When complete, the 5.3-158 will produce 5.3 megawatts of power using a 158-meter jointed blade rotor, the first of its kind, manufactured by GE Renewable Energy's LM business unit. Part of GE's Cypress on-shore wind platform, the 5.3-158 can power approximately 5,000 households, and represents a 50% increase in annual energy production over GE's 3MW wind turbines.
In order to understand what sets the 5.3-158 turbine apart, we spoke with GE Renewable Energy's Minesh Shah. Minesh leads a truly global team of engineers responsible for the development, design, and production of the turbine. He explains what makes this new technology so important, the challenges and benefits of managing a team spread across multiple continents, and exactly what it takes to go from product definition to manufacturing in only 18 months.
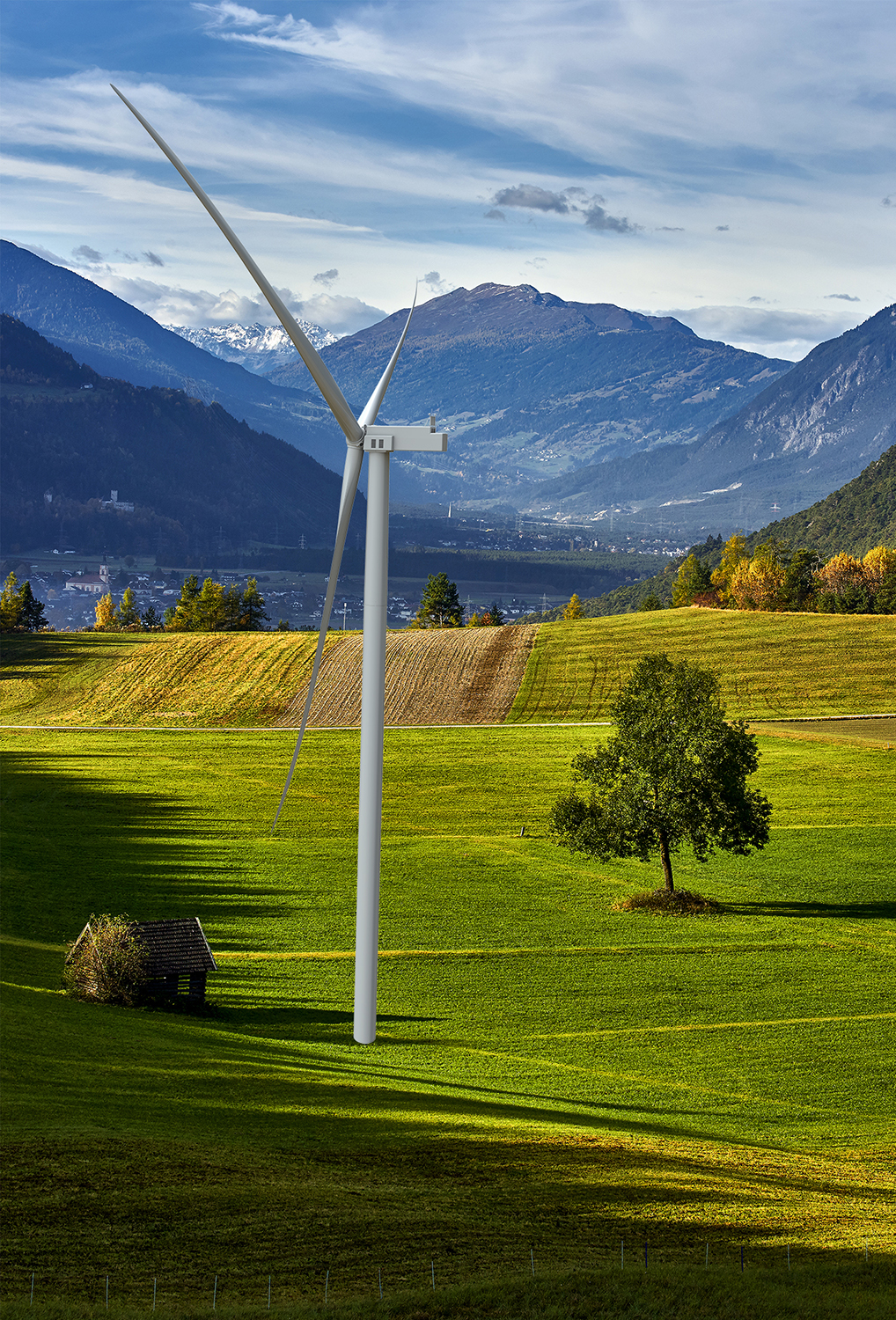
You're almost to the finish line with the 5.3 - 158 Wind Turbine. How did the project begin?
Minesh Shah: When we started looking at the landscape that we were facing, we knew that blade growth was critical. As the blade grows, you're able to capture more wind, and as a result more energy.
The challenge: larger blades are good for capturing energy but they're more expensive and more difficult to move. How do you take a 77 meter blade and make it turn, right? As we looked to balance growth, energy output, and logistics concerns, we started to focus on a single idea: the jointed blade.
How does a jointed blade address all of those concerns?
Minesh Shah: A jointed, two-piece blade allows us to do a number of things a single blade design can't. We can keep pushing blade growth while avoiding the logistical constraints around large single blades. We can install turbines in places we simply couldn't access before. As the technology improves, we can replace and upgrade blades — and change the economics of existing plants for the better. And on the manufacturing side, a two-piece blade allows to use existing factories versus expanding their size to accommodate the longer length. This provides us a chance to leverage our investments in factories more easily.
Was the jointed blade an idea your team had been thinking about for a while?
Minesh Shah: We've been working on this technology for many, many years. It started in '09, '10, with different concepts, but the one that we're using today was developed over the last four and a half, five years. Now we've reached the point where the savings from a logistics point of view versus a single-piece blade really allowed us to bring the jointed blade forward.
So what changed? What made this the right time for the jointed blade?
Minesh Shah: The earlier versions really weren't meeting some critical requirements: you don't want to do any processing in the field, you don't want to adversely impact the installation process, and you don't want really special tooling or skills to be necessary to bring these two pieces together.
The team at the research center [GE's Global Research Center in Niskayuna, New York] really focused on, "How do you solve a very difficult requirements and what's a design approach that can do that?"
You spent a decade working as a researcher at the global research center before moving into management. How did your background influence your approach to the research and development process?
Minesh Shah: We did one thing very different in this particular development effort: we made the research center part of the development team right from the beginning.
That's not how its usually done?
Minesh Shah: So typically in the past, there's a huge effort from the technology development, then there's the hand off. That hand off requires a lot of work to get done to make that technology industrialized or productized for the marketplace. So that hand off slows us down.
As a researcher, your whole mission is really to get your work into a product. That's what an industrial research lab is all about. Having been on the product side over the last ten years allows me to appropriately design the problem statement to give much more clarity to the phenomenal people at the research center. That way, they can know exactly what problems they have to solve in order to deliver the end product.
So how long did it take you to go from defining the product to where you are now, manufacturing the turbine?
Minesh Shah: Accelerating the development and the design cycle allowed us to go from, “Hey, here's the product definition” to being able to put the product in the ground - all in 18 months.
18 months seems like a short turnaround for an undertaking of this scale.
Minesh Shah: We're moving forward for a simple reason: we set an ambitious goal and our teams rose to the challenge. Now we're delivering an innovative two-piece blade design that's going to drive the industry forward.
The assembly of the machine is happening in Germany, and our design teams are in the US and Germany, in Barcelona, China, and India. So when we think about our engineering team, it's very global as is our supply chain, when you look at where the components are produced.
Beyond the researchers at the GRC, where are the rest of your teams located?
Minesh Shah: The assembly of the machine is happening in Germany, and our design teams are in the US and Germany, in Barcelona, China, and India. So when we think about our engineering team, it's very global, as is our supply chain.
What are the benefits of building such a global team?
Minesh Shah: Technology development is really predicated on having the best people. And when you have the opportunity to get great folks and a diversity of thought, a diversity of approaches, from across the globe, it does wonders, both from a product and a capability point of view.
It's important to keep in mind that it's not just the team that's global: the product is really meant for a global base, from Germany to Australia to Brazil and beyond. Working with a global team prepares us for working with a global clientele and supporting the product globally.
How do you ensure that the 5.3-158 and the cypress platform in general meet the varying needs of so many different clients?
Minesh Shah: As a team, we connect with customers and sales folks around the globe early in the process and get their feedback, so we understand how to adapt and adjust our work to their needs.
But you can't simply make a different turbine to fit the needs of each individual customer, correct?
Minesh Shah: The wind space is quite interesting in that it's got a high level of configuration variation to meet all these different needs. So we're not at a point where you're designing a one-off - but it's also not like in the automotive industry where you're producing a million or a consumer product where you're producing millions. So we have this healthy challenge that requires flexibility: we have configuration variation that's clearly there and at the same time we want to try to get to as much standardization as possible, so that we can drive the right competitive cost position.
Electricity is so fundamental to progress - in terms of agriculture, water...so many different facets of life can be changed through just the ability to have energy and electrical generation. The opportunity to do it in a sustainable way is just amazing.
What keeps you motivated as you manage such a complex project
Minesh Shah: Electricity is so fundamental to progress - in terms of agriculture, water...so many different facets of life can be changed through just the ability to have energy and electrical generation. And the opportunity to do it in a sustainable way is just amazing. And when you talk to your kids and say you work on wind turbines, they can get it. Right? Because the connection to what people care about is so tight in the wind space, it's extremely exciting thing to be a part of. It's really cool.
So do your kids think your job is cool?
Minesh Shah: (laughs) The thing with my youngest one is, he knows because I keep telling him, we gotta get the weight of the product down. Every time he'll ask me, "Did you get the weight of the product down?"