But business was drying up. Looking to save money, toy companies were relying more and more on in-house sculptors rather than freelancers. “They were experimenting with anything that would bring down their costs,” Langford says. “I was at the upper level of the talent pool in terms of experience and training, but even with that skill level you don't have to be Michelangelo to sculpt a toy.”
To make matters worse, tool manufacturers in China had begun offering to sculpt toy designs for free in return for getting the tool contracts for producing the finished toys. “The director of sculpting at Mattel was a friend of mine, and he said ‘Matt, look, you're just going to have to find another gig, because the industry is just flat-out changing,’” Langford says.
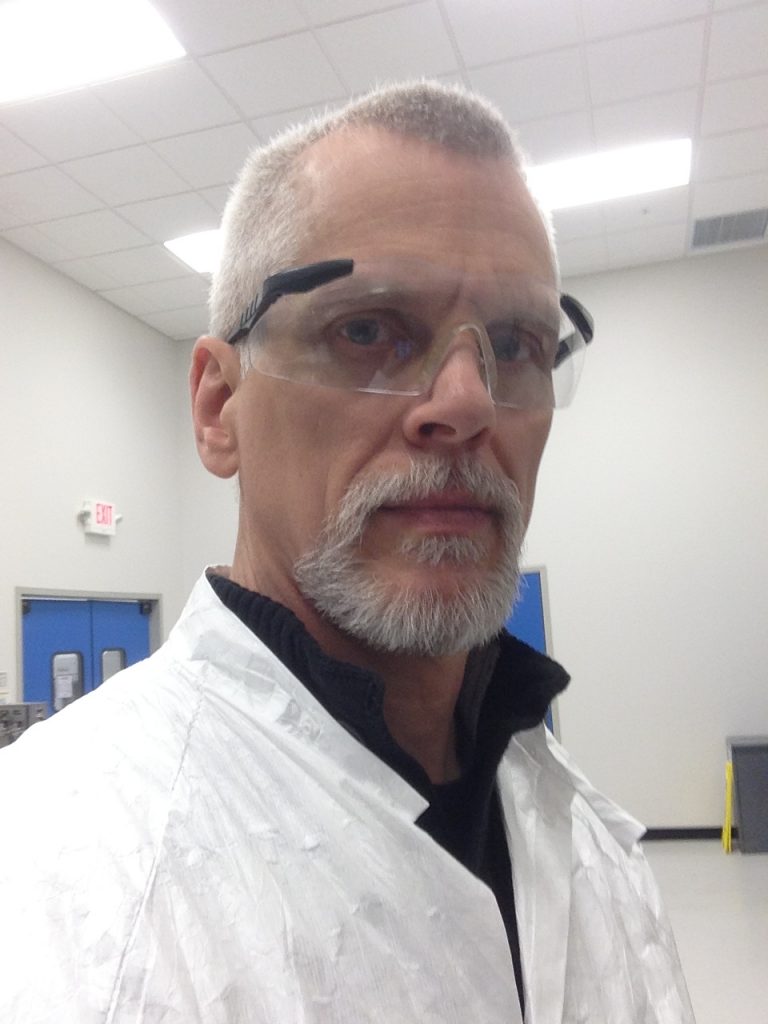
One of Langford’s neighbors suggested the sculptor apply for a job at Morris Technologies, a local company started by 3D-printing pioneer Greg Morris that was looking for people with metal skills. “As a fine art sculptor, I had a background in bronze casting, which made it possible for me to go there,” he says.
Langford began working in Morris’ additive metals department, where he did finishing work on a variety of items, including joint replacements, bone screws and artificial heart pump valves after they emerged from 3D-printing machines. “I picked it up quickly, because it was basically a variation on things that I’d done in the toy industry,” Langford says. While his work for Morris wasn’t as whimsical as his Star Wars pieces, Langford found the same sense of satisfaction in perfecting the parts.
In 2013, when GE Aviation bought Morris’ company, Langford stayed on and eventually moved over to GE’s Additive Technology Center in Cincinnati, where he now makes complex airplane engine parts that were difficult, or even impossible, to make through conventional casting. “We’re taking parts like heat exchangers and fuel nozzles that used to be 20- or 30-piece items and combining them into one unit produced additively,” he says. “It’s tricky and fascinating.”

Langford has been able to move around within the center working on design, metal inspection, finishing work and other parts of the fabrication process. His favorite work, however, is his current job — running an SLA polymer lab, where he uses a plastics-based 3D printer to build models of the parts that eventually will be printed out of metal. “The models give visual feedback to the engineers and allow them to see their pieces, handle them and test the fit,” Langford says.
The design work requires many of the same muscles Langford used to flex when designing toys. Although he usually works from digital engineering drawings, he still needs to visualize what the final product will look like, and he still uses his artistry to turn the ideas into real pieces. “I'm still working as an artisan,” he says. “I think, if you can make your daily bread and utilize the skills that you have, that's respectable.”
He’s also still doing art on the side. In the last few years, he’s won commissions to create sculptures around the country, including the America’s Response Monument, a collaboration with artist Douwe Blumberg that stands near Ground Zero in New York City. “The things I’m doing at GE are sort of cousins to the things I’m doing in my art,” he says. “In my artistic life, I’m pursuing a light on the horizon, and I’ve got a day job that’s valuable, serves a purpose and is appreciated.”
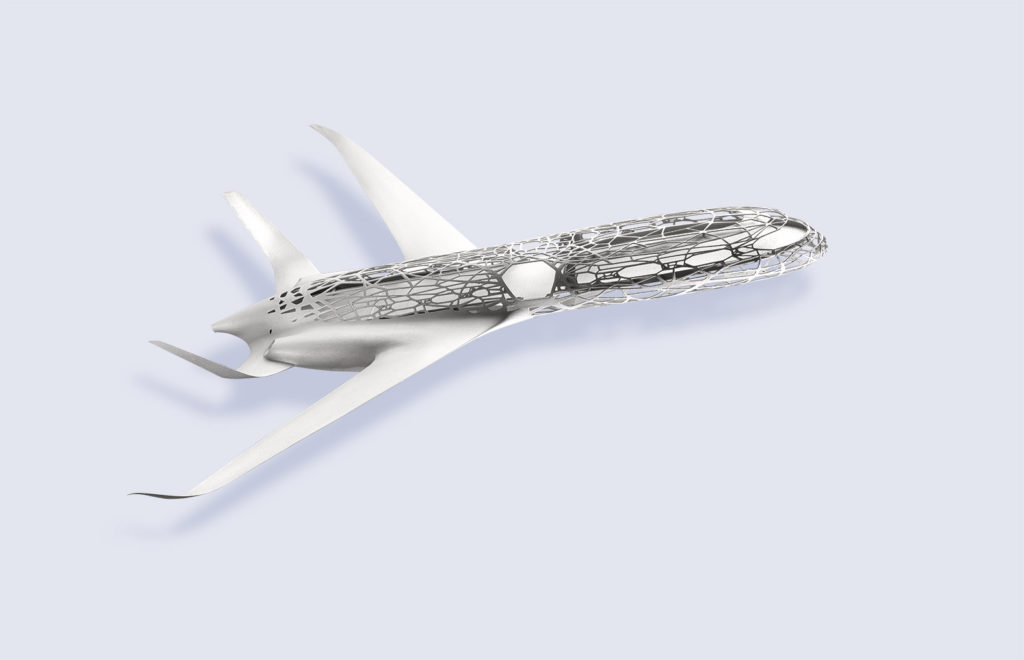