More than 60 percent of frequent flyers cite delays among the things about air travel that they find most dismaying. And the bill for such delays? For passengers, the costs are spread around — an extra $25 in parking here, a missed business meeting there. Carriers, meanwhile, pay an estimated $62 per minute in crew, fuel, maintenance and other costs. It adds up. The Federal Aviation Administration and the research group Nextor calculated that such delays cost U.S. passengers and airlines tens of billions of dollars last year.
Most of those costs and all of the annoyance for the passengers on that flight from LaGuardia could have been avoided if the airline had been able to predict that the part was going to fail and prevent it from happening, says Karen Thomas, executive vice president of sales and services for Americas at the data and analytics company Teradata. She says that combining flight analytics and sensor data from engines with customer data, airlines can better manage flight disruptions, not to mention missed connections.
Teradata has now entered into a strategic partnership with GE Aviation to do just that. The two companies will take a stab at analyzing a portion of the growing mountain of commercial aviation data, which is adding around 15 billion terabytes every year — a billion times the size of the Library of Congress. (Just one terabyte of data can hold 200,000 songs or 500 hours of movies.) GE data from 320 million flight-hours alone could open up untold avenues for solving delays and other problems. “Full flight data hasn’t been connected to customer data,” Thomas says. “Now it is, and that can be a game changer for the aviation industry.”
The new partnership will enable airlines to zero in on specific issues, like finding a wing part requiring service more frequently than expected. Software analytics could make it possible to determine which supplier sold the particular parts and where and when they were installed. “It might turn out a supplier had a bad lot, so you only need to check the 24 planes with parts delivered on that specific day to that specific location from that particular supplier,” says Andrew Coleman, chief commercial officer for GE Aviation’s Digital Solutions business. He says problems that might have required months or years to solve now will potentially take hours or even minutes.
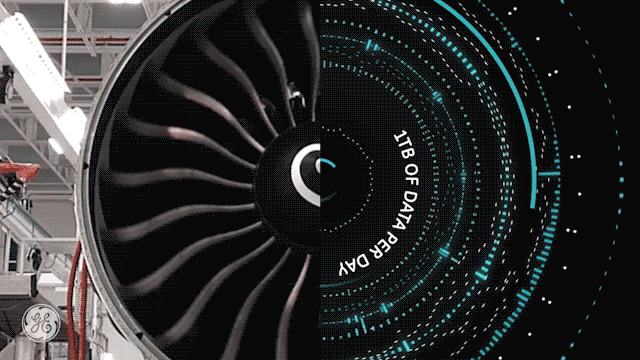