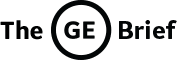
February 27, 2020
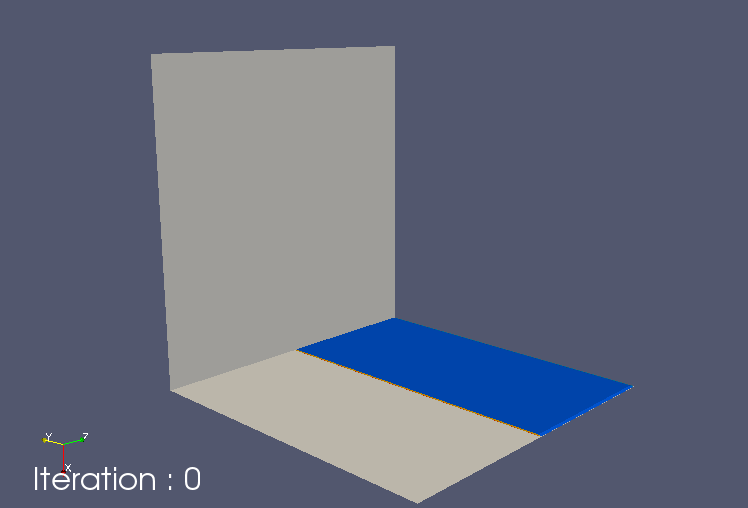
TESTING THEIR METAL
When it comes to traditional manufacturing techniques, humans have some practice — we’ve been working metal for millennia. But we’ve only had a few decades, by contrast, to get used to 3D printing, in which computer-guided lasers fuse tiny metal particles into complex shapes. Because it’s still so relatively new, there are kinks to be worked out. “We’re finding that while we have capabilities to build features we never had before, we don’t yet have the design tools to take advantage,” said Brent Brunell, technology director for additive technology at GE Research. That’s why GE, Xerox subsidiary PARC and Oak Ridge National Laboratory (ORNL) are collaborating on a new project that they hope will cut the timeline for designing and validating 3D-printed components by two-thirds.
Super models: Funded by a grant from the U.S. Energy Department’s Advanced Research Projects Agency (ARPA-E), the project is a natural fit for GE, which was the first company to get 3D-printed parts approved for use in jet engines. The consortium will compile a database of materials that could be used in 3D printing, and take advantage of ORNL’s powerful supercomputers to model how various parts will hold up during the strain of the build process. That should speed up prototype design, Brunell explained: “We’ll be able to produce parts we never could have produced before. And with the push of a button, change the design and get a new part in weeks or months, instead of years.”
Learn more here about the ARPA-E grant.
NEW TRICKS
What those GE Research engineers above are doing is, in short, helping an old industry (manufacturing) learn new tricks (3D printing). But new industries and technologies can learn new tricks too — as demonstrated by scientists elsewhere at GE Research who are trying to train computers themselves how to learn. As the chief scientist for artificial intelligence at GE Research, Peter Tu works with researchers from Siena College under a grant along those lines that’s funded by the U.S. Defense Department’s Grounded Artificial Intelligence Language Acquisition program, or GAILA. The idea is to teach computers to learn language through visual and contextual cues — just like kids and animals do.
Sit, stay, compute: AI is great at processing massive amounts of data and spotting subtle patterns. It’s less good in situations when the AI agent has what Tu describes as a “poverty of stimulus” — simply not enough information to go on. That’s something kids and animals are great at: “As children, we do a large number of inductions,” Tu said. “A child with limited examples is very good at drawing out general rules.” If AI-enabled machines can master such nuances in communicating with humans, and eventually with one another, Tu thinks, it’ll be a step toward machines that comprehend all sorts of problems. Although cognition-wise, they’ll still have a ways to go compared to humans — millions of years of evolution have given us a bit of a head start.
Learn more here about Tu’s highly intelligent work at GE Research.
A JEWEL IN THEIR CROWN
A mining company operating in Botswana keeps digging up the world’s largest diamonds, but halfway across the globe in California, they’re figuring out how to make their own. In a new article in Science Advances, researchers at Stanford University and SLAC National Accelerator Laboratory described a new method for producing diamonds that involves a carbon and hydrogen molecule found in crude oil and natural gas — plus a powerful laser. As Stanford geologist Rodney Ewing put it, “What’s exciting about this paper is it shows a way of cheating the thermodynamics of what’s typically required for diamond formation.”
Ingenuity is forever: Scientists have been working on synthesizing these gems for decades and for a while, even GE was in on the game. In 1954, a group of GE researchers built a machine that squeezed carbon so hard that it turned into a diamond. But previous techniques have required huge amounts of energy, time or the use of a catalyst. “We wanted to see just a clean system, in which a single substance transforms into pure diamond — without a catalyst,” said Sulgiye Park, the study’s lead author. Research like this is about more than jewelry, though, as Stanford explains in a release: “Diamond’s physical properties — extreme hardness, optical transparency, chemical stability, high thermal conductivity — make it a valuable material for medicine, industry, quantum computing technologies and biological sensing.”
Learn more here.
— VIDEO OF THE WEEK —
Relying on deep expertise and an abundance of data, the GE Grid Solutions unit of GE Renewable Energy is helping make the electrical grid smarter and more resilient, and bringing more renewables to homes and businesses.
— QUOTE OF THE DAY —
“Additive manufacturing isn’t only going to disrupt design. It’s going to disrupt manufacturing too.”
— Brent Brunell, technology director for additive technology at GE Research
Quote: GE Reports. Image: GE Research.
ENJOY THIS NEWSLETTER?
Please send it to your friends and let them know they can subscribe here.