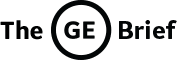
October 17, 2019
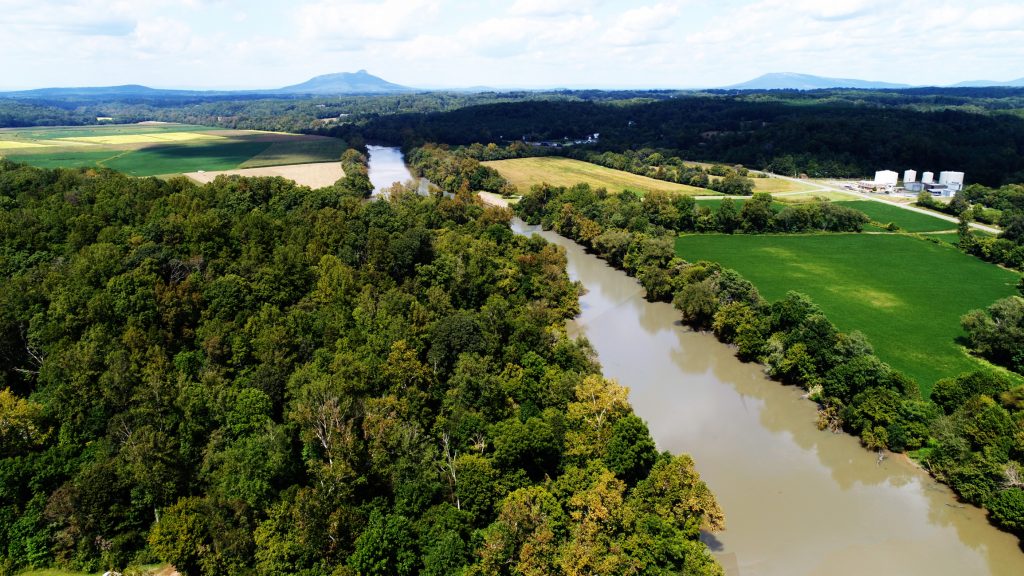
RIVER OF INNOVATION
The most important freshwater source in central North Carolina, the Yadkin River basin supports 38 rare species of fish and mollusks — and it also supports a series of hydroelectric dams that power more than 85,000 homes. For aquatic life, hydro power can make things pretty hard — dams installed for electricity generation and other purposes can deprive water of oxygen, leading to dead zones. But rather than just carp about it, one company has been looking for solutions: Cube Hydro Partners, which owns and operates the Yadkin hydro plants among dozens of other facilities, is installing a new kind of turbine on the Yadkin to ensure the health of the river. Made by GE Renewable Energy, it’s designed to reinvigorate oxygen levels as water rushes through the dam — giving river life a breath of fresh air.
Downstream benefits: Cube is in the midst of replacing three turbines installed decades ago by a former owner at the High Rock dam on the Yadkin. While hydro operators have been fishing for ways to aerate water while producing electricity, the solution has proved elusive: Large oxygen bubbles just floated to the surface of the water, and turbine efficiency declined too. GE engineers designed an aerating turbine that sends smaller bubbles of dissolved oxygen into water and generates electricity more efficiently while doing so. “The whole river downstream should benefit from this,” said Cube VP Neal Simmons. The Yadkin River where Cube operates met state oxygen-level standards more than 95% of the time this summer, up from 57% with the turbines they replaced. People who enjoy the river also claim they’re seeing benefits, Simmons said: “Anecdotally, fishermen say it’s some of the best fishing there’s been in years.”
Want to learn more about how turbines can make aquatic life happier? Go fish!
TOMORROW’S CHOPPERS
This week the helicopter maker Sikorsky — part of Lockheed Martin — unveiled plans for a new craft called the Raider X, an “agile, lethal and survivable compound coaxial helicopter” designed for the U.S. Army’s Future Attack Reconnaissance Aircraft (FARA) program. The Sikorsky Raider X is one of five candidates competing to win a contract from the U.S. Army to move on to the next phase of the FARA program. Two will be selected next year for Engineering Manufacturing Development (EMD) phase. The Raider X architecture is based on a previous Sikorsky chopper, the S-97 Raider, and like its predecessor will have an engine built by GE Aviation: The Army has selected GE’s 3,000-shaft-horsepower T901 for the FARA program. Whereas the S-97 was powered by GE’s YT706 engine, GE’s T901 engine for the Raider X provides the capability for a powerful machine to only get more powerful, as Tim Malia, Sikorsky’s director of Future Vertical Lift Light, explained to FlightGlobal: “As the T901 engine has a power growth curve over time, we'll be able to directly harness that with our existing aircraft. Upgrade the engine — you just got more speed, you just got more payload.”
Blades of glory: “We just couldn’t be happier to carry on the relationship we have with GE currently flying the YT706,” said Sikorsky test pilot Christiaan Corry. “We are really excited to pull the T901 into the Raider X.” The news continues a winning year for the T901, which in February was selected by the U.S. Army to swap into its existing workhorse helicopters, the Black Hawk and the Apache. It isn’t hard to see the appeal: The results of decades of research and innovation, the T901 relies on the latest materials like ceramic matrix composites (CMCs) — a breakthrough material that’s 20% stronger and two-thirds lighter than its metal counterparts — and advanced manufacturing techniques like 3D printing (see our next story). Over time, GE has spent about $9 billion developing these and other technologies at work in the T901, but it’s not just the military that benefits: GE is taking CMCs and 3D printing to a broad range of products, including super-efficient engines for commercial airliners.
Learn more here about the long road the T901 engine has taken to glory, and here about the Raider X.
MAJOR LASER EXPERTISE
Human beings have been casting tools, weapons and ornaments with wax molds for thousands of years — we’ve had plenty of time to hone our craft. 3D printing, on the other hand, has only been around for a few decades. That means that, in William Carter’s estimation, its practitioners have some catching up to do. Carter’s expertise gives him some perspective. The longtime GE Research engineer has been around since the dawn of direct metal laser melting, a subset of the field now known as 3D printing, or additive manufacturing. In fact, it was Carter and his colleague Marshall Jones who, a couple of decades ago, pitched their boss at GE a unique idea. The two had observed an earlier pioneer, Carl Deckard, build simple structures out of layers of plastic powder fused together by laser. Why not try it with metal?
That’s so metal: Early experiments produced promising results, but also revealed a fundamental problem — the process took too long. Carter and his peers kept at it, though, and soon began to build a series of larger and larger parts at faster and faster speeds. He’s seen the technology mature into one of today’s most advanced manufacturing processes — for instance, GE Aviation engineers were able to use 3D printing to combine 800 components of an airplane engine into just 12 parts. And Carter is still trying to speed up the tech, currently through a collaboration with Lawrence Livermore National Laboratory. It’s not just a matter of building a more powerful laser. That’s where Jones, a laser expert and a member of the National Inventors Hall of Fame, comes in. Says Carter: “If you’re watering your lawn nicely, and then you switch to a fire hose, you get a different result.”
How, then, do you build a faster 3D printer? Learn more here about the ins and outs — and past and future — of additive manufacturing.
— VIDEO OF THE WEEK —
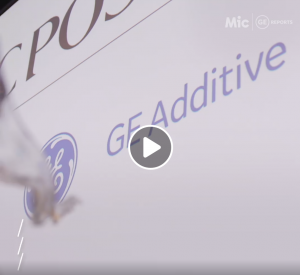
Zac Posen used 3D printers and unique materials to create fantastical dresses for the biggest fashion event of the year.
— QUOTE OF THE DAY —
“It has a very good environmental impact, and it’s a huge, huge win for us as an independent power producer. This allows us to generate several thousands more megawatt-hours every year with the same amount of water.”
— Neal Simmons, vice president of Cube Hydro Partners
Quote: GE Reports. Image: Getty Images.
ENJOY THIS NEWSLETTER?
Please send it to your friends and let them know they can subscribe here.