The plant’s several manufacturing halls — equivalent in size to nearly 21 football fields – strike most first-time visitors as the playrooms of a giant toddler. Massive yellow gantry cranes lift multi-ton rotors and stators gleaming like alien silver sunflowers. They flip them around their axis, and stack them on shafts the diameter and length of tree trunks.
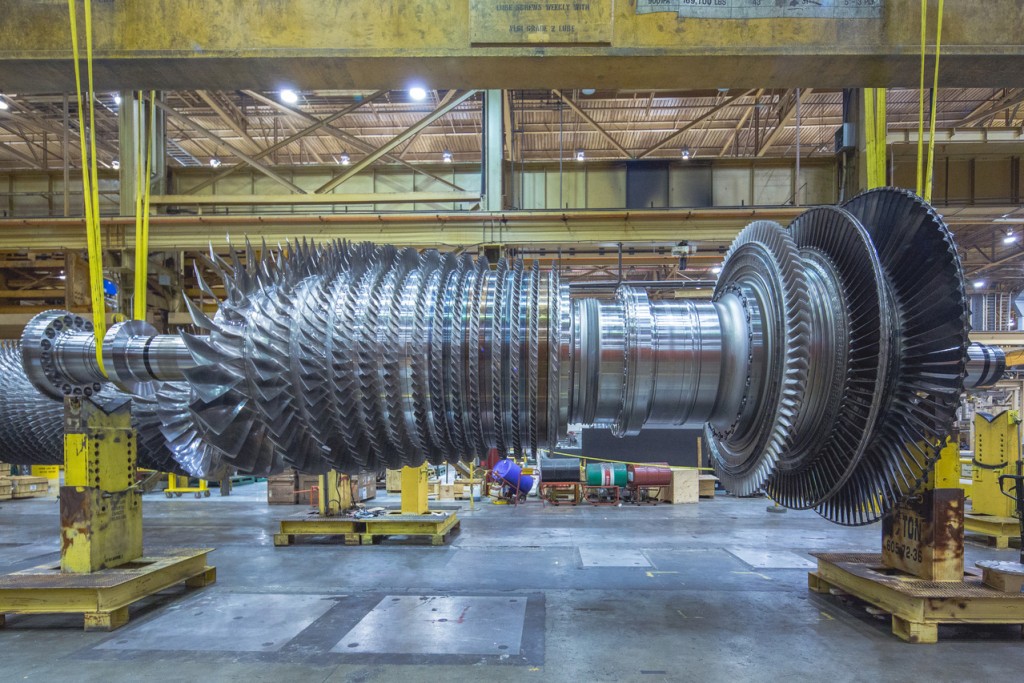
The place smells of high-grade steel and pulses with an industrial symphony of electrical motors cutting in and out. Computer-guided milling machines larger than delivery trucks use jagged cutting heads drenched in white cooling liquid to shape huge turbine wheels.
The plant, which opened in 1968, even has its own railroad spur and also America’s largest train turntable — measured by weight capacity — to move the finished turbines into a unique test stand designed to push turbines to the limit. It can withstand exhaust heated to 1,200 degrees Fahrenheit jetting out of them at 1,100 mph – 10 times faster than the winds of a Category 3 hurricane. There site also has a natural gas plant that supplies the test stand with fuel and allows the turbines to run a full load.
The place also has a 70,000-square-foot research center called Advanced Manufacturing Works. It's replete with 3D printers and powerful lasers. Engineers use them to develop and test parts for next-generation machines like the air-cooled Harriet 9HA turbine — the world’s largest and most efficient gas turbine. Although the facility is strictly off-limits to outsiders, GE Reports recently got a tour. Take a look.
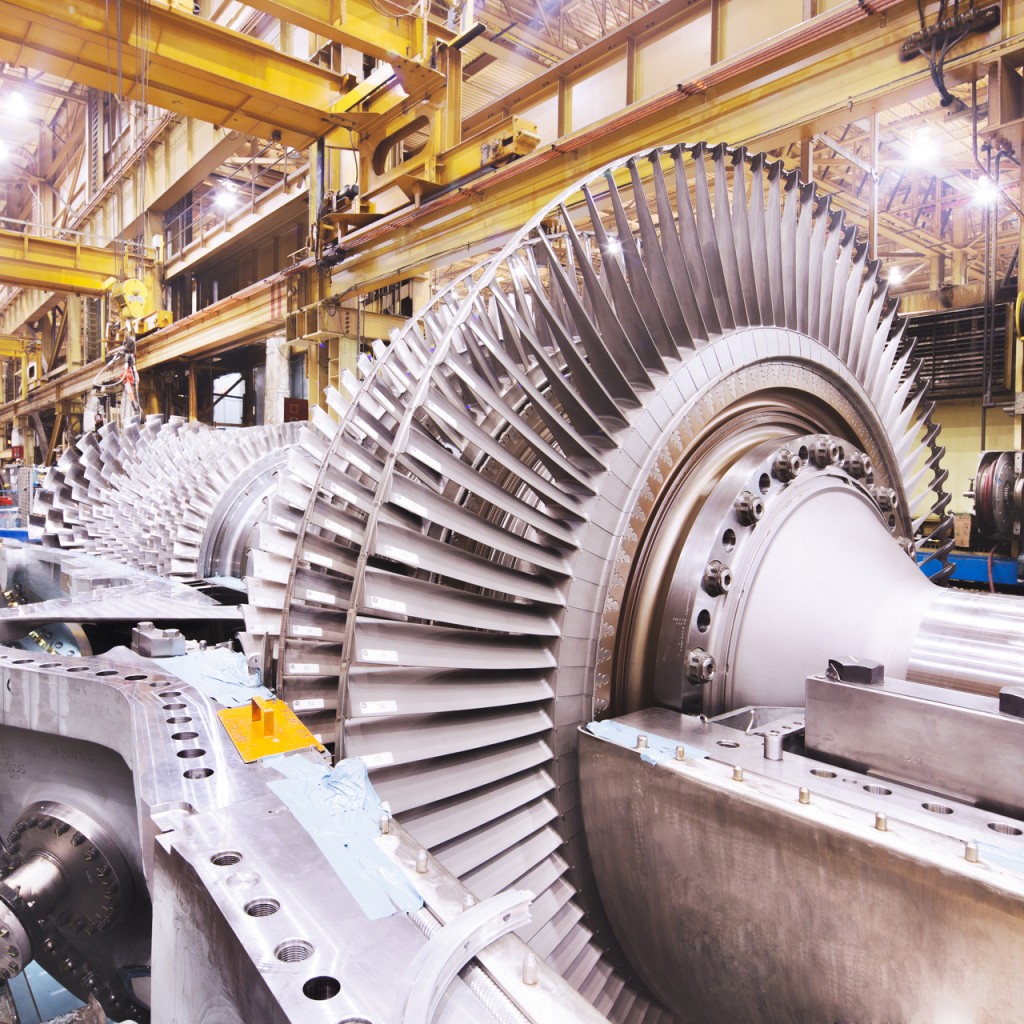
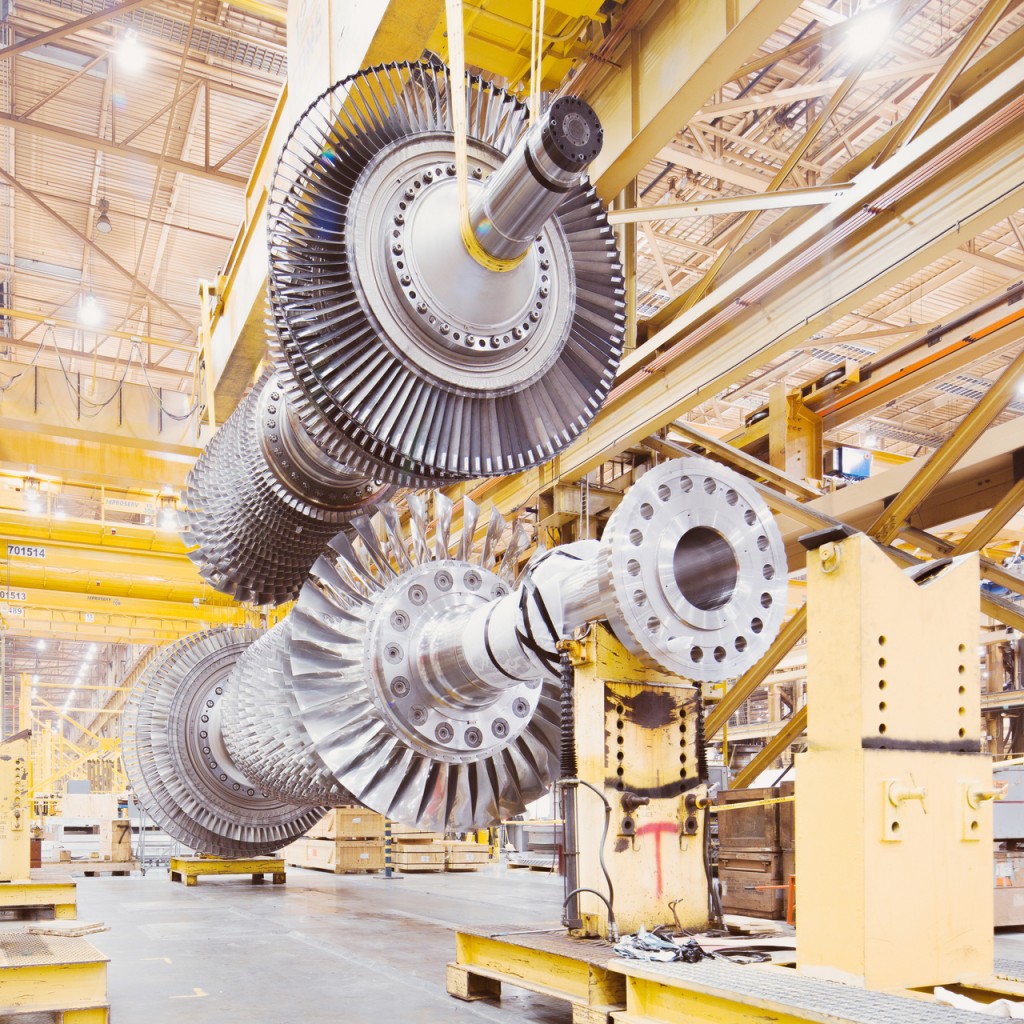
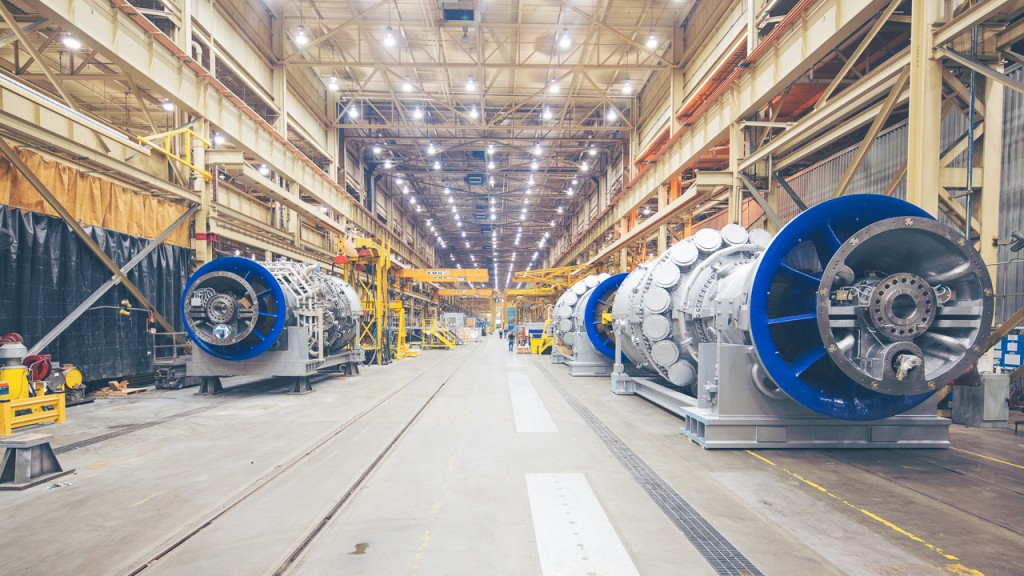
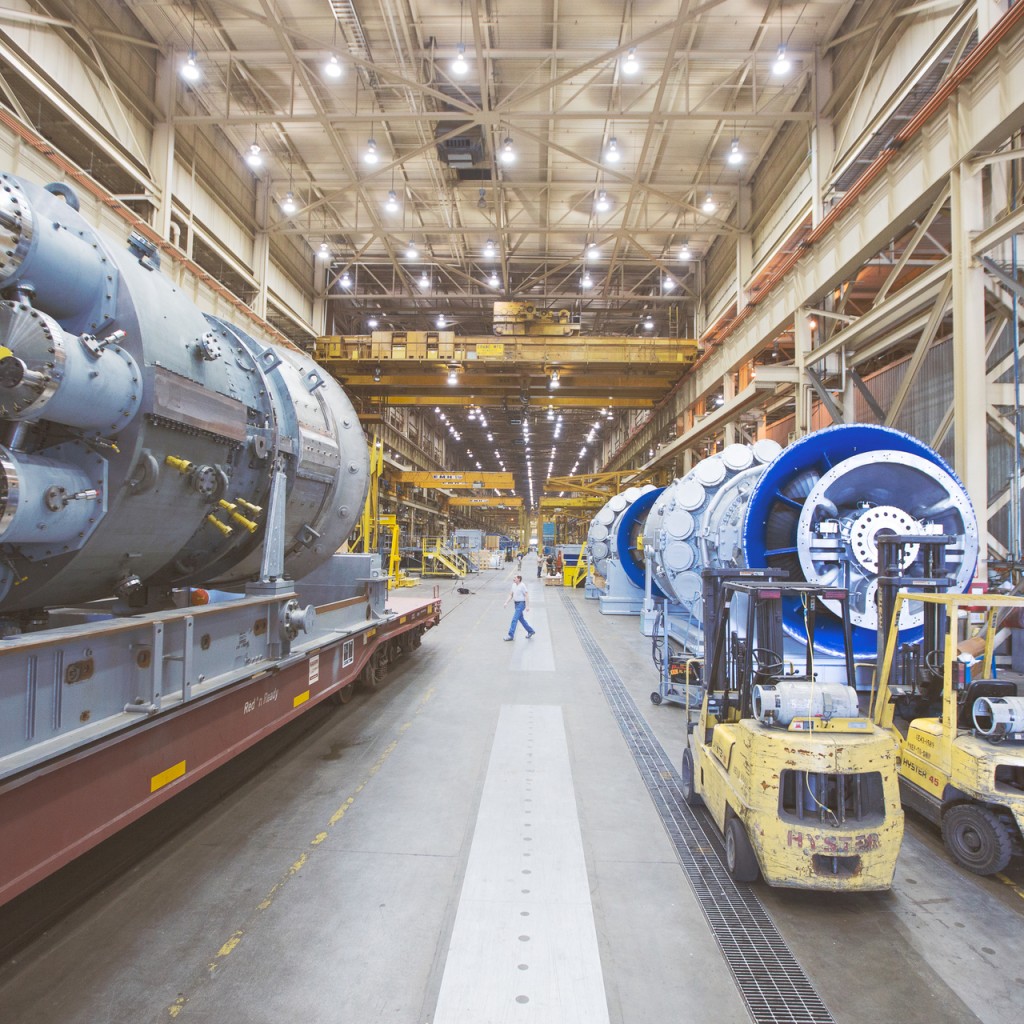
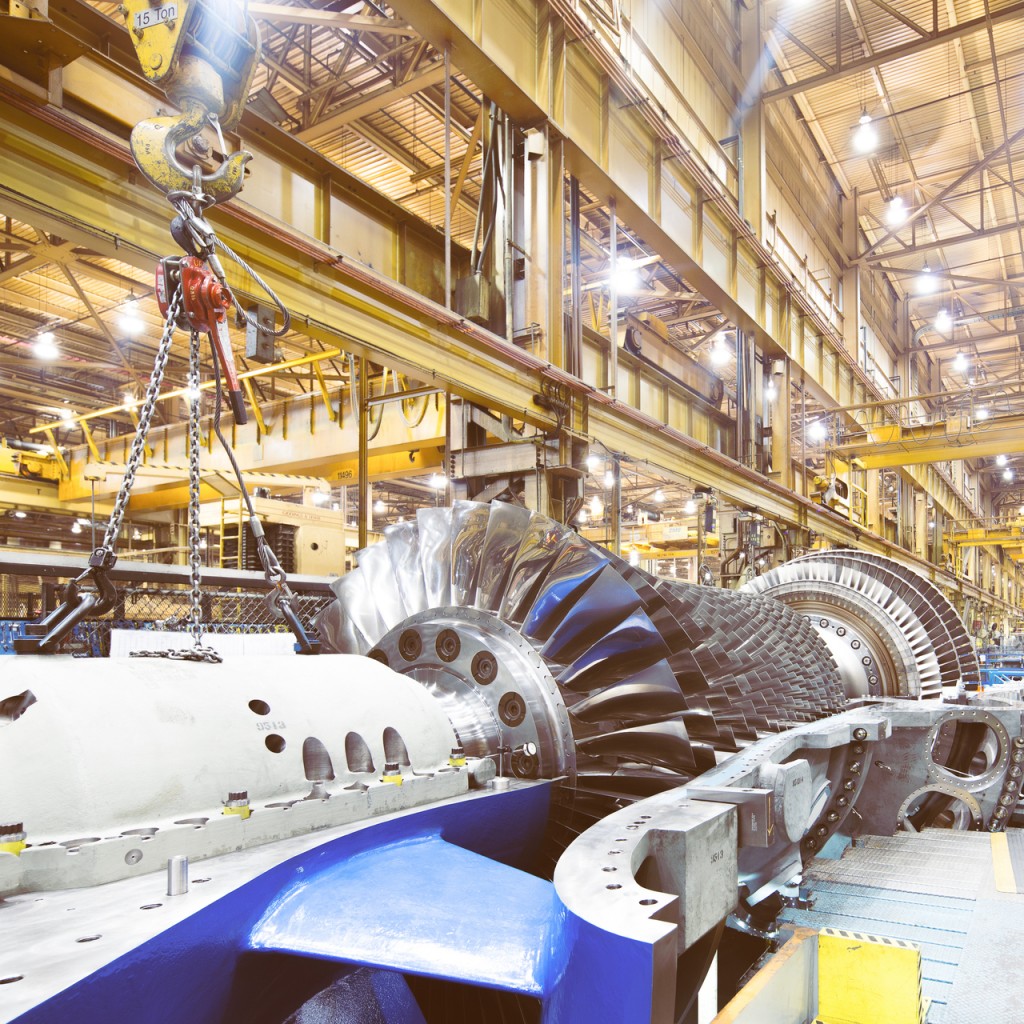
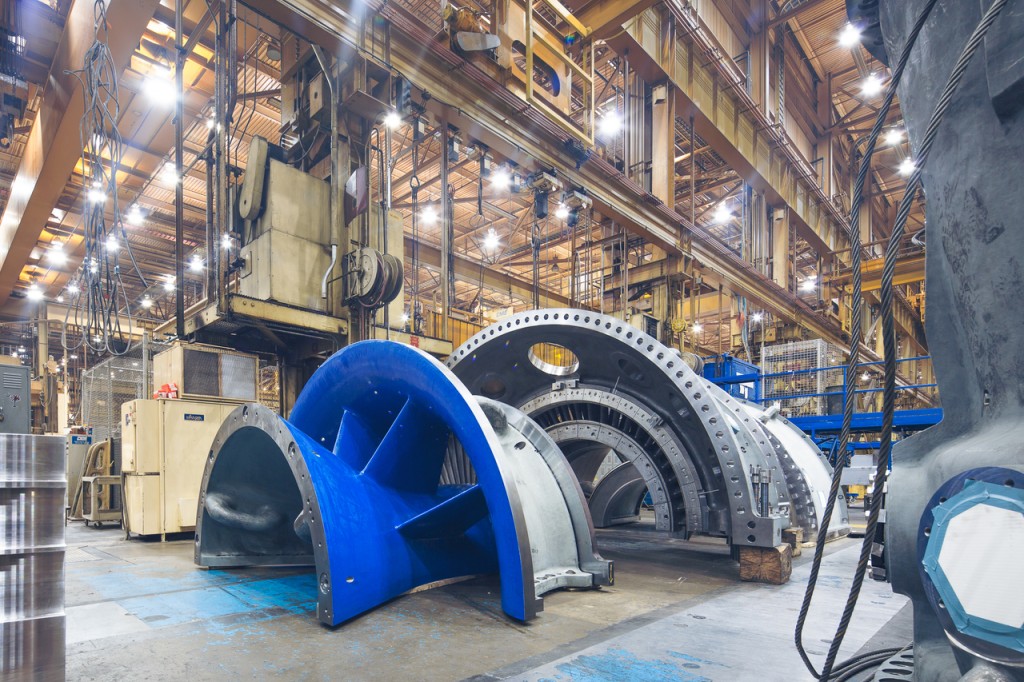
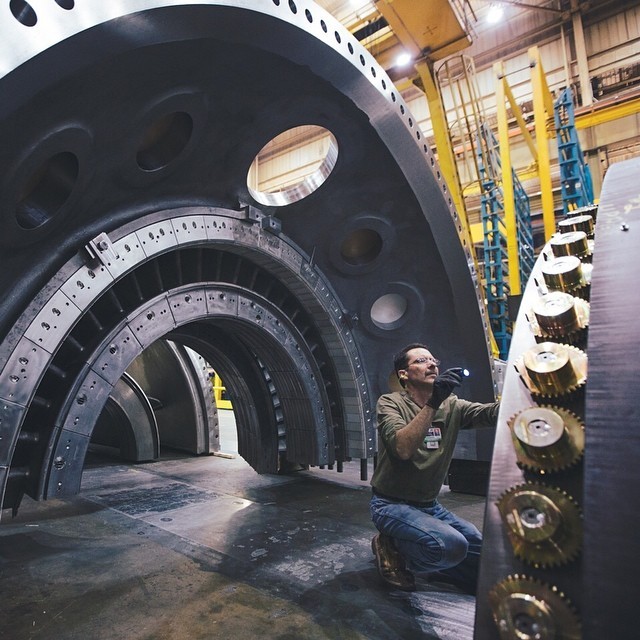
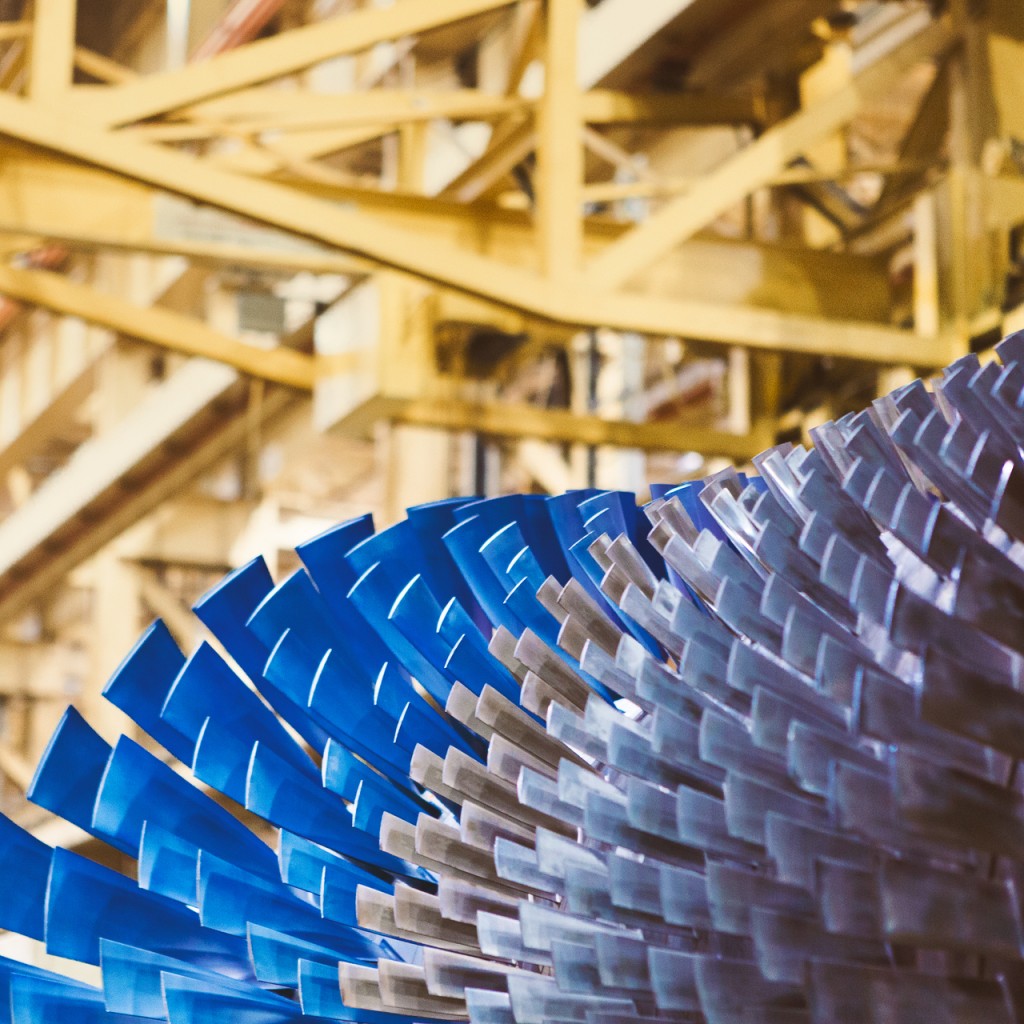
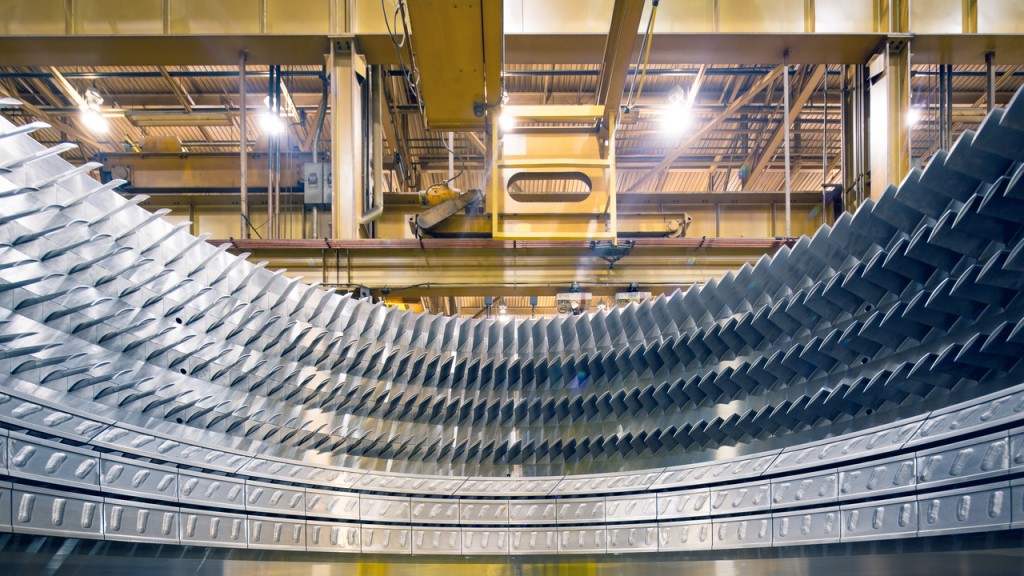
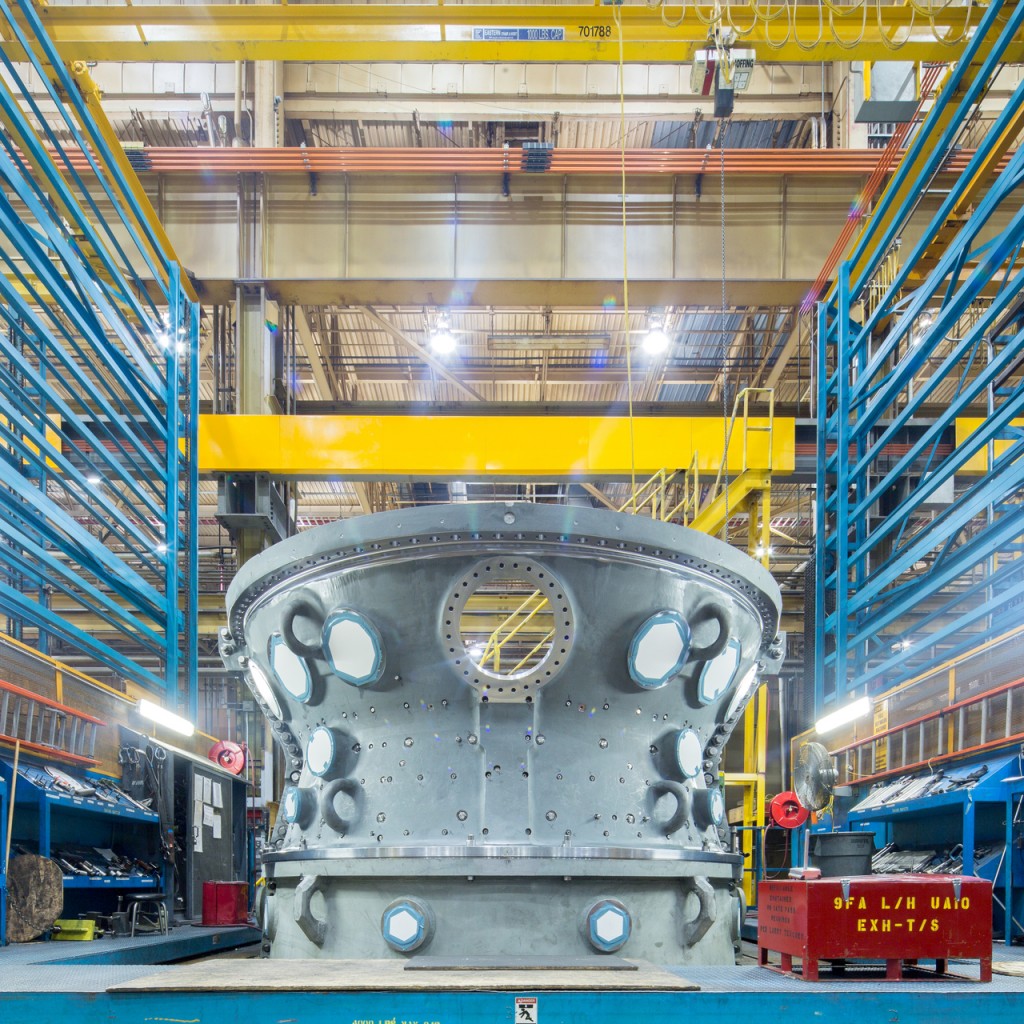
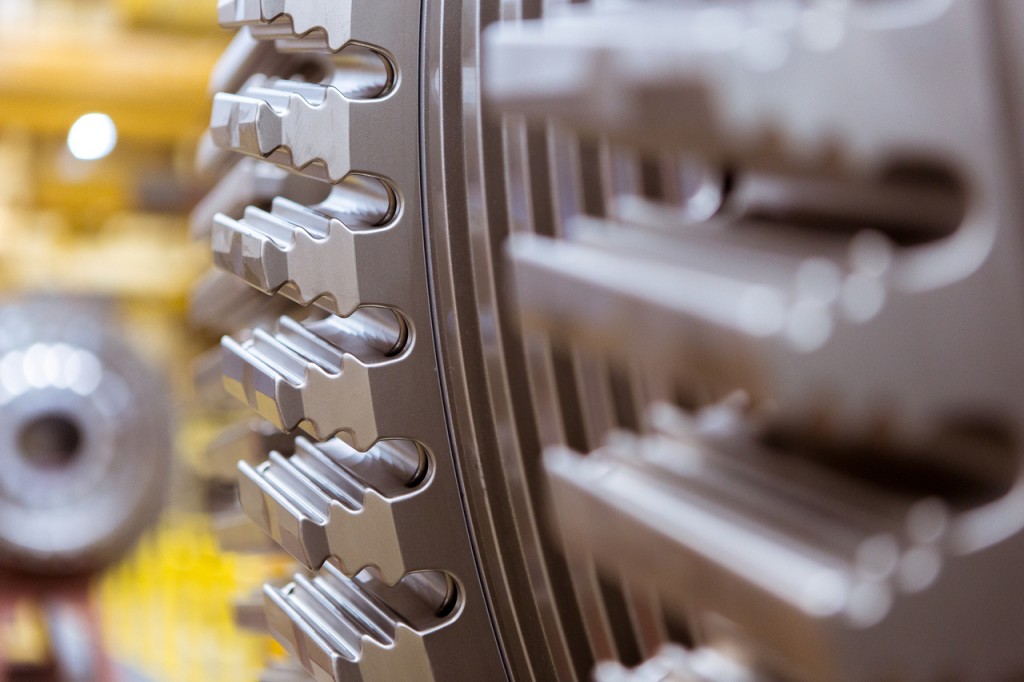
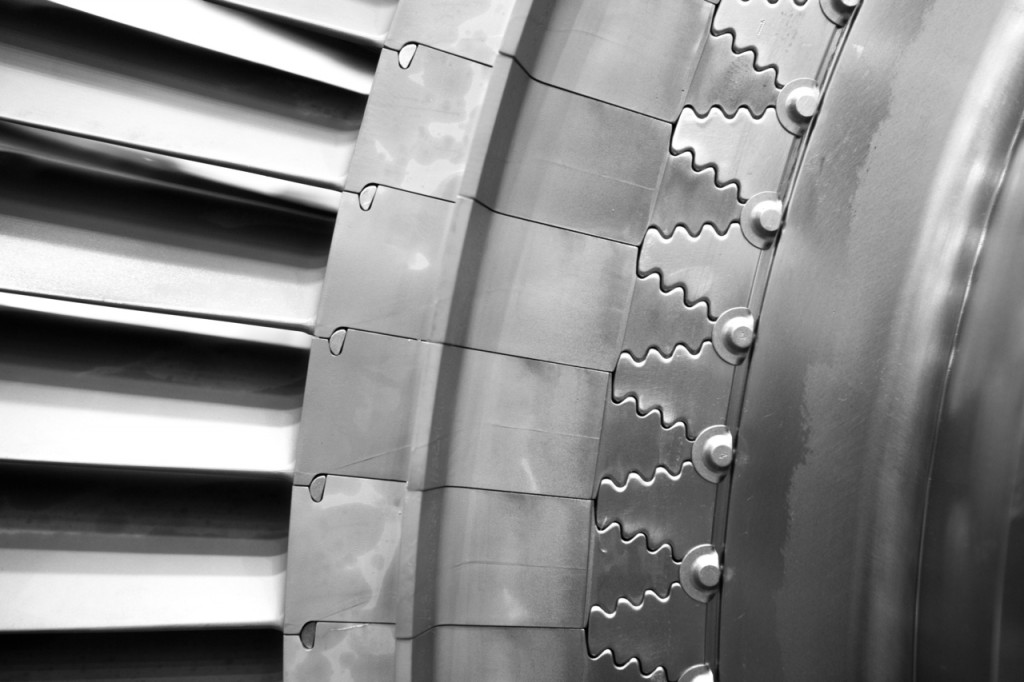
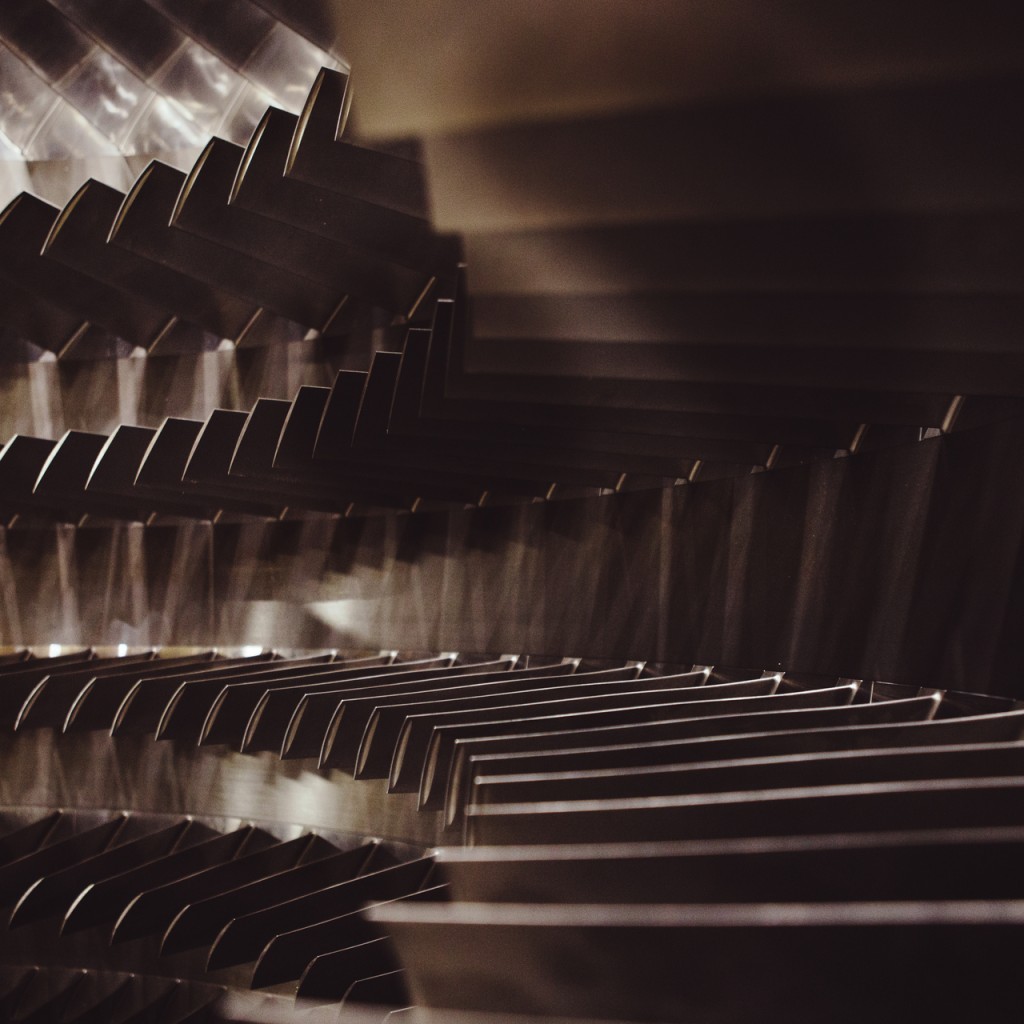
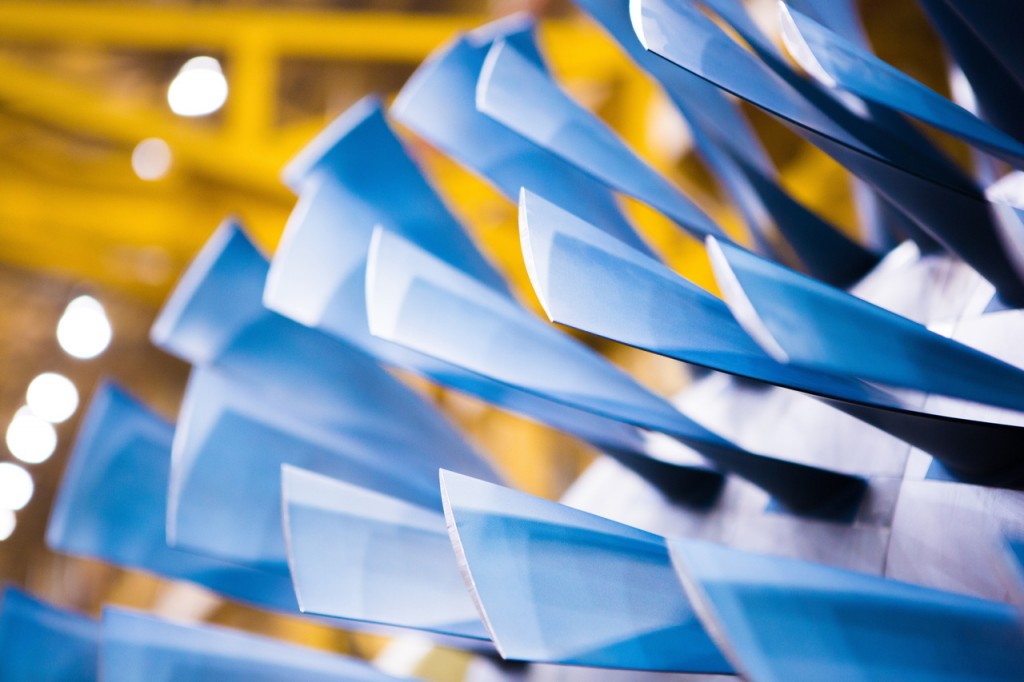
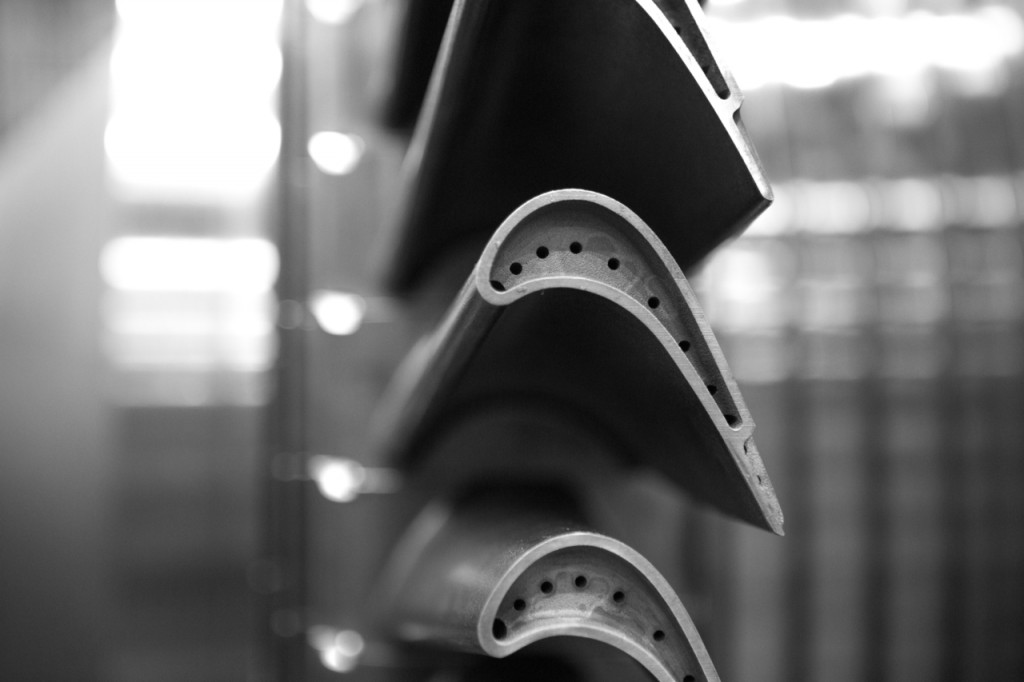
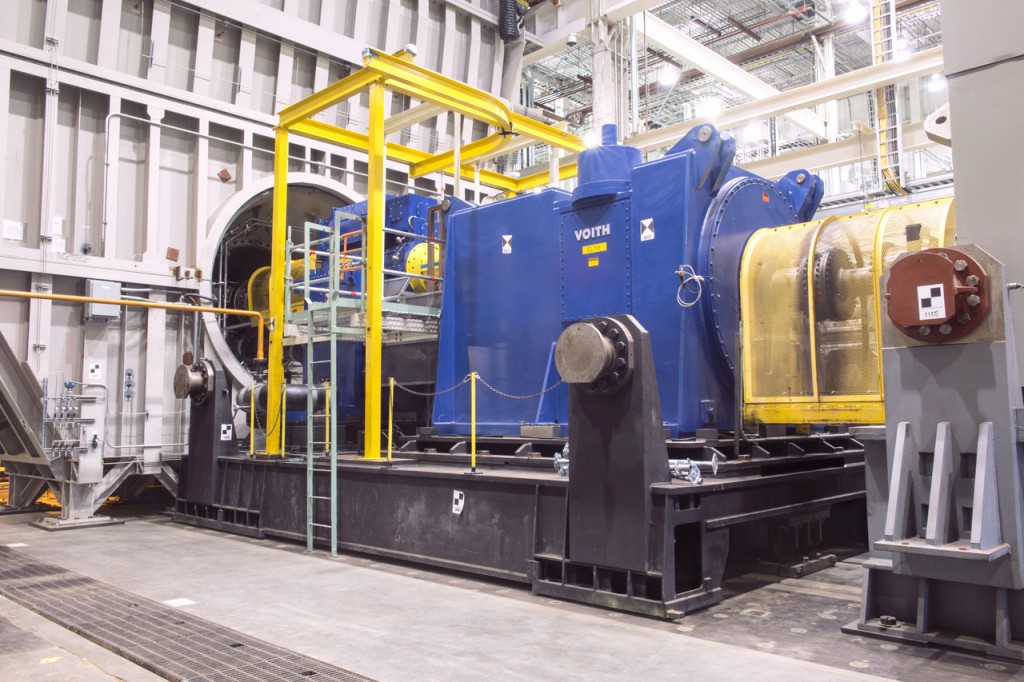
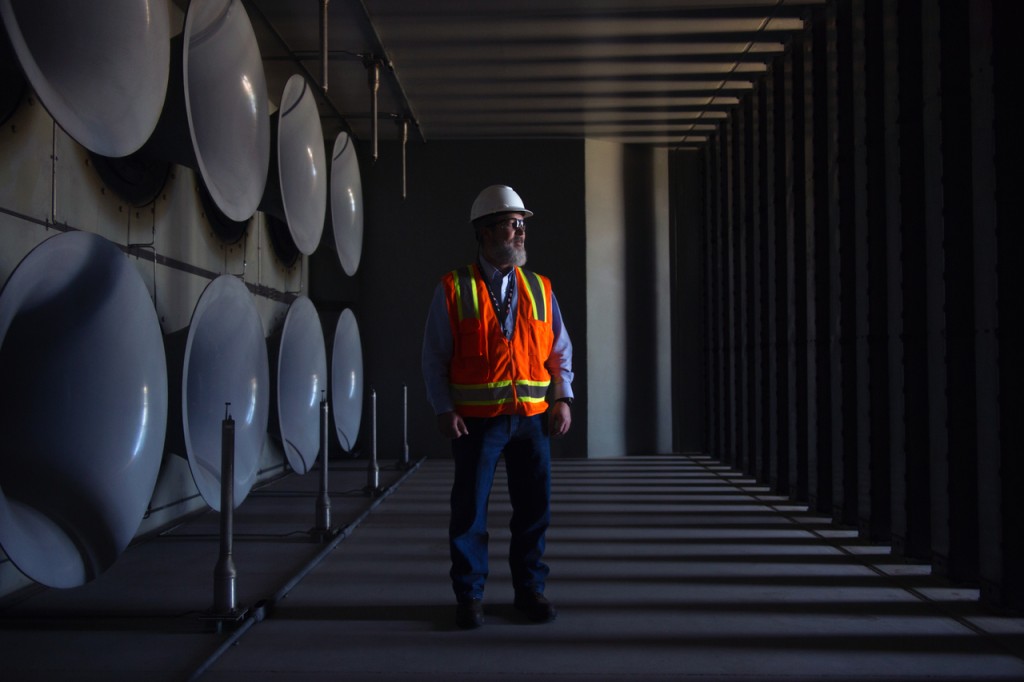
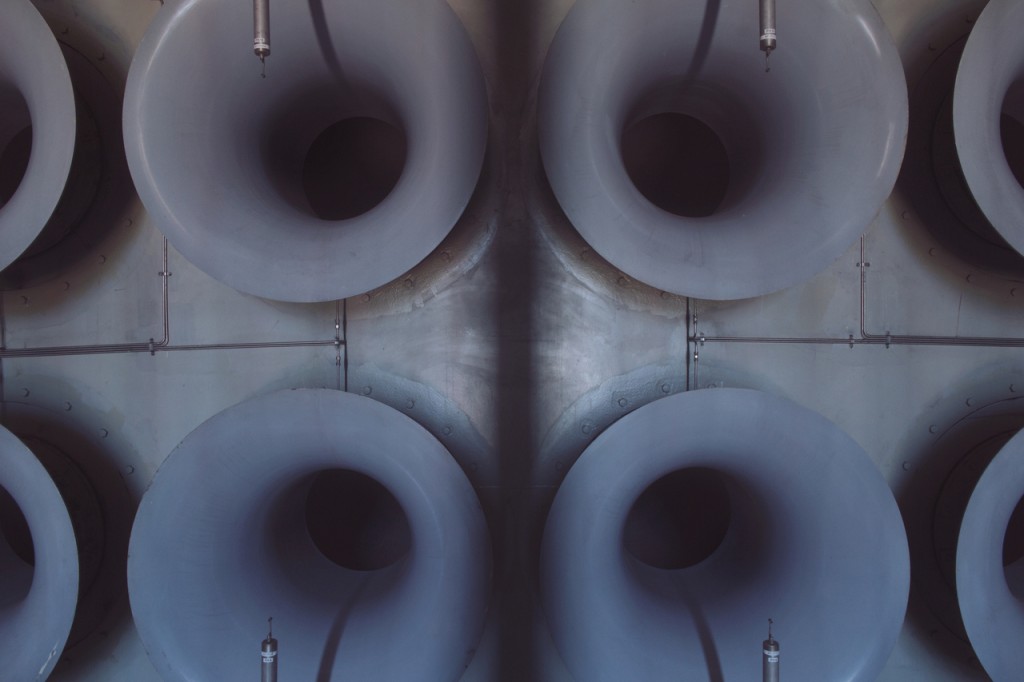
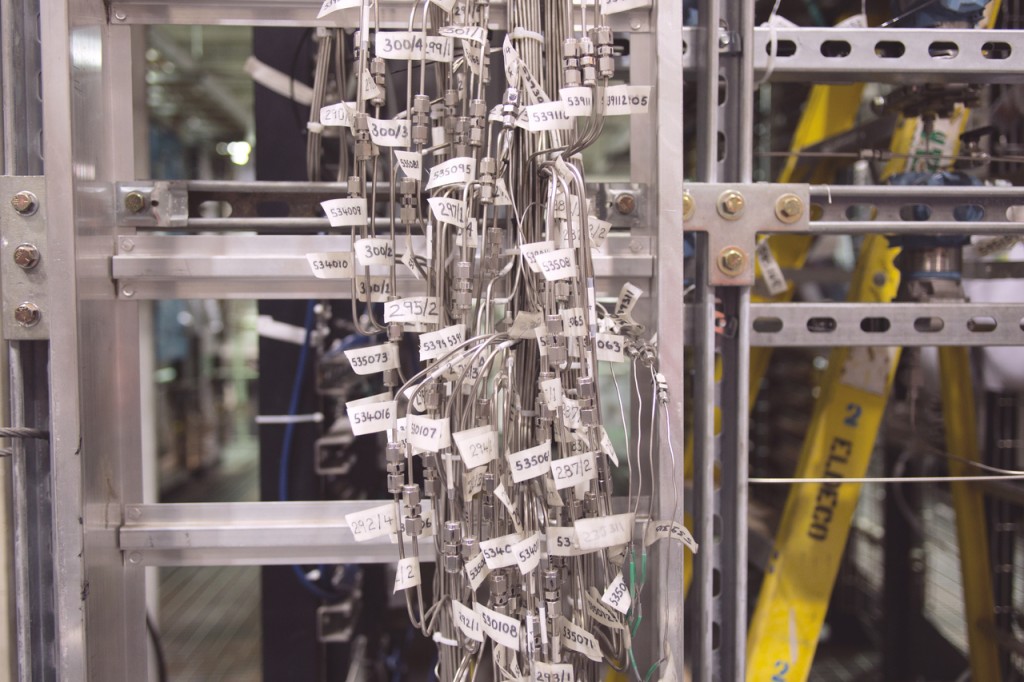
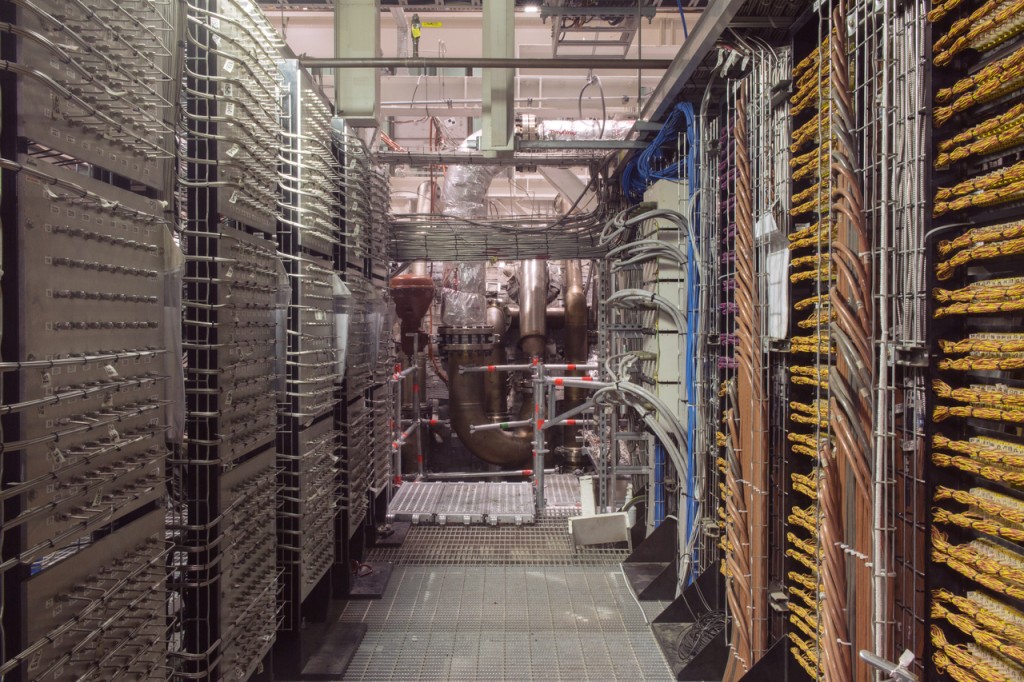
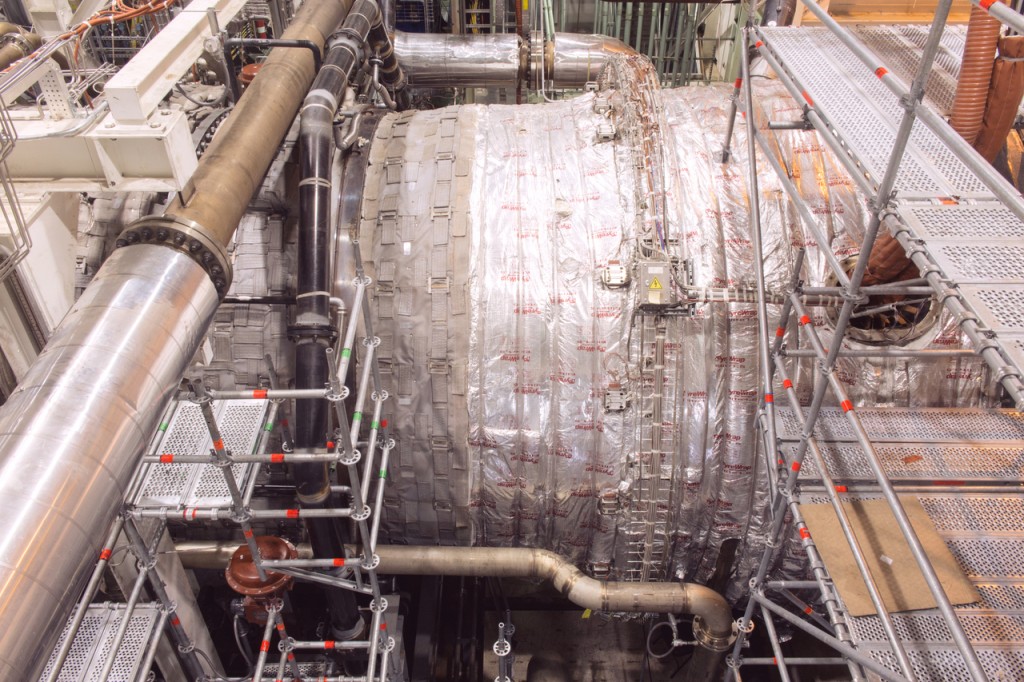