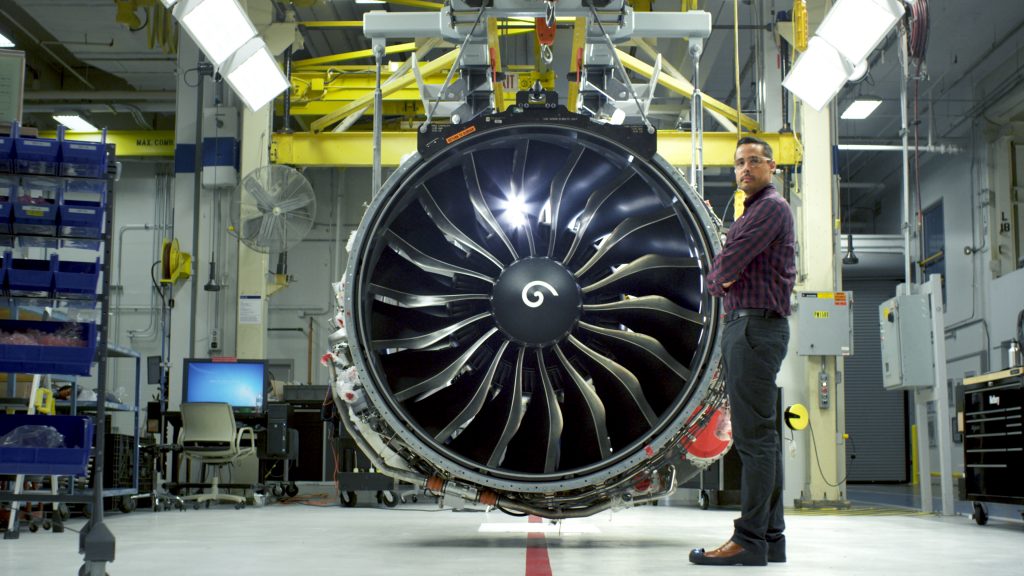
BUILDING JET ENGINES IN 3D
GE Aviation’s 3D-printing facility in Auburn, Alabama, recently turned out its 30,000th fuel nozzle tip: a walnut-sized part that gave rise to one of the world’s best-selling commercial jet engines, ignited a new GE business unit and expanded the possibilities of 3D printing on a mass scale. As high as the little part flies these days, it wouldn’t have been possible without the innovative tinkering of an ambitious team of GE engineers.
Fueling the future of manufacturing: The engineers designed a fuel nozzle tip that fits the specifications of the LEAP engine, a next-gen commercial engine now powering the likes of Airbus’ A320neo and Boeing’s 737 MAX jets. The nozzle tip’s design was so labyrinthine that it couldn’t be realized via traditional manufacturing methods. Enter 3D printing, which is especially suited to complex parts like this one. Rather than requiring the welding of as many as 20 parts, 3D printing offers engineers the chance to build the fuel nozzle tip by fusing layer upon layer of fine metal powder into the final shape.
Still, they had a ways to go till the finish line. GE Aviation had previously used 3D printing only for prototypes — never for a whole fleet of commercial jet engines. But they delivered. CFM International, the 50-50 joint venture between GE Aviation and Safran Aircraft Engines that developed the LEAP, has received orders and commitments for more than 16,300 LEAP engines valued in excess of $236 billion at list price.
How did GE turn a 3D blueprint into a high-flying reality? Learn more here.
RUST NEVER SLEEPS, BUT NEITHER DO GE ENGINEERS
At the world’s largest oil refinery, nestled within thick mango groves in the Indian state of Gujarat, the health of some 4,000 kilometers of pipes is a constant concern. The pipes are the Jamnagar facility’s most critical component, but they’re vulnerable to corrosion from water, which in this region comes courtesy of monsoons; and corroded pipes require costly repair and downtime.
More than a pipe dream: Since 2012, engineers from GE’s India Technology Center in Bangalore have been on the case. They’ve worked with the refinery’s operator Reliance Industries to develop a suite of sensors and software that can detect water early and dispatch teams to stop corrosion before it takes hold. “When we cut ourselves, the brain immediately knows it because of the network of nerves connecting every part of our body to the brain,” said Vinay Jammu, technical leader for software and analytics at the GE Bangalore center. “We are trying to develop something similar for machines.”
The solution being tested — which currently involves 20 sensors on 2.5 kilometers of pipes, with more on the way — combines GE’s engineering savvy with software and data analytics, a digital-age approach that helps the team identify threats with greater accuracy and foresight. “Today the state of the art of detection is statistics,” said GE senior engineer Manoharan Venugopal. “Refineries estimate the probability of corrosion in the system and replace as much as a quarter of their pipes every year. We think we could be more surgical.”
Read more about the sensors at the Jamnagar refinery here.
THE SECRET WORLD WAR I PROJECT THAT LAUNCHED GE AVIATION
This month, the world remembered 100 years since the end of World War I, a conflict that changed the map of Europe and left an estimated 17 million people dead. But, amid its devastation and disruption, the war also accelerated the rise of new industries like aviation.
Flying high: The war was the first large military conflict that involved planes. In November 1917 — seven months after the United States entered the war alongside the United Kingdom, France and Russia — GE President E.W. Rice received a note from the National Advisory Committee for Aeronautics, NASA's predecessor. The U.S. government wanted to develop its own version of a turbosupercharger, a mechanical device designed to fill the cylinders of a piston engine with more air than it would typically ingest, and boost the performance of warplanes powered by the Liberty aircraft engine, which was central to America’s air combat effort. The project succeeded: Planes equipped with the device went on to score several world altitude records, and its chief designer GE engineer Sanford Moss ended up in the National Aviation Hall of Fame.
Read about GE’s journey from the turbosupercharger to the LEAP here.
COOLEST THINGS ON EARTH ?
1. Stem cells against Parkinson’s
In patients with Parkinson’s disease, a loss of dopamine-producing neurons in the brain leads to symptoms like bodily tremors, stiff muscles and difficulty walking. Now neurosurgeons in Japan have implanted “reprogrammed” cells into the brain of a Parkinson’s patient that might make up for the neuron shortage and alleviate symptoms.
2. Electrical temporary tattoo
Scientists at Carnegie Mellon University and Portugal’s University of Coimbra have developed an ultrathin electric circuit that can be applied to the skin just like a temporary tattoo — because it’s printed on the same kind of paper as temporary tattoos. This new tech was developed as part of a larger project that is looking for ways to embed wearable low-cost electronics onto thin, flexible materials that can be attached to the skin, where they could monitor things like heart rate and muscular activity.
3. AI creates fingerprints
New York University researchers used a neural network to generate artificial fingerprints that could trick biometric identification systems. Described as a “master key” for fingerprint-ID systems, these “DeepMasterPrints” could fool such systems about one in five times, versus the typical error rate of one in a thousand.
Read more about this week’s Coolest Things on Earth here.
— QUOTE OF THE DAY —
“People think 3D printing is as simple as operating an ink printer, but it’s not. The fuel nozzle requires orchestrating over 3,000 layers of powdered metal that are about the thickness of a human hair.”
— Chris Schuppe, general manager of GE Additive’s AddWorks
Quote: GE Reports. Image: GE Aviation.
ENJOY THIS NEWSLETTER?
Please send it to your friends and let them know they can subscribe here.