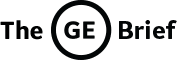
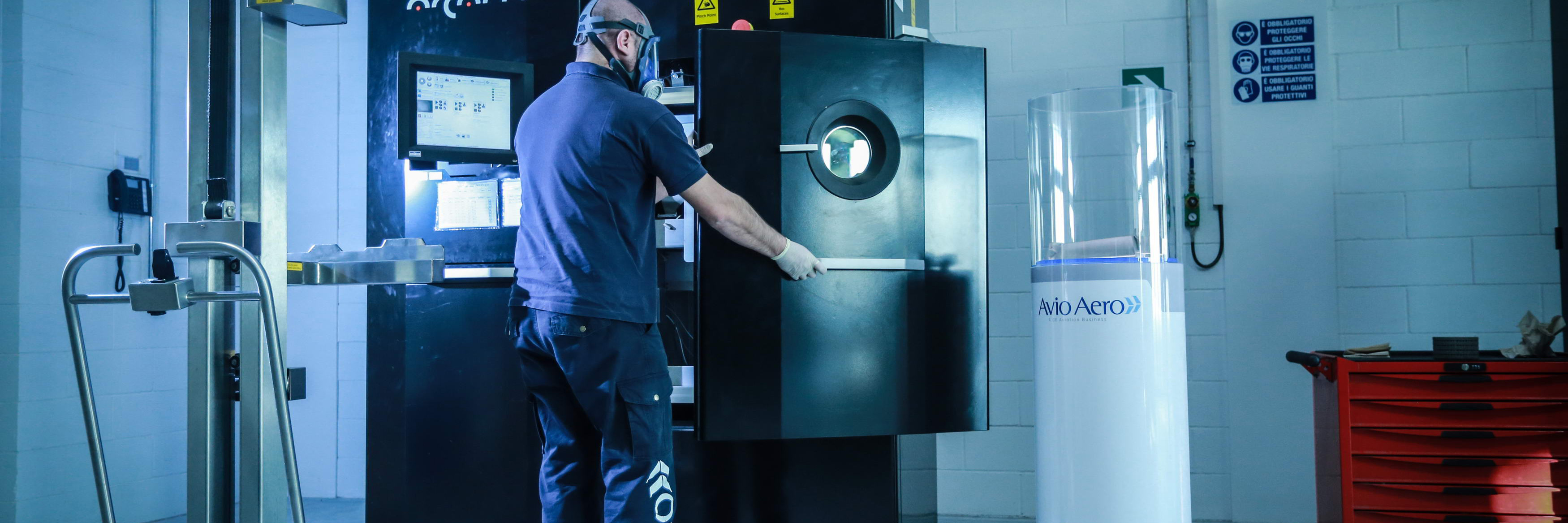
“This factory has helped us understand what the art of the possible is with additive manufacturing.”
— David Joyce, president and CEO, GE Aviation
1. 3D PRINTING JET ENGINE BLADES
The lush green fields near the town of Cameri in northern Italy hide an industrial secret: a futuristic factory that 3D prints 15-inch, sleek turbine blades for the world’s largest jet engine, the GE9X. GE Aviation is developing the engines for use in the Boeing 777X, a fast, fuel-efficient aircraft named one of the top 10 aviation innovations of 2015.
The 3D printing plant holds 20 wardrobe-sized printers created by Arcam. Each machine can print six blades at once. They are made from titanium aluminide, a strong wonder material much lighter than most metal alloys used in aviation.
The blades, combined with 3D-printed fuel nozzles, will make the engine 10% more fuel efficient than its predecessor — no small feat, considering that fuel accounts for almost 20% of airline operating costs. 3D printing is clearly growing up. Click here to learn more.
2. BIOPRINTED BODIES 
Engineers at Johnson & Johnson’s 3D Printing Center of Excellence are learning how to 3D-print surgical tools, implants, and even make “bioprinted” tissue for organs. Earlier in 2017, J&J visited GE Healthcare’s advanced manufacturing lab in Waukesha, Wisconsin, to explore the possibilities of additive technologies like 3D printing.
Combined with physics, materials science and advanced computing, additive manufacturing allows engineers to solve medical problems in ways that were “previously unimaginable,” said Joe Sendra, the global vice president for manufacturing, engineering and technology at J&J.
Doctors can use 3D printing to create precisely fitted implants from MRI and CT scans. They can also print bespoke surgical tools. Learn more about the new frontiers of 3D printing in medicine.
3. OPEN SOURCE PROSTHETICS
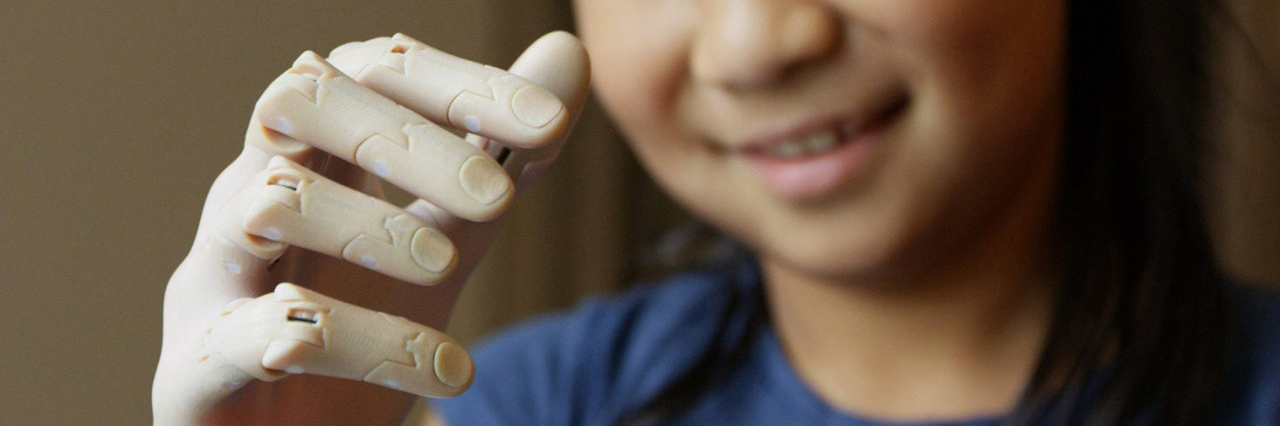
Engineer Easton LaChappelle built his first robotic prosthetic arm when he was just 14, using Lego, fishing wire and electrical tubing. In 2013, then-President Barack Obama shook the prototype’s hand at a White House science fair. Seven years later, the young inventor has partnered with Microsoft to create a 3D-printed, fully functional robot arm for a 9-year-old girl named Momo.
LaChapelle’s 3D-printed arm looks, moves and feels like a human arm, which allows Momo to do the simple things she’s always dreamed of, like being able to open a door alone. LaChappelle’s project doesn’t end there: He has released the prosthetic design as open source to help others create affordable prosthetics of the future.
In 2014, GE engineer Lyman Connor also took to building a bionic 3D-printed hand for a young patient — learn more about his project here.
4. MASTER OF ROBOTS
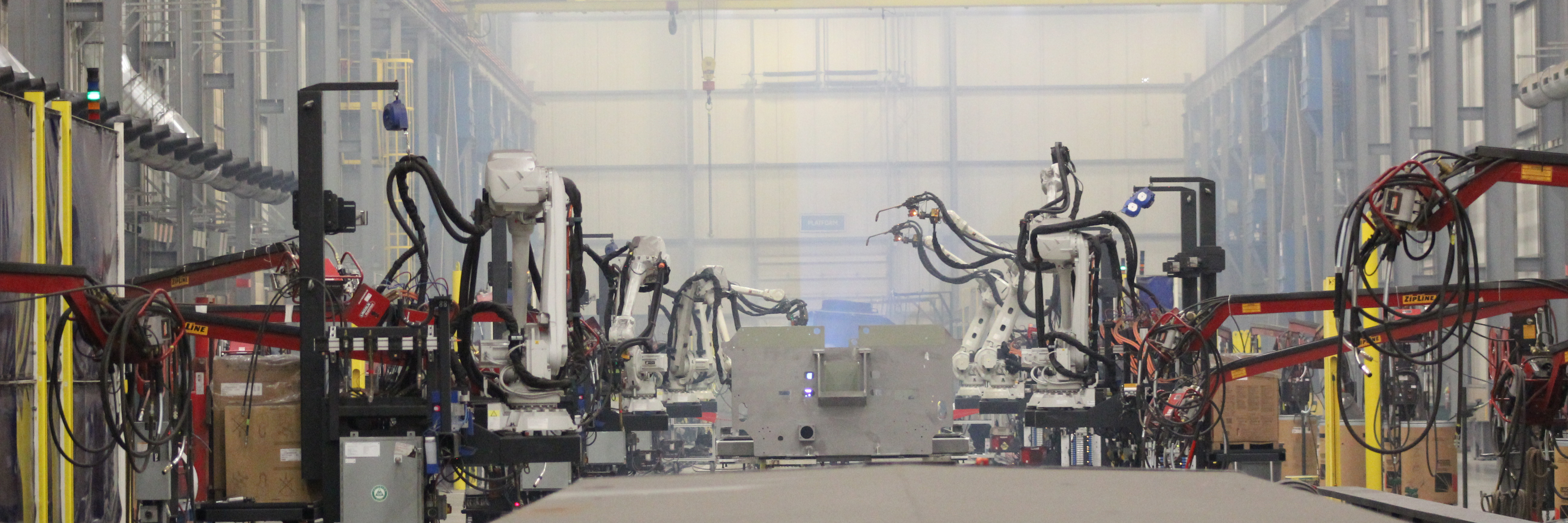
Inside GE Transportation's engine remanufacturing plant in Pennsylvania, robot assistants are helping human workers become more efficient. Robots can do the work of cranking a hydraulic torque wrench to precisely tighten bolts of a 40,000-pound locomotive engine.
Instead of having to reconstruct each engine from scratch, workers can now also make smaller repairs, thanks to digital sensors that can diagnose exactly what needs fixing on locomotive parts.
While some workers fear losing their jobs to automation, economists and historians are optimistic that technology can actually open new roles for human employees. At GE, some welders are already learning how to program robots that help them improve their craft.
Look inside GE’s “brilliant” locomotive remanufacturing plant.
ASK GE
Paul Williams from Sydney asks,
How will the United States minimize the power generation fluctuations of wind and solar?
Answer:
“Wind and solar are called ‘non-dispatchable’ generation sources, meaning that they cannot be easily turned on or off. Dispatchable generation such as gas turbine-based power plants burning natural gas are the perfect complement to renewables. These plants are able to start in a matter of minutes and can ramp power output up or down very quickly while remaining connected to the grid. Utility-scale battery storage is another possibility. The tremendous cost reductions in batteries over the past few years, driven mainly by the growing demand for electric vehicles, has opened up new possibilities for battery storage with utilities in the U.S.”
— Jim Donohue, Director of Market Insights, GE Power
Subscribe to The GE Brief here.
Quote: GE Reports. Images: Yari Bovalino, GE Reports, Belief Agency, GE Transportation.