GE's Christine Furtoss explains how additive technologies today are making breakthroughs, from surgical procedures to jet engine parts. In the future, the use of 3-D models in additive manufacturing will go beyond the realm of our imagination.
Imagine the day when we can “Print-On-Demand” real, functional parts for complex machines any time, any place around the world. In other words, imagine that printing a critical part for an engine whenever you want, wherever you want, becomes as simple as printing on a sheet of paper in your inkjet printer. It’s hard to fathom today, but with each day comes news of amazing breakthroughs in additive manufacturing that makes me think this day is closer than we think.In June, additive manufacturing — which uses 3-D models to build materials layer-by-layer — made a big assist for surgeons in the operating room. Using a 3-D printed model of a patient’s cancerous kidney, surgeons were able to achieve a unique view of the tumor’s position that enabled them to remove it while preserving the kidney itself. It’s a powerful example of how 3-D printing is enabling the seemingly un-impossible to be possible.
This year, GE became the first jet engine maker to install 3-D printed fuel nozzles on its newest engine for narrow body aircraft, the CFM LEAP. It’s a critical part that impacts the overall fuel economy of the engine. Just consider that a one percent improvement in fuel efficiency represents billions of dollars in potential savings to the airline industry. With 3-D printing, we were able to design and print parts that could not be made any other way. These CFM LEAP engines have already been through dozens and dozens of test flights with customers like Boeing and Airbus. In other words, this isn’t make-believe. It’s real and having impact today.
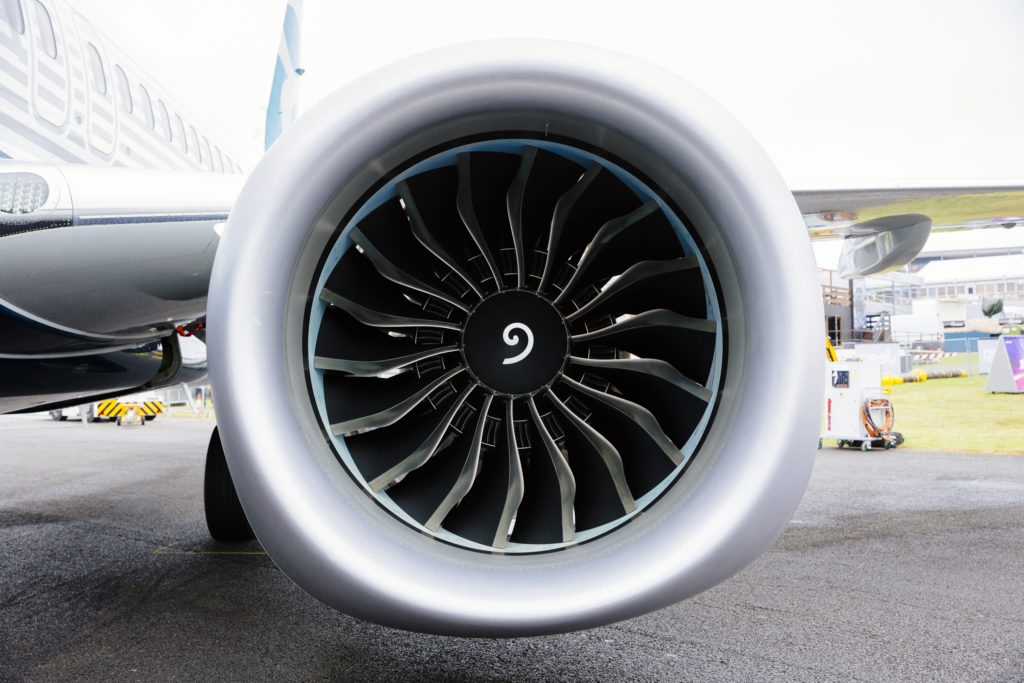
From hospital operating rooms on the ground to commercial air traffic 35,000 feet high, we’re just beginning to experience where additive manufacturing can take industries like aviation, healthcare and energy. Additive technologies have liberated product design constraints like never before, but we believe they can do much more. Additive can change entire supply chains and how parts flow through them. Economic models could be totally disrupted. But doing so will require a new level of commitment and investment to build, scale and innovate our way there.
This week, GE is hosting two important groups at our Research Center in upstate New York that are at the center of driving this revolution. The first is America Makes, which is part of the National Additive Manufacturing Institute in Youngstown, Ohio, and a key part of President Obama’s National Network for Manufacturing Innovation (NNMI). The second is the 3MF Consortium, which is working to bring a standard industry format for the sharing and using of software files in additive manufacturing.
GE is proud to be an industry partner in both groups. When we meet, we’ll be discussing ongoing work but also exploring the keys for additive to take the next big leap from breakthrough moments to full-scale revolution. I believe it really comes down to making technical advances in three key areas: machines, materials and software.
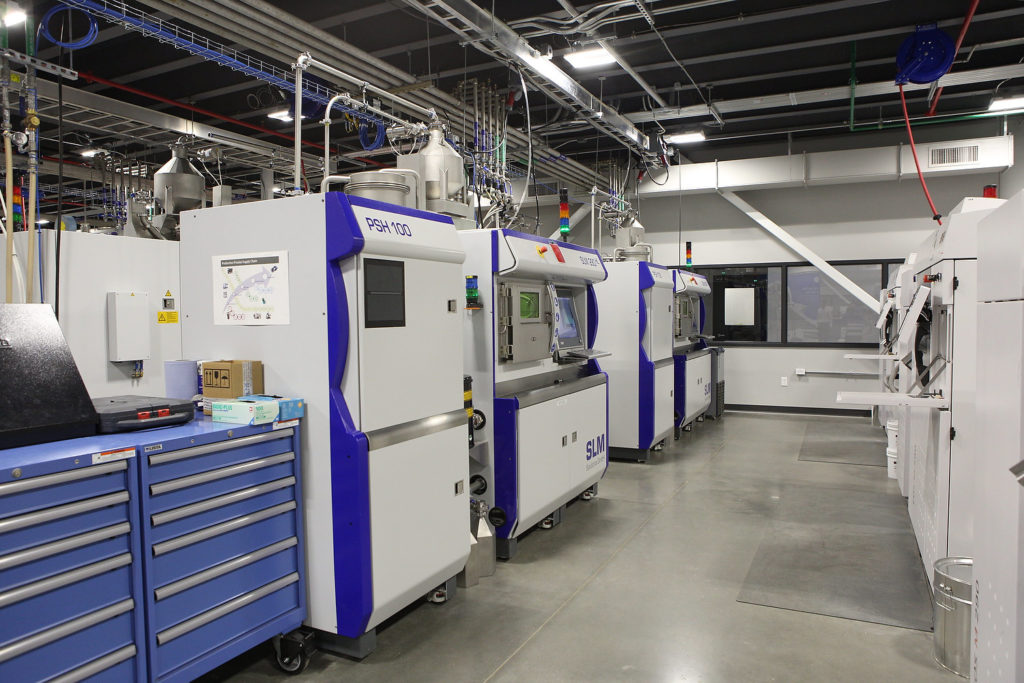
Faster Printers, Bigger Parts
Let’s start with machines. Today, 3-D printing machines are producing parts in reliable, repeatable ways.
In metals, direct metal laser melting (DMLM), or sintering processes, where lasers etch out the shape of a part on a bed of metal powder layer-by layer, are able to make smaller, more complex designs like the fuel nozzle very reliably. We have several DMLM printers on site at our research lab in Niskayuna, New York, as well as at our new $40 million Center for Additive Technology Advancement in Pittsburgh and GE Aviation’s $50 million Additive Manufacturing production facility in Auburn, Alabama.
The key challenges now are enabling machines that can print faster and produce a wider range and more sizes of parts. The limitations with production speed and sizes of parts are preventing more widespread use of additive processes.
A Recipe Book Of New Materials
Along with improving the machines, we also want to expand the availability of materials used to make parts. Today, GE is working with a handful of metal materials in additive processes. In the future, we want to create a database of dozens, even hundreds of new materials. The functionality of materials has always been a big differentiator in product performance, and the use of additive in materials discovery could really exploit that advantage.
To accelerate our understanding, we have created a new Additive Materials Lab at GE Global Research to write the recipe book on 3-D and additive materials.
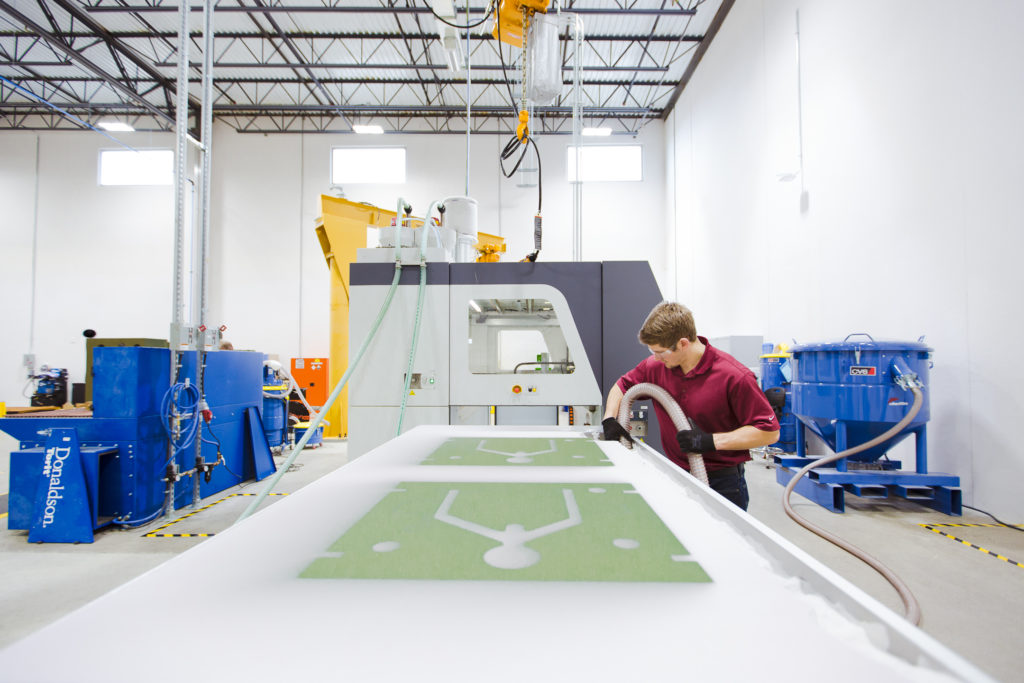
Software A Key Industry Accelerator
Finally, software will be another major accelerant in the development of the additive industry. This will be especially true in the design and development of new components. Many companies like GE have turned to the cloud and open crowdsourcing platforms to accelerate knowledge in this area and create new and better designs. The availability of these platforms through forums such as those sponsored by GrabCAD, NineSigma and others have really opened up who can participate in design and product development and the number of good ideas that can be seen and reviewed.
The digital connections afforded through software also will enhance our ability to bring key additive stakeholders together in a more cohesive ecosystem. This is perhaps the most critical factor in determining how transformative additive could be. We need to develop and grow the ecosystem to truly move additive from these breakout moments to a full-scale revolution.
When we can print complex metal parts “On-Demand” like paper, we’ll know when that day has arrived.
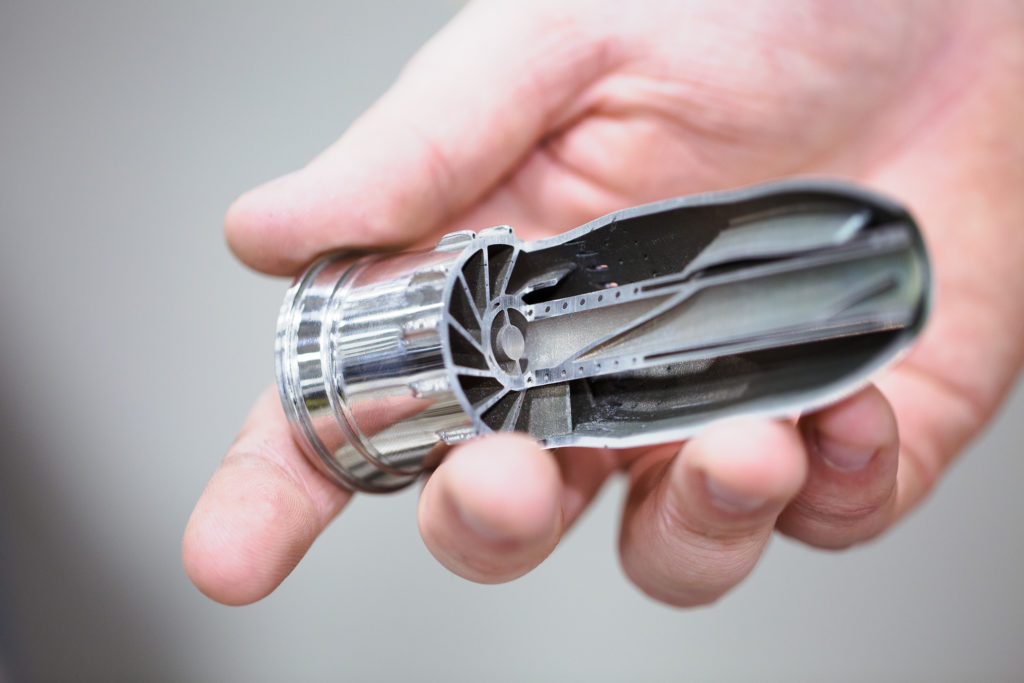
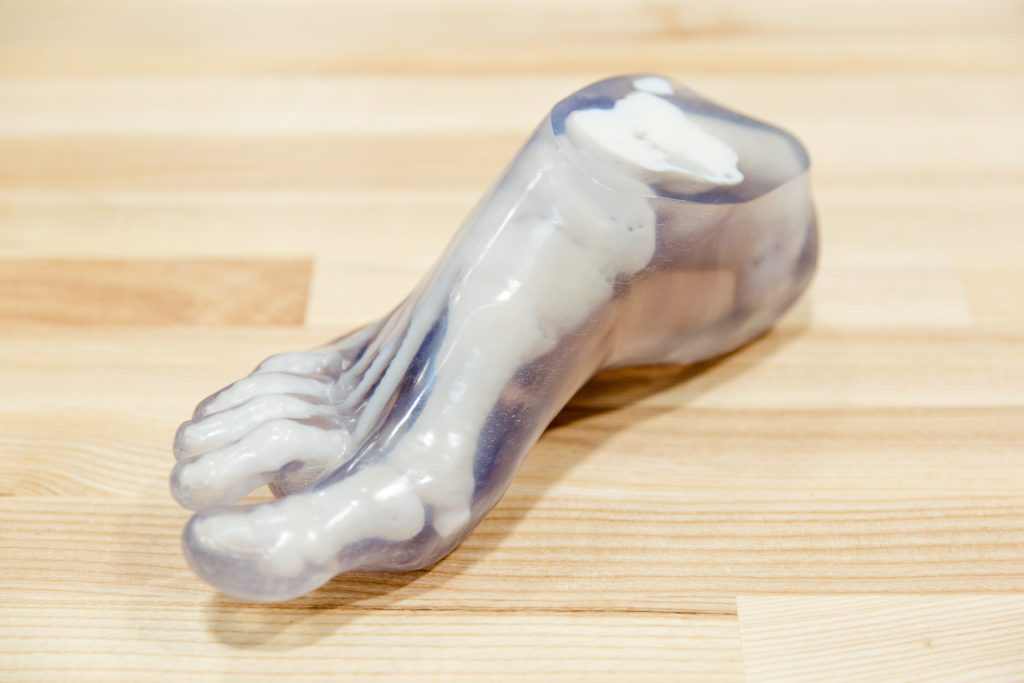
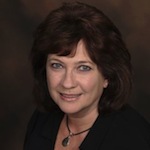
Christine Furstoss is vice president and technical director for manufacturing and materials at GE Global Research.
All views expressed are those of the author.