3D printing and other additive manufacturing methods, used to print human bones as well as jet engine parts, were popular themes for GE Reports readers in 2017. Other top stories covered the latest technology for power plants, jet engines, healthcare and STEM. Here’s our selection
An Epiphany Of Disruption: GE Additive Chief Explains How 3D Printing Will Upend Manufacturing
[embed]https://www.facebook.com/thefutureisnowbymic/videos/1387491274694234/[/embed]
Mohammad Ehteshami, who leads GE Additive, says that additive manufacturing methods like 3D printing are coming into the mainstream and disrupting how companies make things. “Additive is so powerful that you either lead it or you get victimized by it,” Ehteshami says.
Survivor: This Woman’s Battle With Leukemia Is Pointing The Way To The Future Of Healthcare
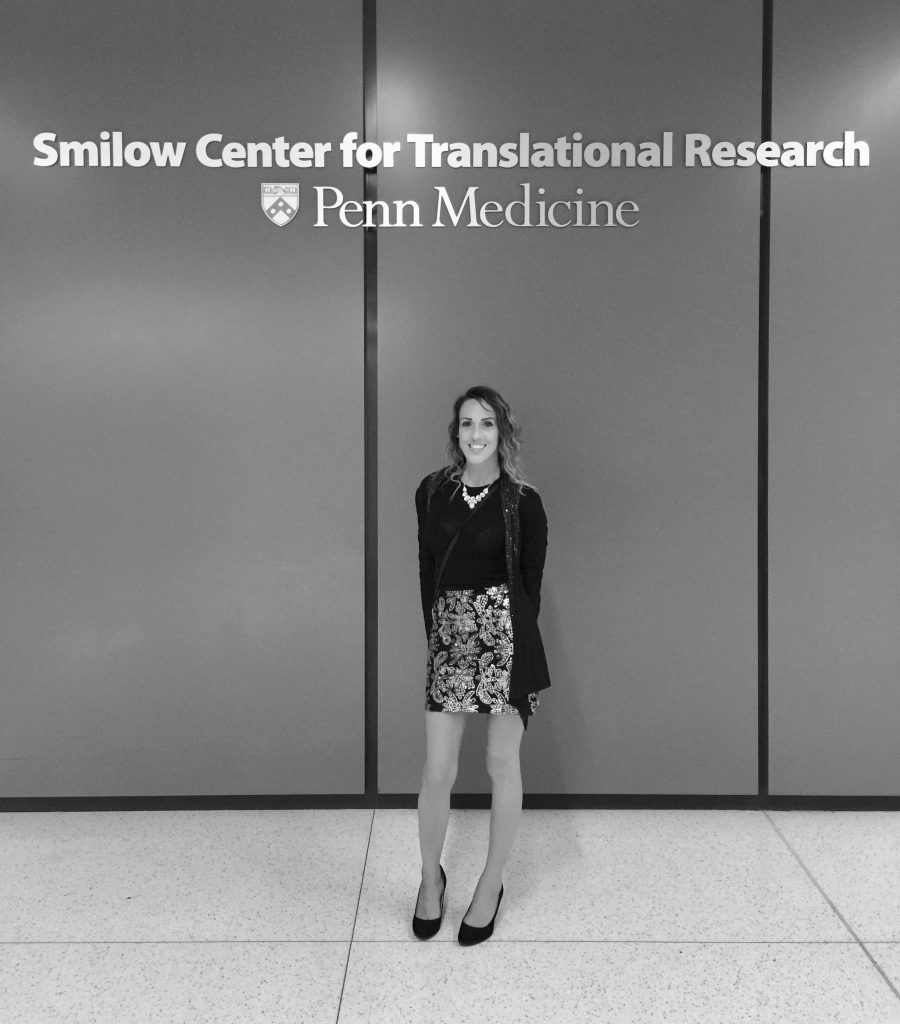
When Nicole Gularte discovered that her acute lymphoblastic leukemia had returned yet again, she did something unexpected: She let the disease relapse so she could qualify for a trial of a promising new cancer treatment called CAR T-cell therapy. What happened next is nothing short of amazing. Cell therapy involves extracting a patient’s T-cells — the immune cells that fight against infection — and reprogramming them to find and kill cancer. Gularte made the right call. A year after her treatment, her disease is still in remission.
Mission Critical: GE’s New Digital Center In Atlanta Is Using Data From Power Plants To Spot Trouble And Save Money
[embed]https://www.facebook.com/GE/videos/1502002026534753/[/embed]
GE's global power plant monitoring center in Atlanta is a place like no other. The largest facility of its kind in the world, it looks like a smaller version of NASA’s mission control center. It has banks of computers and a wall-to-wall, colorful LED screen flashing real-time operating conditions inside 5,000 turbines, generators and other equipment churning away at 900 power plants located in 60 countries and serving 350 million people.
The facility, called the Monitoring and Diagnostics Center, is connected to computers that can process billions of data points every day and spot potential problems before they get out of hand. Recently, it spotted a faulty bearing that could have caused an expensive power outage. “The plant never felt it, never heard it, never saw anything,” said Justin Eggart, who works at the center. But the center's software — which runs on Predix, GE's app development environment for the industrial internet — did.
GE Just Turned The World’s Most Powerful Jet Engine Into A 65-Megawatt Power Plant
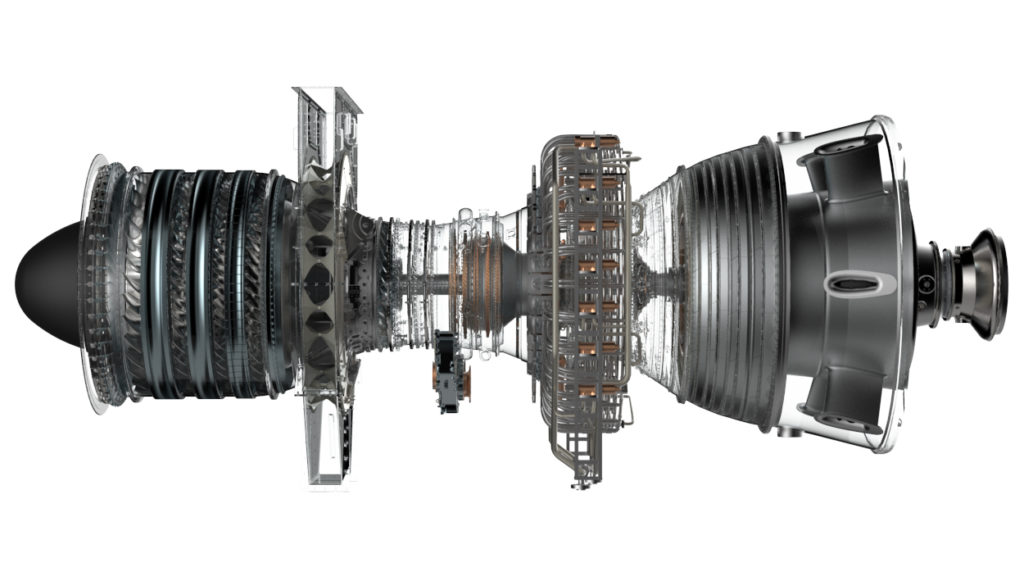
GE engineers took the world’s largest jet engine and turned it into a power plant. The machine’s beating heart comes from the GE90-115B, capable of producing 127,900 pounds of thrust, according to “Guinness World Records.” The electricity generator, which GE calls LM9000, will be able to produce a whopping 65 megawatts — enough to supply 6,500 homes — and reach full power in 10 minutes.
Where Turbines Are Born: An Inside Look at GE’s Big Iron Maternity Ward
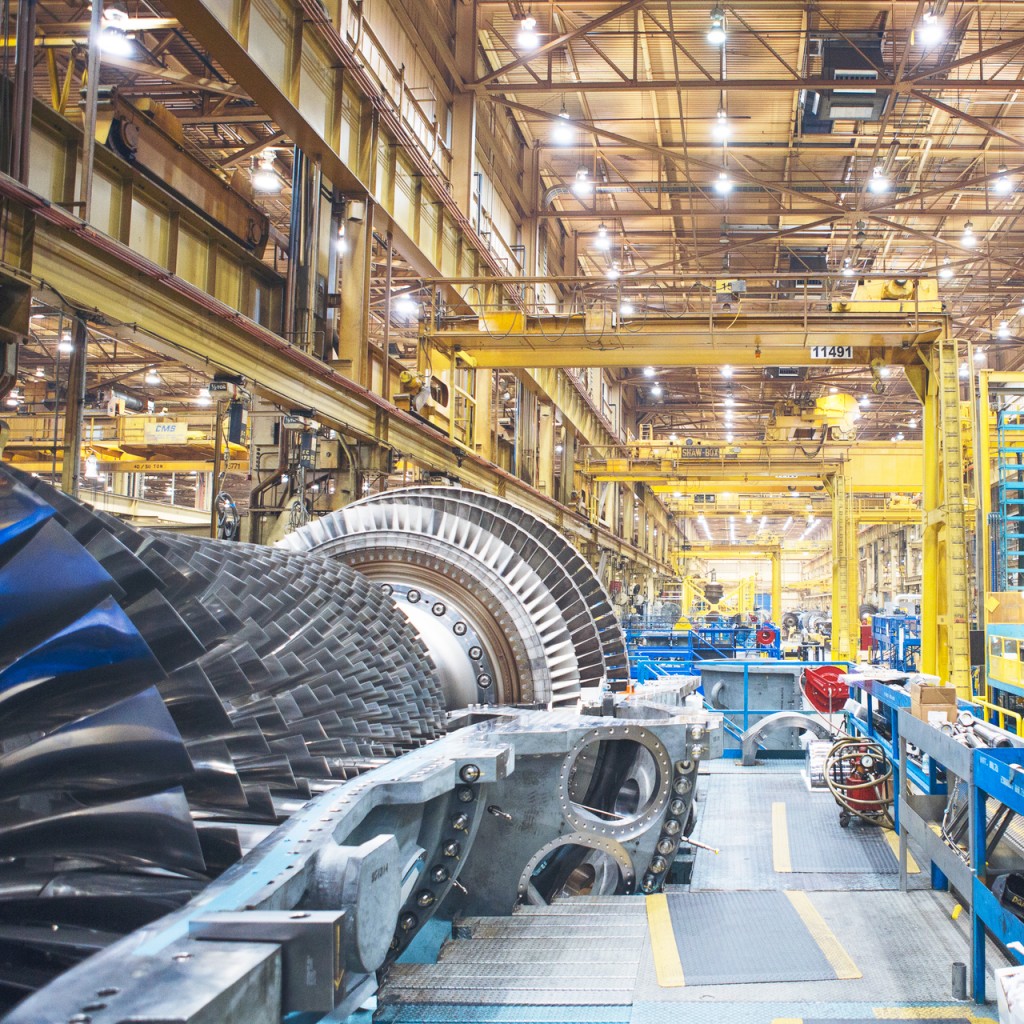
There are places in the world that make us feel small and force us to marvel at the skills and ambitions of their architects and engineers. They include cathedrals in Europe, NASA’s Cape Canaveral rocket launchpad and the Panama Canal. GE’s gas turbine plant in Greenville, South Carolina, may not be on everyone’s list. But it comes close.
Image credit: GE Power.
Engineered By Women For Women: Colleagues Band Together To Take Fear Out Of Breast Screening
[embed]https://www.facebook.com/thefutureisnowbymic/videos/1296508093792553/[/embed]
Fearing test results can be a major deterrent to proper health care. But what about when patients fear the test itself? Mammograms, though the most effective breast cancer screening tool for most women, are one example. One in 8 women are diagnosed with breast cancer, yet studies have found that as many as 30 percent of women in the United States, and 40 percent in Europe, skip the mammogram. So a group of engineers at GE Healthcare designed the Senographe Pristina, a mammography machine that “mixes science with empathy.”
The team used feedback directly from doctors, technicians and patients, and was largely female. Their scanner has subtle features designed to make the experience more pleasant — from smooth, round surfaces to arm rests and relaxing LED lights. Clinics with the Pristina are also taking cues from the device to improve the feel of the exam rooms themselves, with features like calming music and walls painted with warm colors. Studies have shown that the screening can reduce breast cancer mortality rates by 20 percent, so improvements to make patients feel at ease are crucial. The Pristina is a great example.
New One-Of-A-Kind Turboprop Engine Delivers Jet-Like Simplicity To Pilots
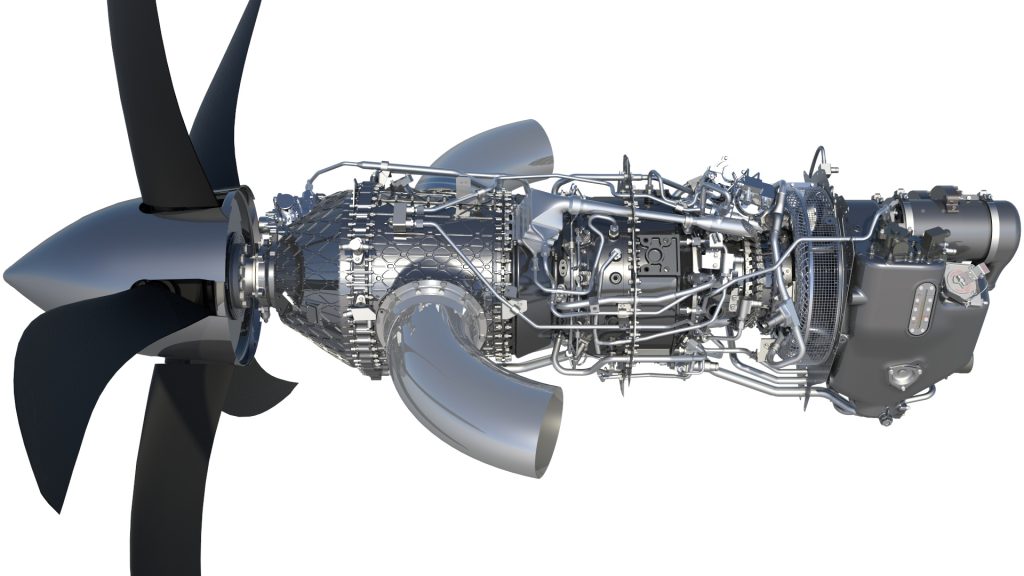
For the first time, GE test engineers just fired a new Advanced Turboprop engine with large sections made on a 3D printer. 3D printing and dozens of other new technologies used in a civilian turboprop engine allowed the team to combine 855 separate components into just 12, shave off more than 100 pounds in weight, improve fuel burn by as much as 20 percent, give the engine 10 percent more power and simplify maintenance. “This engine is a game changer,” says Paul Corkery, general manager of the Advanced Turboprop program.
GE And Apple Team Up To Bring The Industrial Internet To The iPhone and iOS
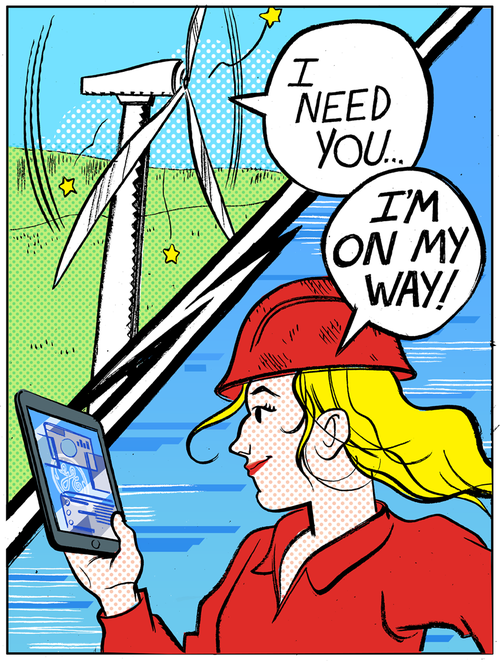
The Industrial Internet is getting the Apple treatment. GE and Apple announced at GE’s Minds + Machines conference in October that they will bring Predix, GE’s app-development platform for the Industrial Internet, to Apple’s iPhone smartphones and iPad tablets, used by 700 million people around the world.
Image credit: GE Reports.
An Engineer’s Dream: GE Unveils A Huge 3D Printer For Metals
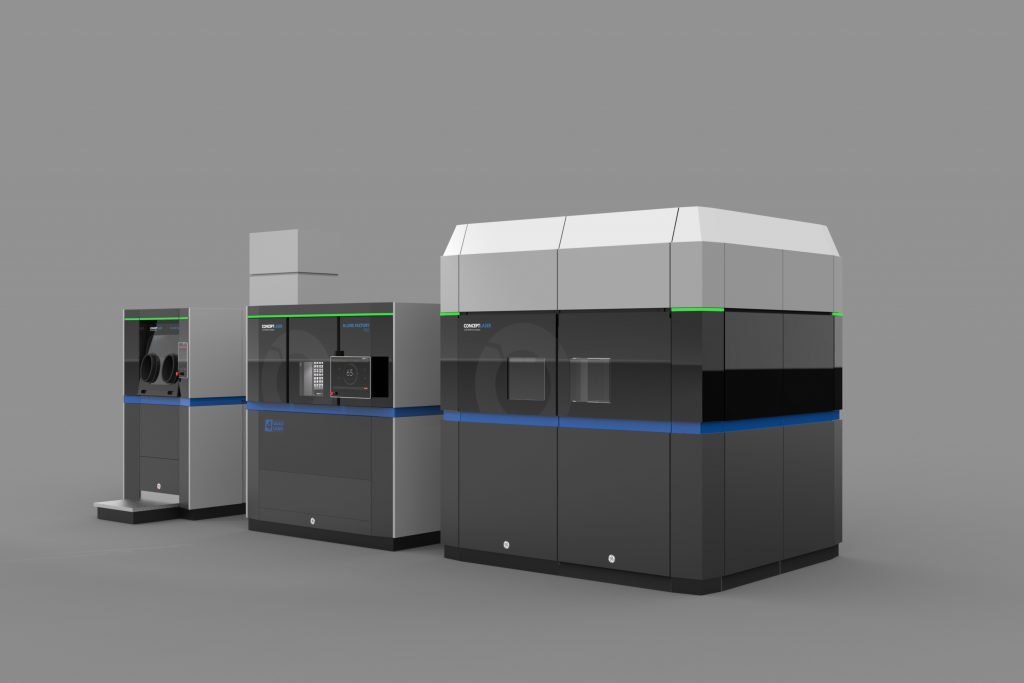
In November, GE unveiled a beta version of the world’s largest 3D printer for metals, which uses a laser and a powder bed to make parts. It is capable of printing parts as large as 1 meter in diameter directly from a computer file by fusing together thin layers of metal powder with a 1-kilowatt laser. And because the technology is scalable, the machine has the potential to build even bigger parts.
Image credit: GE Additive.
Da Vinci Code 2.0: How 3D Printing And Digital Technologies Are Altering The Face Of Aircraft Engine Manufacturing In Italy
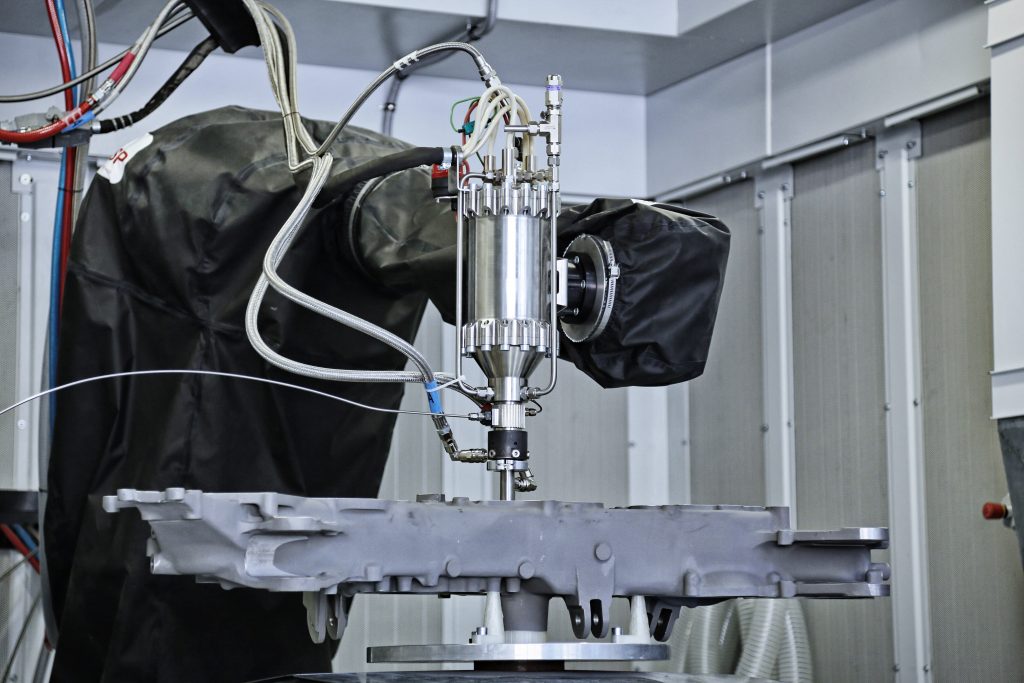
Additive technologies like 3D printing are revolutionizing manufacturing in much the same way as the internet transformed information and shopping. Instead of removing material, these techniques grow parts from the ground up by either depositing or fusing layers of material. Engineers can design parts on their computers and then send their drawings directly to a 3D printer. The machines break down the design files to individual layers and join them together in the right pattern. “There are no limits to complexity,” says Dario Mantegazza, a manufacturing engineer at Avio Aero, a GE Aviation company. “You can create hollow structures if you want, or something like a bone.”
Bone Machine: 3D Printing Is Revolutionizing Plastic Surgery
[embed]https://www.facebook.com/thefutureisnowbymic/videos/1268575106585852/[/embed]
Plastic surgeon Laurent Lantieri has been working with Materialise, a Belgian additive manufacturing and design company, to build bone implants for his patients. Using a 3D CAT scanner, Lantieri creates a 3D scan of a patient’s face, for example. Materialise clinical engineers then use a virtual 3D model of the patient’s undamaged bones, based on a CT scan, as a guide to building patient-specific implants that replace the damaged bones. A shattered cheekbone on the left side of a person’s face is replaced with a mirror image from the right side. A destroyed orbital socket can be made whole by matching it to the remaining socket.
School’s In: GE’s New “Brilliant Learning” Program Will Train Workers For Jobs Of The Future
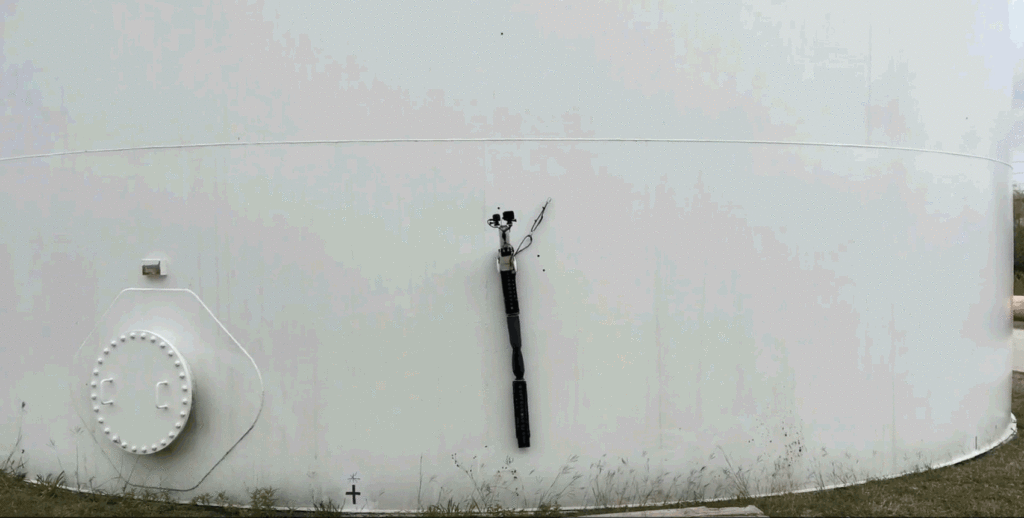
Last spring, GE launched a new “brilliant learning” program for employees around the world. It includes “massive open online courses” in several languages, workshops, “immersion boot camps on lean manufacturing” and other training designed to help factory employees get ready for the arrival of 3D printing, big data, robotics, digital and lean manufacturing, and other advanced technologies.
Top image: The Belgian additive manufacturing and design company Materialise uses a virtual 3D model of the patient’s face, based on a CT scan, as a guide to build patient-specific implants to replace damaged bones. Images credit: Materialise.