị với ít nguồn lực hơn. Từ đó, khái niệm này đi đến mọi nơi trên thế giới và được Viện Công nghệ Massachusetts do nhà nghiên cứu James Womack dẫn đầu đặt tên là quản trị tinh gọn. James Womack cũng là tác giả của “The Machine That Changed the World” – cuốn sách được coi là kinh thánh của phong trào này.
Tinh gọn cũng trở thành trọng tâm trong vòng quay của GE. “Khi chúng ta tiến lên phía trước với sự biến đổi tinh gọn của mình, chúng ta không chỉ đơn giản là đánh dấu vào một ô trống” Larry Culp, Chủ tịch và CEO của GE đã viết trong một lá thư gửi các cổ đông vào tháng Hai. “Chúng ta đang thay đổi cách điều hành GE, kinh doanh bằng kinh doanh, hàng ngày, và từ dưới lên”
Tinh gọn nhà máy
Công xưởng sản xuất chính là nơi Boucher và nhóm của ông bắt đầu quá trình tinh gọn. Trong những năm qua, khi nhà máy Greenville phát triển, GE liên tục bổ sung các máy móc mới, đặt chúng ở bất cứ nơi nào còn trống. Boucher nhớ lại: “Chúng không hề được sắp xếp, có những máy móc không được sử dụng đến cứ nằm mãi một chỗ”. Và kết quả là, các nhà quản lý lập thời gian biểu làm việc dựa trên các máy móc đang hoạt động mà không hề xem xét đến khoảng cách cần di chuyển giữa mỗi công đoạn.
Khi tìm giải pháp, họ nhận thấy một bộ phận quan trọng là cánh tuabin đang nằm chất đống bên cạnh máy móc, gây cản trở quy trình. Lúc này, chúng có tỉ lệ tồn kho và phế liệu cao nhất trong nhà máy.
Cánh tuabin là một lưỡi thép phức tạp được lắp trong phần nóng của tuabin và làm quay rotor. Những người công nhân ở Greenville định hình nó bằng các khuôn đúc công nghệ cao có giá trị hàng chục ngàn USD và được đặt làm riêng. Nhiệt độ bên trong tuabin có thể vượt qua điểm nóng chảy của kim loại nên các bộ phận này phải được phủ lớp phủ chuyên dụng và trải qua các quy trình bảo vệ phức tạp khác.
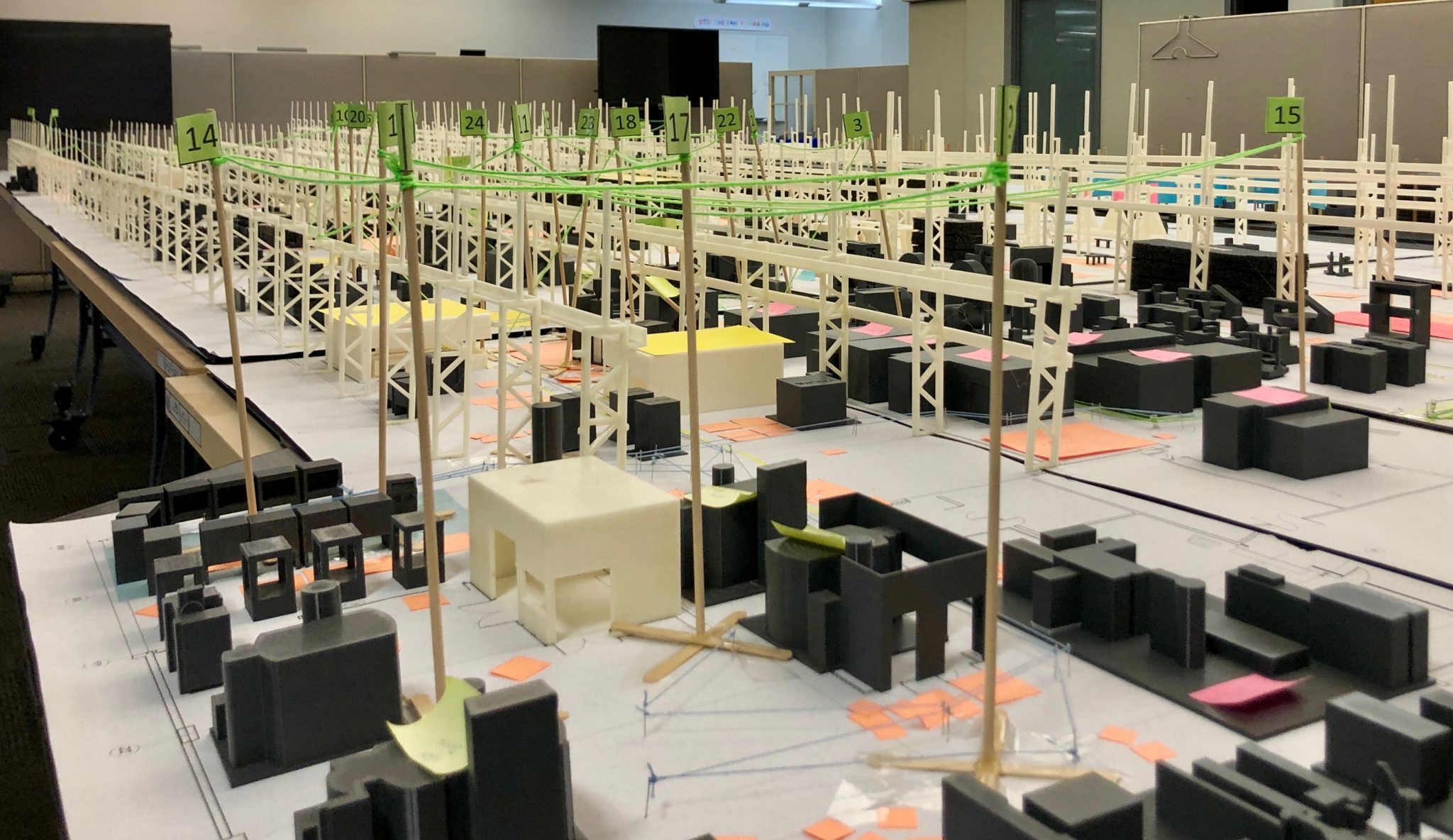
Hình trên: Một mô hình với tỷ lệ 1:60 của nhà máy khổng lồ với các máy móc được in 3D từ nhựa đen. Các bó sợi được dùng để vạch ra hành trình của các cánh tuabin được vận chuyển trong nhà máy, cố định nó bằng những cái đinh. Jon Boucher nói: “Trông nó như một bát mì spaghetti lớn. Ai nấy cũng đều ngạc nhiên khi nhìn vào mô hình. Rồi họ nhận ra: đến lúc phải thay đổi”. Nguồn ảnh: Tomas Kellner, GE Reports.
Dây chuyền mẫu
Boucher và đội ngũ lãnh đạo của Greenville chuyển đến một tòa nhà hành chính và sử dụng một phần của một tầng lớn được để trống. Họ mang theo vài chục chiếc bàn gấp và xếp chúng lại với nhau để xây dựng nền tảng cho mô hình tỷ lệ 1:60 của nhà máy hoàn chỉnh. Các mô hình máy móc thu nhỏ được in 3D từ nhựa đen. Tiếp theo, họ lấy các bó sợi để vạch ra hành trình của các cánh tuabin được vận chuyển trong nhà máy và cố định nó bằng những cái đinh.
Từ mô hình, họ thấy những sợi dây chăng một cách lộn xộn không kiểm soát quanh nhà máy và lặp đi lặp lại nhiều lần. Nhóm nghiên cứu tính toán rằng cánh tuabin cần di chuyển tổng cộng hơn 4,8km xunh quanh nhà máy mới hoàn tất quá trình gia công trong thời gian 85 ngày. Boucher nhớ lại: “Trông nó như một bát mì spaghetti lớn. Ai nấy cũng đều ngạc nhiên khi nhìn vào mô hình. Rồi họ nhận ra: đã đến lúc phải thay đổi”.
Không dừng lại ở đó, nhóm cũng phát hiện ra rằng những người vận hành máy phải nâng từng cánh tuabin với cân nặng lên tới vài pound và được gắn lỏng lẻo một cái chân vịt hơn 200 lần trước khi nó được hoàn thành. Việc này khiến cho mọi thứ bị chậm lại.
Từng bước tinh gọn
Boucher và các cộng sự tiến hành gỡ rối cho “bát mì spaghetti” bằng cách xây dựng sơ đồ chuỗi giá trị cho cánh tuabin. Boucher giải thích: “Công cụ quản trị tinh gọn này cho phép bạn biết được cần thêm giá trị vào đâu và liệu bạn có lãng phí gì trong hệ thống không. Nó thực sự đã cho chúng tôi cái nhìn toàn cảnh về những gì cần làm và những cơ hội đang có”.
Điều dễ thấy nhất là những chiếc cánh tuabin di chuyển qua nhà máy một cách thất thường, chất đống và gây nghẽn ở các giai đoạn sản xuất khác nhau. “Chúng tôi có hàng ngàn bộ phận trong nhà máy, được xếp dọc quanh các máy móc”, Boucher cho hay.
Để các dây chuyền quạt tuabin chạy không bị cản trở, nhóm quyết định tinh gọn các cụm máy móc đang bày ra chật kín sàn xưởng sản xuất. Trong mô hình dây chuyền mới, các máy đa năng bị loại bỏ, thay thế vào đó là các máy móc chuyên dụng nhỏ hơn. Kết quả là công nhân không thể bỏ máy hỏng để sang làm trên máy khác mà bắt buộc phải khắc phục vấn đề. Boucher chia sẻ: “Mục đích của dây chuyền này là nhìn được rõ ràng các vấn đề cần sửa chữa. Đây là một chức năng bắt buộc. Khi bạn có một dây chuyền, mọi hoạt động sẽ tuân theo quy trình từ A đến B đến C theo quy định, không ngừng nghỉ và không lộn xộn”.
Tiếp đó, họ xác định tốc độ của dòng vận chuyển trong dây chuyền – thuật ngữ tinh gọn gọi là “thời gian tối đa”, tức khoảng thời gian cần thiết để hoàn thành mỗi bước. Đây được xem như là “nhịp tim” của dây chuyền. Nếu nhịp độ chậm đi hoặc dừng lại, người vận hành sẽ dễ dàng nhận biết dây chuyền đang gặp vấn đề nào đó.
Cách tiếp cận này có thể giúp giảm đáng kể lượng phế liệu và hàng tồn kho. “Trước đây, chúng tôi có thể sản xuất hàng chục, đôi khi hàng trăm bộ phận mà chúng gặp phải cùng một vấn đề. Hiện tại, điều này đã được khắc phục. Chúng tôi phải luôn đảm bảo rằng mọi thứ được thực hiện đúng quy trình. Nếu có phần nào có lỗi, dây chuyền phải ngừng lại và được sửa chữa. Có dây chuyền, hàng tồn giữa các quá trình đã được loại bỏ” Boucher cho biết thêm.
(còn tiếp)