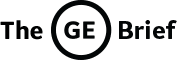
February 14, 2019
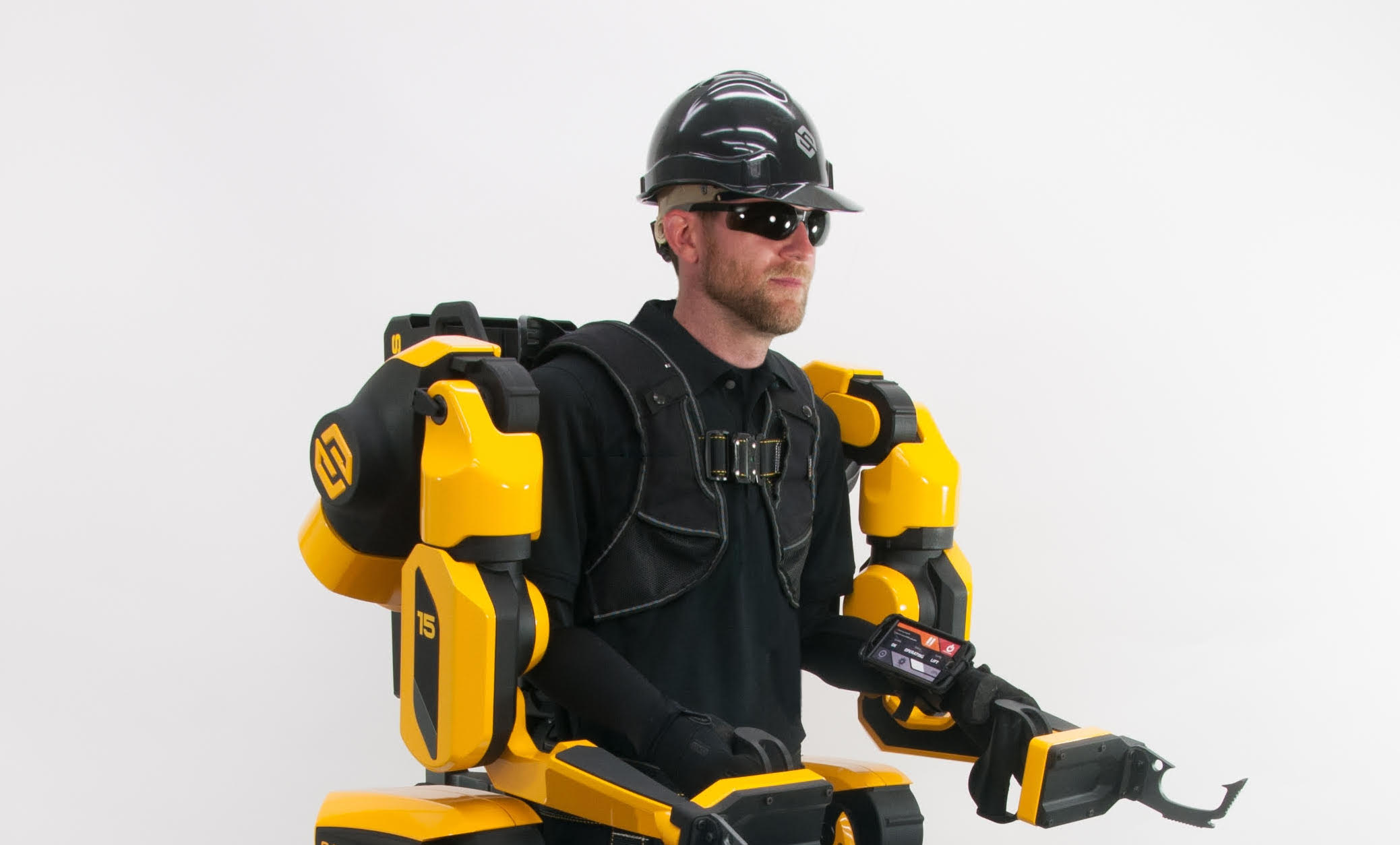
XO-RBITANT STRENGTH
The bionic person capable of superhuman strength is an old sci-fi fantasy that’s about to become an industrial fact: A robotic exoskeleton that wraps around a human body, planned for release next year, will allow its wearer to pick up objects with the strength of a forklift but the dexterity of human hands. Developed by Sarcos Robotics with investment from GE Ventures and others, the Guardian XO will have a wide range of applications, including at factories, mines and construction sites. Rather than replacing human labor, though, the exoskeleton supplements it. Take drywall installation, where workers have to lift sheets as heavy as 200 pounds: The machine can take a load off, but the work of installing remains too delicate for full automation.
Power up: Full-bodied exoskeletons have been under development for decades, but were held back by their need to be plugged into a power source. But after assiduous R&D, plus great advances in battery technology, Sarcos engineers were able to build the Guardian XO to run on less than 10 percent of the power required by early iterations. “The first prototype 10 years ago was hydraulically powered and drew 6,000 watts,” said Kristi Martindale, Sarcos chief marketing officer. “Now it’s less than 400 watts of power for the whole suit.” The machine can operate for a full eight-hour shift without having to be plugged in and — unlike the human wearing it — doesn’t require bathroom breaks.
The only drawback? Terrible at conversation. Click here to learn more about the Guardian XO.
GEAR HEADS
Recently, a technician in Singapore put in a call to his colleague back at the office. The technician was peering into a jumble of wires that needed to be plugged back in correctly — problem was, all of them were black. Bomb-squad action movie? Nope: electrical substation, which had undergone a planned 24-hour outage. A fault had occurred as crews were planning to take it back online. GE field service manager Nicolas Godingen talked the technician, an electrical engineer, through the process of sorting the wires, and eventually power flowed through the substation again. Godingen gave his assistance over the phone, but his team is also embracing technology that makes this kind of communication even easier: wireless smart helmets, which allow technicians onsite to access expert guidance from anywhere in the world.
Hail fellow helmet: Tech companies have had mixed results selling augmented-reality gadgets like smart glasses to everyday consumers. But those products have found a niche in industrial settings like substations and power plants, where engineers don’t mind wearing futuristic-looking devices if it helps speed things along. Equipped with mini screens, cameras and audio communication, smart helmets look just like typical hard hats but allow the wearers to seamlessly communicate with experts working out of the office. The ones used by Godingen’s team, for instance, are Bluetooth-enabled and overlay digital images on the wearer’s field of vision. The helmets have less obvious benefits, too: Experts can be in two places at once without having to get a visa for international travel.
Wirelessly transport yourself here to learn more about how smart helmets are helping GE engineers on the job.
HOW TO SURVIVE THE ROBOT REVOLUTION
So robotic exoskeletons won’t be replacing drywall installers anytime soon — but what about other forms of automation and other kinds of work? A new analysis from the Brookings Institution breaks down the susceptibility of jobs to automation by factors like education level and skill set. For instance, the “automation potential” of jobs requiring a bachelor’s degree or more is just 24 percent — compared to 55 percent for those jobs that require less than a bachelor's.
Taking charge of business: As automation displaces lower-skilled workers, they’ll be in less demand and thus forced to accept lower wages, according to Brookings senior fellow Harry Holzer, who recommends state and federal policies to aid at-risk workers. Among those most vulnerable are food preparation assistants, cleaners, and workers in the agricultural, forestry and fishery industries. Safer jobs include teachers, lawyers, and hospitality and retail roles. Another bright spot? Digital mobility, which includes building and maintaining autonomous vehicles. With 9.5 million jobs in 2017 — more than finance, real estate or administrative services — that sector is still growing.
Brookings Now rounds up all this and more recent research on automation and the future of work. Learn more here.
— VIDEO OF THE WEEK —
Quote: GE Reports. Image: Sarcos.
ENJOY THIS NEWSLETTER?
Please send it to your friends and let them know they can subscribe here.