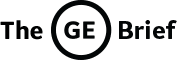
November 7, 2019
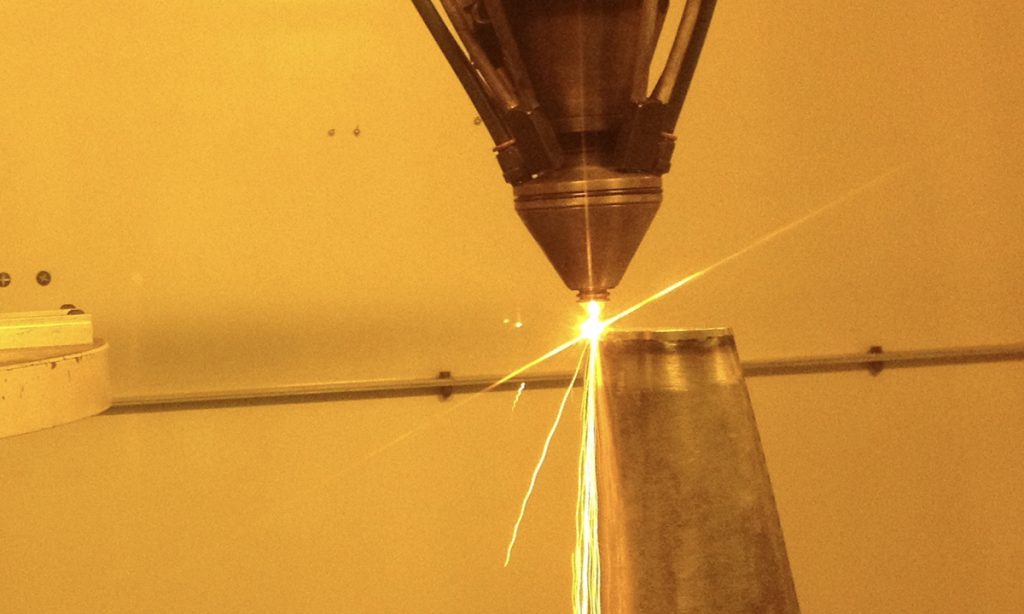
SOUPED-UP REPAIR SHOP
Over the next decade, Asian nations are projected to add more than 400 gigawatts of electrical capacity; that’s like adding a Germany to the power grid, then adding another Germany. Though much of that capacity will be renewables, those renewables will need to be supported by efficient gas turbines. And there’s none more efficient than those from GE’s record-setting HA family, the world’s fastest-growing gas turbine. But buying a gas turbine is a bigger deal than buying, say, a lawnmower, and currently, if utilities need a maintenance crew to inspect theirs, they’ve got to call GE’s repair shop in Greenville, South Carolina. That’s why today, GE announced that it’s investing up to $60 million into an existing facility in Singapore. The shop has been around since the 20th century; the money will bring it firmly into the 21st.
Investment in the future: GE’s upgrade to the Singapore facility will involve training 160 additional highly skilled employees, and support an R&D center to develop more advanced repair techniques. “This new facility gives us the ability to better support our customers in the region, and connect them with the global supply chain and 24/7 service,” said Ramesh Singaram, president of GE Gas Power Asia. Asia’s growth trajectory means that the percentage of HA turbines in the region will grow. Today, Asians without access to electricity to heat homes and cook meals likely rely on firewood, which contributes to deforestation, besides being dirty and inefficient. “Gas-powered generation can be a savior for many countries, especially in this region,” Singaram said.
Click here for more about GE’s big plans in the Asia-Pacific region.
LOOKS LIKE A BILLION BUCKS
Gas turbines aren’t the only engines powering the economies of Asia — there’s airplane engines, too. And just like gas turbines, the airplane engine market involves much more than just the engine itself; follow-on service agreements are a crucial part. The latest example? A deal that China’s Colorful Guizhou Airlines just signed with CFM International, a 50-50 joint venture between GE and France’s Safran Aircraft Engines, to service the airline’s fleet of LEAP-1A engines, which will power as many as 35 Airbus A320neo jets. Valued at $1 billion list price, the deal follows a prior engagement between Colorful Guizhou and GE: In June, the airline agreed to lease its first four jets from GE Aviation Capital Services (GECAS). Colorful Guizhou’s jets will be flying in fine company. Every two seconds of every day these days, a CFM-powered aircraft takes off somewhere in the world.
A colorful future: They’ll be flying, too, in increasingly busy skies. A new Airbus survey of the industry projects that the existing global fleet of 28,000 passenger and cargo planes will nearly double by 2038 — to 48,000. Along the way, the industry will hire 550,000 new pilots and 640,000 new technicians to help keep the jets on time, passengers happy, and carriers profitable. And Asia is the place to be. The same report expects the commercial aircraft services market to deliver a “cumulative” $4.9 trillion over the next 20 years, with the rapidly growing Asia-Pacific segment being by far the largest player.
Learn more here about the new GE deal with Colorful Guizhou Airlines.
ROCKET TO A NEW DIMENSION
Tim Ellis, co-founder and CEO of California startup Relativity Space, estimates that 3D printing accounts for fewer than 1% of the parts made by other rocket makers — even though that technique, which typically fuses layer upon layer of metal or plastic into bespoke shapes, has been heralded as the future of manufacturing. Ellis’ business is trying to hurry that future up by an order of magnitude: Relativity Space, which develops engines and launchers for commercial orbital rockets, wants 3D printing to account for 95% of its rocket parts by the end of next year.
3, 2, 1 ... As Thomas Hornigold points out in a new article in Singularity Hub, it now takes more than a year to build a new rocket from scratch, and manufacturers must rely on a “very diverse supply chain” to provide up to 10,000 components. Just as with airplane engines, the promise of 3D printing is that it could reduce the number of discrete parts, speed their production and — crucially — reduce the weight of the finished product. Hornigold writes, “Speeding up the process of manufacturing launch vehicles can prevent new satellites or experiments from having to wait months or years to reach low Earth orbit, which is a substantial bottleneck in the commercial exploitation of space.” Read more here.
— VIDEO OF THE WEEK —
— QUOTE OF THE DAY —
“Customers make investment decisions on power over a 20-year view. So it’s important they see we can support our customers in real time with capable and responsible engineers.”
— Ramesh Singaram, president of GE Gas Power Asia
Quote: GE Reports. Image: GE Power.
ENJOY THIS NEWSLETTER?
Please send it to your friends and let them know they can subscribe here.