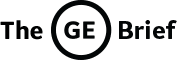
May 7, 2019
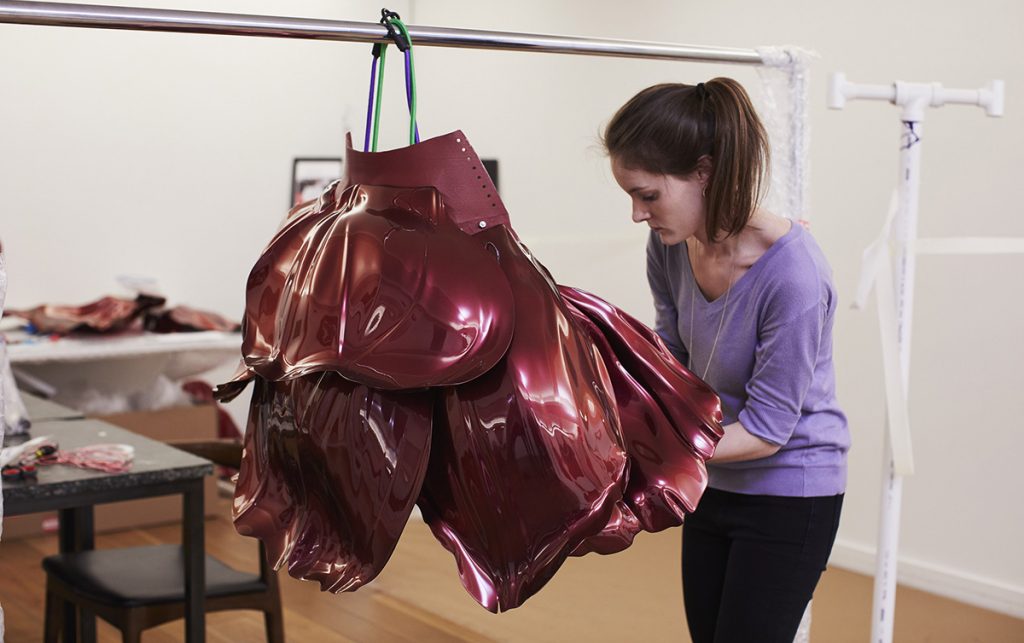
HIGH-TECH MEETS HIGH FASHION
A rose by any other name might smell as sweet, but it’s hard to imagine one looking any cooler than the rose-shaped gown worn by supermodel Jourdan Dunn at last night’s Met Gala. Shiny as a new Ferrari, the petals of the dress featured complex layers of folds and swirls. Italian taffeta, French silk chiffon? Even better: North Carolina plastic. The gown’s 21 plastic petals were 3D-printed outside Raleigh by Protolabs, and the titanium cage holding them together was 3D-printed at GE’s Additive Technology Center in Cincinnati. It was just one piece from a collection of 3D-printed garments created by fashion designer Zac Posen for the Met Gala. The pieces nudged 3D printing from heavy industry to high fashion.
Days of design and roses: To realize his concepts, Posen worked with engineers at GE Additive and its manufacturing partner Protolabs, which specializes in plastic and metal additive prototypes. When they’re not prepping for the fashion event of the season, GE Additive and Protolabs use 3D-printing technology to produce industrial components ranging from jet engines to gas turbines — the same flexibility that enabled them to create complex high-fashion garments helps them produce bespoke parts that the engineers of yesterday couldn’t have dreamed of. (Examples? Just keep reading.) Posen’s dreamy shapes “require very different modeling techniques,” said GE Additive’s Sarah Watson. “The beauty of additive is that it enables designers to quickly and efficiently create parts with this level of complexity.”
Over nearly six months, the designs moved from concept to 3D-printed reality. Learn more here about the garments’ journey to the Met Gala.
3D PRINTING ON A WHOLE NEW PLANE
How do you make blades for the world’s largest jet engine? Layer by hair-thin layer — or at least that’s how it’s done by Avio Aero, a GE Aviation company that makes parts for the massive GE9X engine, designed for Boeing’s next-generation 777X plane. Nestled into the rolling hills of Northern Italy’s Po Valley, Avio Aero’s Cameri operation uses electron beams to weld together millions of grains of fine powdered metal to create some of the jet engine’s most durable parts. Cameri, one of the world’s largest 3D-printing factories, just got even bigger — with an expanded footprint that will allow the plant to turn out 60,000 turbine blades a year by 2023.
The new Italian stallion: To produce the arm-sized engine blades, Cameri gets a leg up from a wonder material called titanium aluminide, or TiAl. Jet designers love TiAl because it’s light and strong — but until 3D printing became a realistic option, manufacturing with the material was difficult. Now 3D printers built by Arcam, a company GE acquired in 2016 and folded into its GE Additive business, make relatively easy work of it, welding the material at temperatures up to 1,000 degrees Celsius following a software blueprint designed by GE engineers. All of this and other innovations means it improves fuel efficiency by 10% over the GE90 engine, which powers most current 777 planes.
The GE9X engine had its maiden flight in March, with deliveries to airlines expected to begin next year. Learn more here.
NOT JUST HOT AIR
True power comes to those who ... can chill a bit. At least that’s the idea behind heat exchangers in power plants. They’re used to capture energy flowing from the primary gas turbine and transfer it to a secondary turbine power loop to generate yet more electricity. The process cools the primary exhaust flow with a “working fluid,” like the antifreeze in a car. The problem is that, with conventional materials and manufacturing methods, heat exchanger components overheat at less than 1,200 degrees Fahrenheit, limiting the amount of additional energy that can be extracted. So Peter deBock and his team at GE Research took a page from Mother Nature’s playbook, using a 3D printer to create a new heat exchanger that mimics the human lungs — “the ultimate heat exchanger,” says deBock. By copying the lungs’ ingenious highway of capillaries, which expose hot blood to cool air, scientists generated more energy more efficiently.
Fizz and chill: They also changed their coolant of choice from steam to CO2 (the stuff that gives fizziness to soda and champagne). At the right temperature and pressure, CO2 becomes supercritical, acquiring the density of liquid but flowing more like a gas — and able to hold an enormous amount of heat energy. As a result, a power generator using CO2 as a medium can be 10 times smaller and more efficient than one that uses steam. It also requires fewer parts. These innovations caught the eye of ARPA-E, the U.S. Department of Energy’s advanced research arm. In April, ARPA-E awarded GE a $2.5 million, 2.5-year grant to develop a 50-kilowatt demonstration heat exchanger using its new design.
Time to pop open some bubbly? Click here to find out what else goes into building a lung-shaped, 3D-printed heat exchanger.
COOLEST THINGS ON EARTH ?
1. The Carmen Sandiego Of Microscopes
Researchers designed a 3D-printed digital microscope that’s “small and robust” enough to be used anywhere in the world — potentially a boon to health workers looking to diagnose disease in remote areas.
2. Spaceburgers
A Russian biotech lab is spearheading the 3D printing of living tissue aboard the International Space Station, in hopes of helping scientists learn about the health impacts of long-term space travel. Another thing astronauts will need for a long trip through the cosmos? 3D-printed meat, which the lab plans to start producing later this year.
3. It’s Good To Be King Louie
Lonely long-distance astronauts might also need a hug from time to time — and they might be able to turn to King Louie, a soft, inflatable robot designed by engineers at Brigham Young University. In space he’ll be easy to store, if you let his air out; here on Earth, Louie represents the “soft robotics” technology researchers have been designing for use in the home.
Read more about this week’s Coolest Things on Earth here.
— QUOTE OF THE DAY —
“They would tell us things like, ‘It needs more movement and energy!’ We had to learn how to interpret this in CAD.”
— Sarah Watson, design engineer at GE Additive consulting arm AddWorks
Quote: GE Reports. Image: Patrick Fraser.
ENJOY THIS NEWSLETTER?
Please send it to your friends and let them know they can subscribe here.