The world’s fastest and largest liners, including Normandie and Queen Mary 2, sprung from its dry docks. The port also serves as a transit hub for the fuselage and wings that make the double-decker Airbus A380, the world’s largest passenger aircraft.
There’s more. GE Renewable Energy makes and tests the Haliade, one of the world’s largest and most powerful wind offshore turbines, in a new 35-acre factory just east of the city. “This is our cathedral,” says Pascal Girault, the plant’s manager.

Standing twice as tall as the Statue of Liberty, each Haliade can generate 6 megawatts, enough to power 5,000 homes. The turbine has a 150-meter diameter rotor that sweeps over an area wide enough to fit three soccer fields.
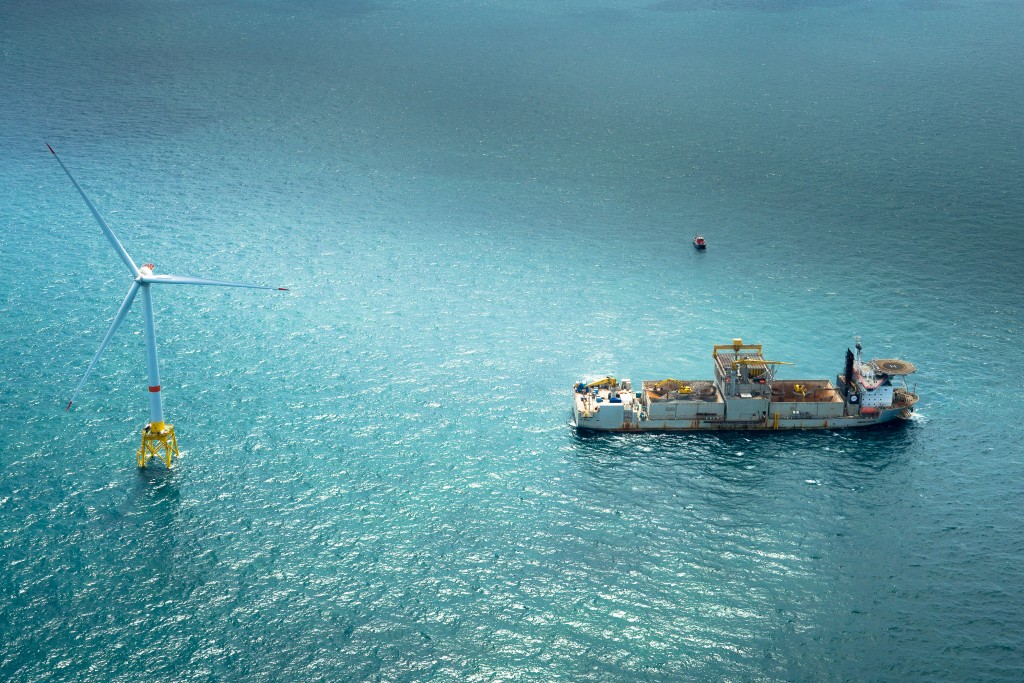
When GE Reports visited the plant in late March, there were five Haliades moving down the production line. They will power America’s first offshore wind farm located three miles off the coast of Block Island, Rhode Island. The wind farm is scheduled to come online at the end of 2016 and generate 125,000 megawatt-hours of electricity annually. Here’s how they are made:

Workers at the Saint-Nazaire factory manufacture generators and assemble nacelles for the Haliade. The nacelle is the casing that shelters the generator and other equipment on top of the tower. There are 170 people working in the plant in two shifts and GE has plans to bring that number to 300. Electro-mechanics make up about 60 percent of the workforce. A fifth of the workers are engineers.
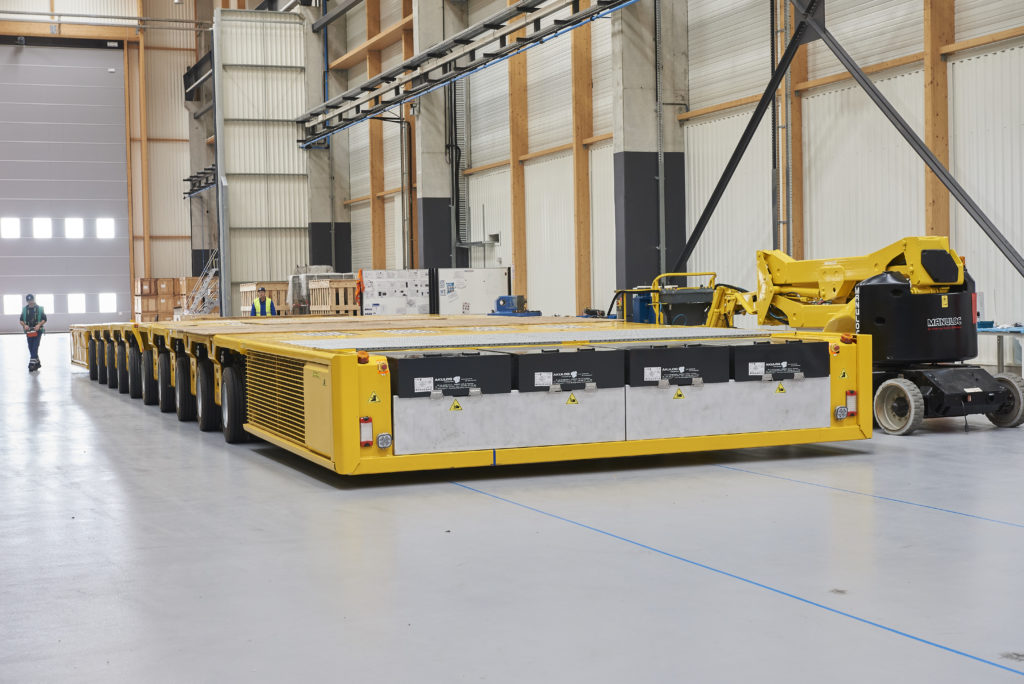
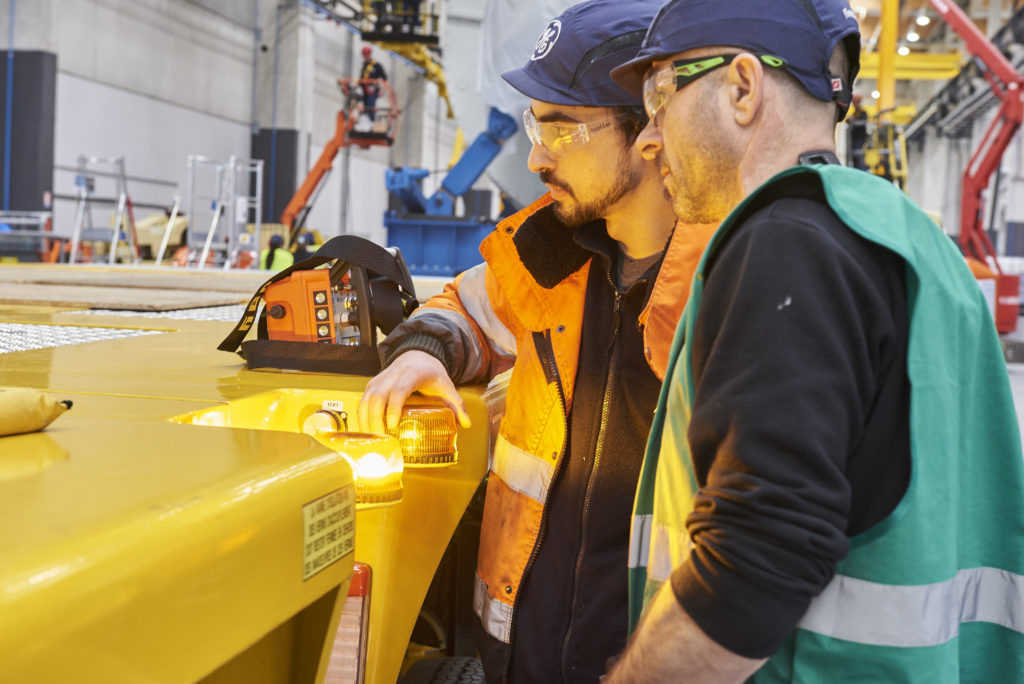
The plant is located on the banks of the Loire and many of the large Haliade components arrive by ship. The team begins by unloading massive stator and rotor steel rings for the 6-megawatt permanent magnet generator. They place them on large yellow and orange multi-wheelers and move them inside the plant. Since the generator is driven directly by the rotor – there is no gearbox - it has fewer rotating components. This makes it more reliable and less expensive to maintain.
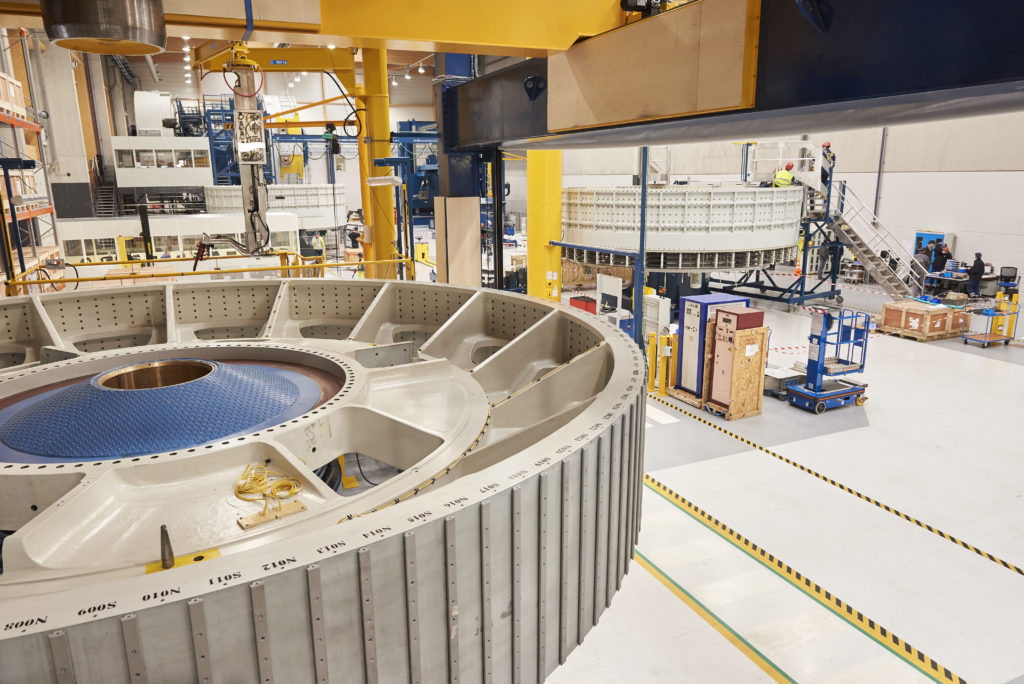
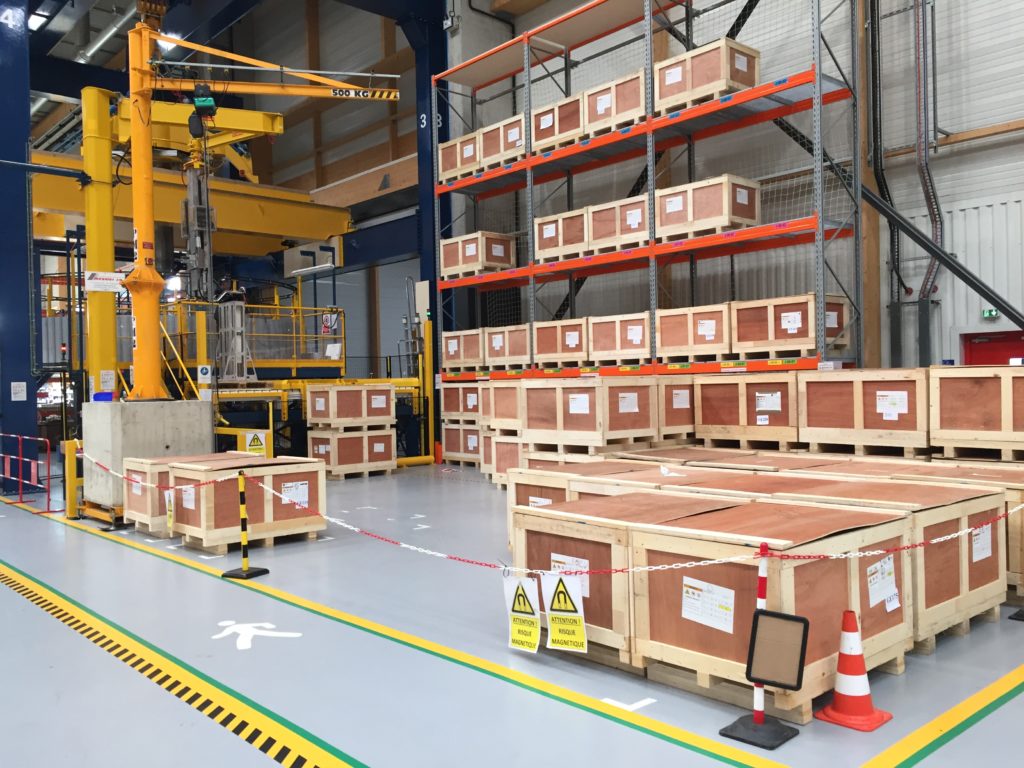
Once inside the factory, workers slide the parts on innovative air cushion movers. The movers allow them to position the heavy parts for assembly without relying on cranes. One team begins by attaching 256 magnets made in Japan to the rotor. When the wind spins the rotor, the rotating magnetic field generates electricity. “The magnets are so strong the rotor makes electricity by just turning it from north to south on the shop floor,” says operations manager Jean-Baptiste Vilcoq.
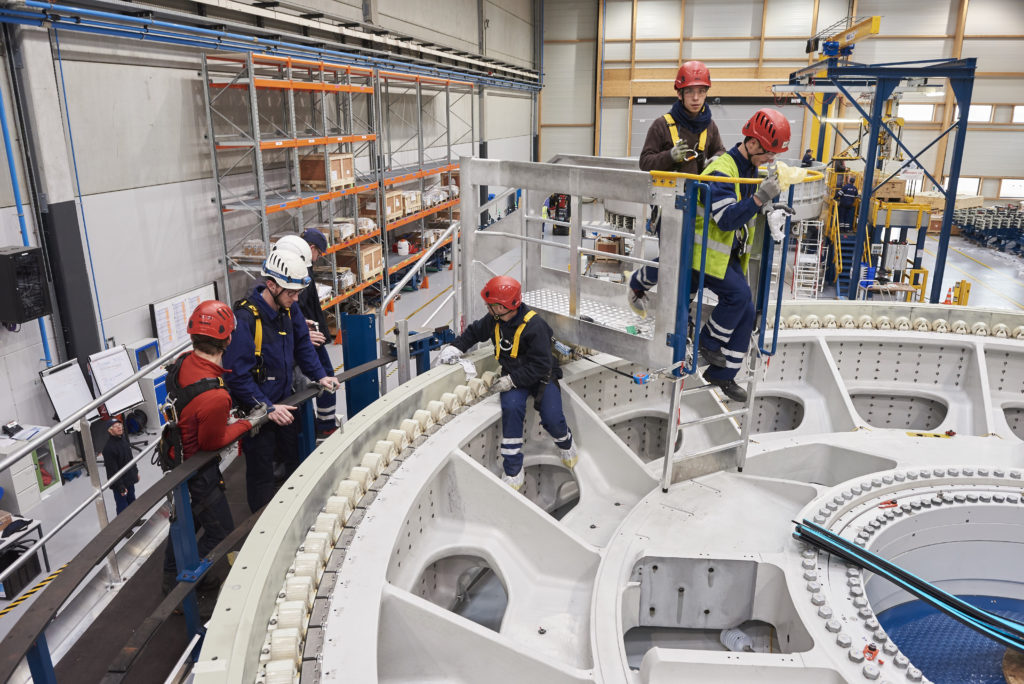
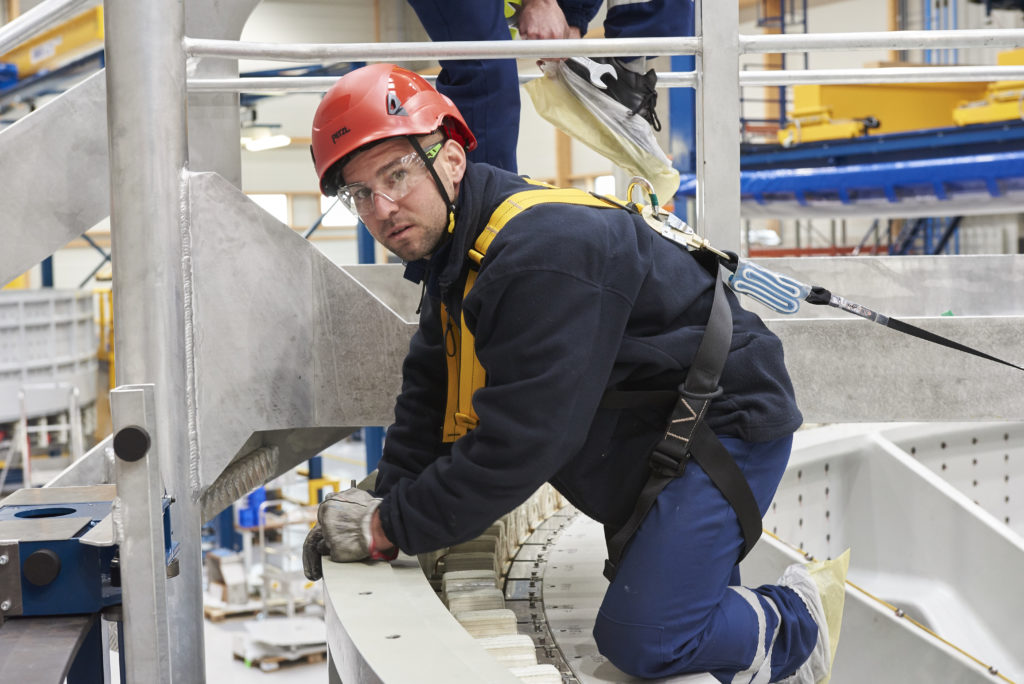
Nearby, workers start assembling the stator, which is the outer ring of the 150-ton generator. The ring, which measures nearly 25 feet in diameter (7.6 meters), holds 144 magnetic poles to three bands of coppers bars – one for each phase - that carry 900 volts. There’s also a hydraulic cooling system that keeps the generator's internal temperature down.
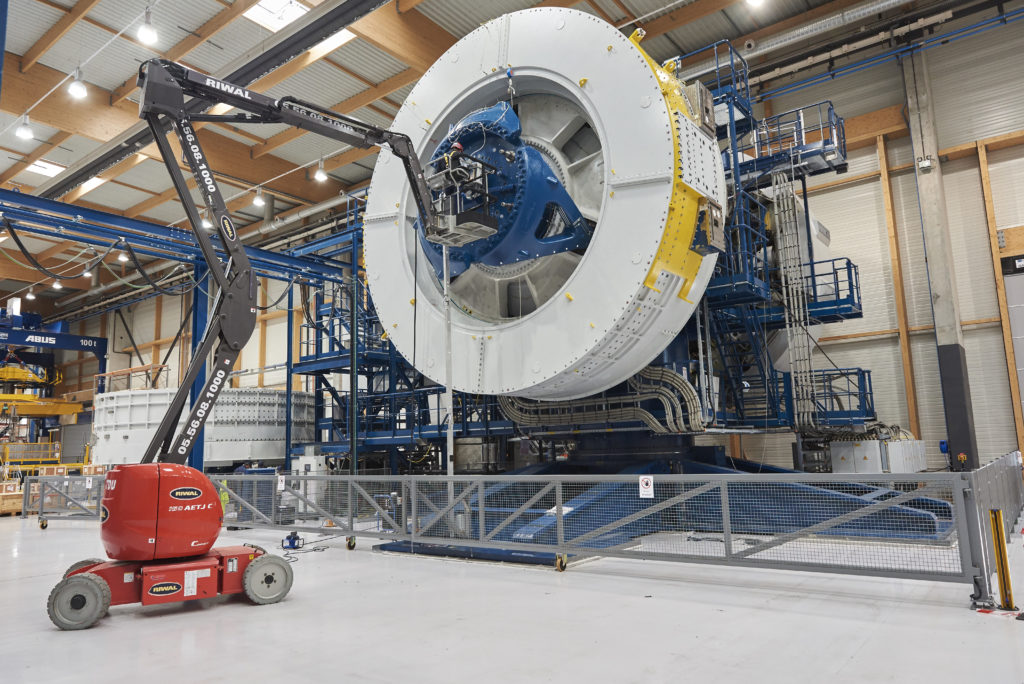
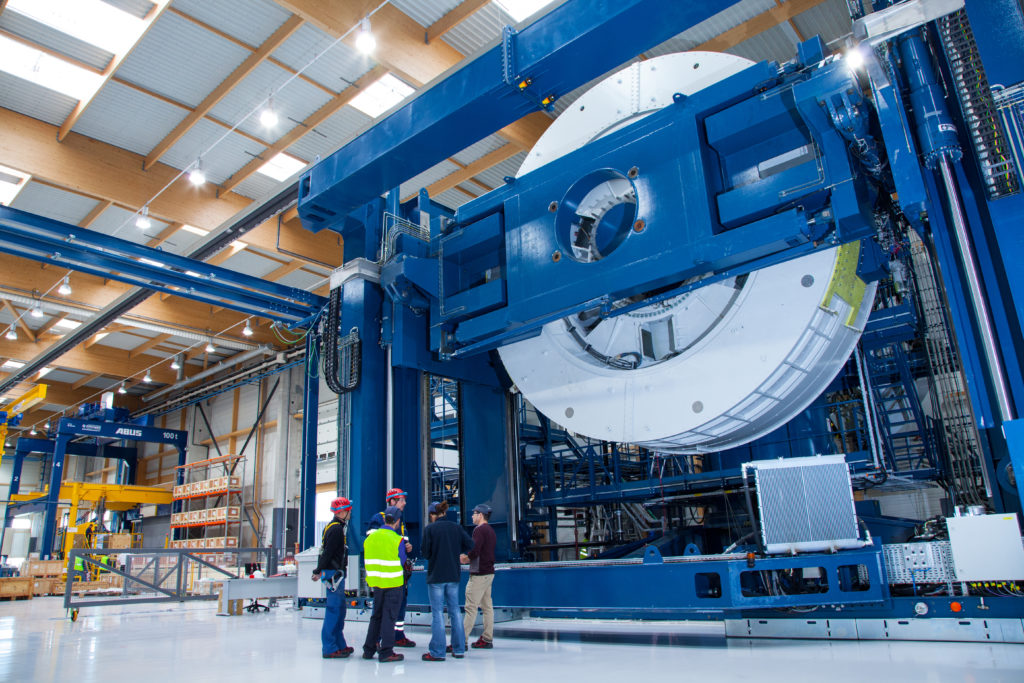
The next step involves fitting the rotor inside the stator, flipping it on its side and moving the assembled part to a huge, custom-built rig for testing. The rig includes a one-of-a-kind, 7.3-megawatt electrical motor that simulates the wind and spins the generator.
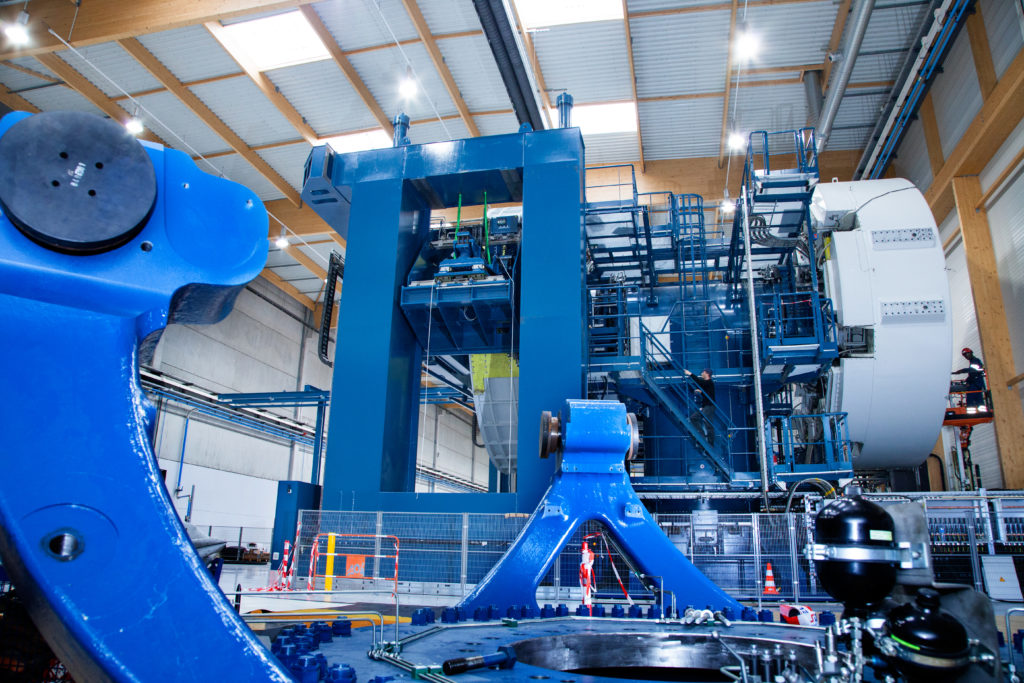
Since the generators that are being tested are rated to produce 6.5 megawatts at full load, workers use the electricity to drive the test rig and reduce stress on the local grid. Workers test everything from vibrations to electrical output. The Haliade was designed to spin up to 11.5 rpm, but the rig can go up to 15. The testing takes about four days. The plant was built around the test rig, Vilcoq says. “We don’t have to send the generators out for testing and we know about any problems right away. It speeds things up immensely.”
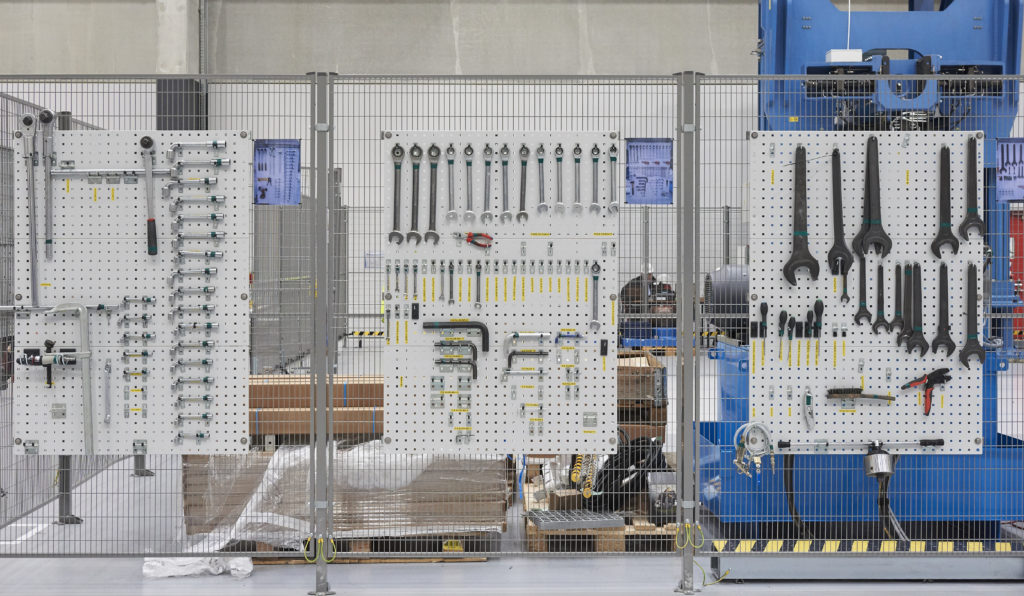
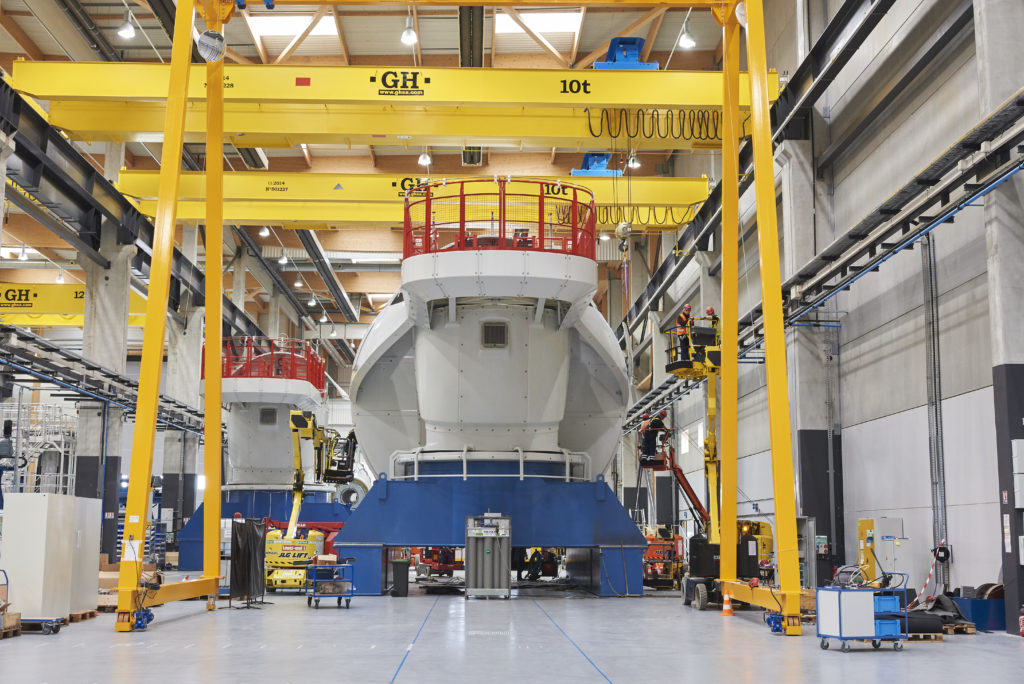
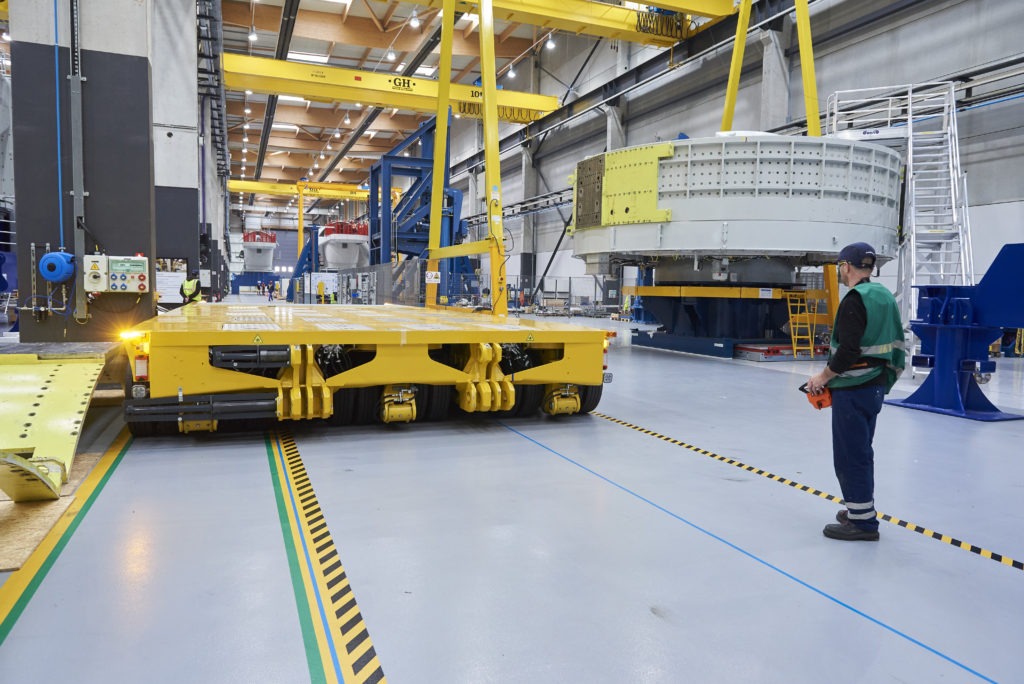
The completed generator moves to another assembly hall located next door where workers are assembling the nacelles (below).
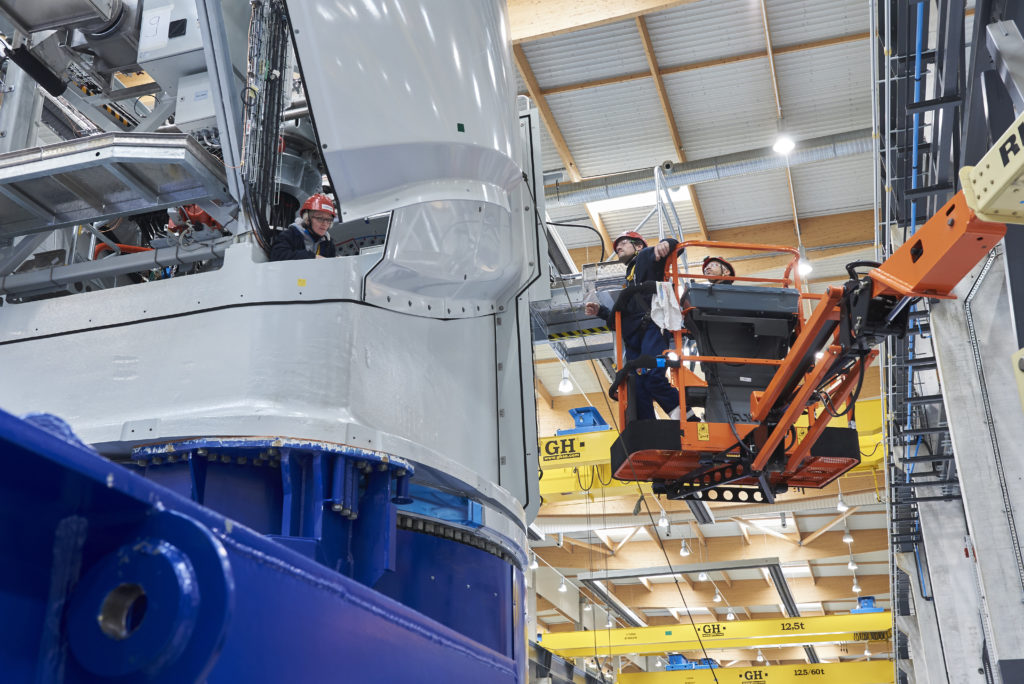
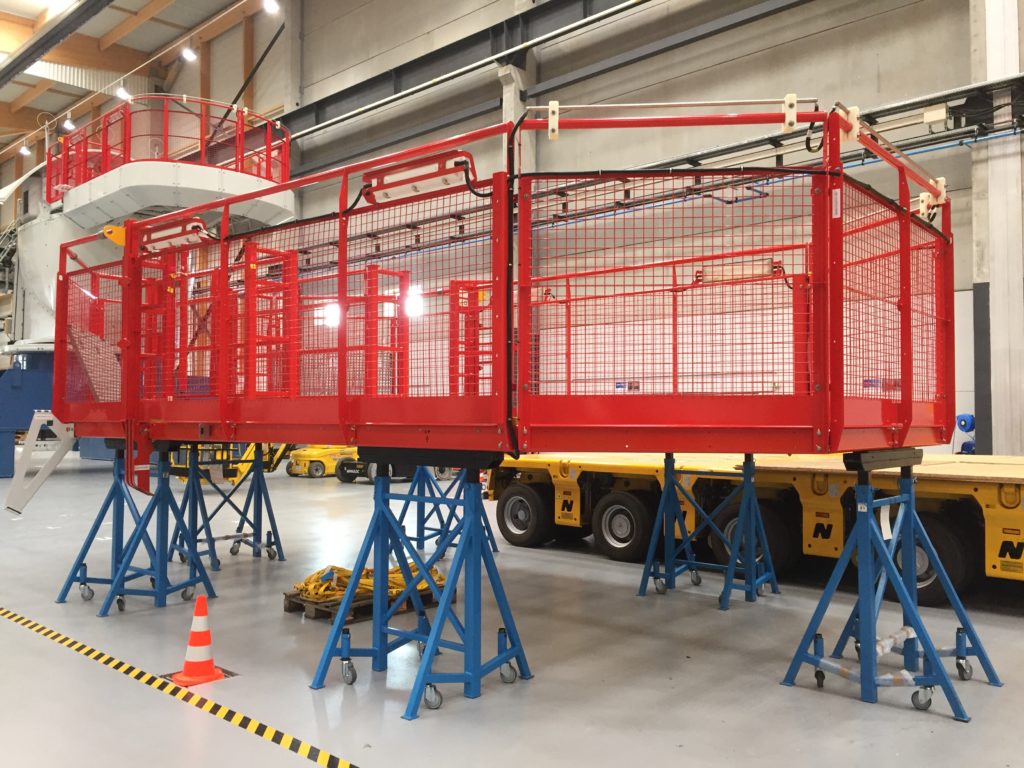
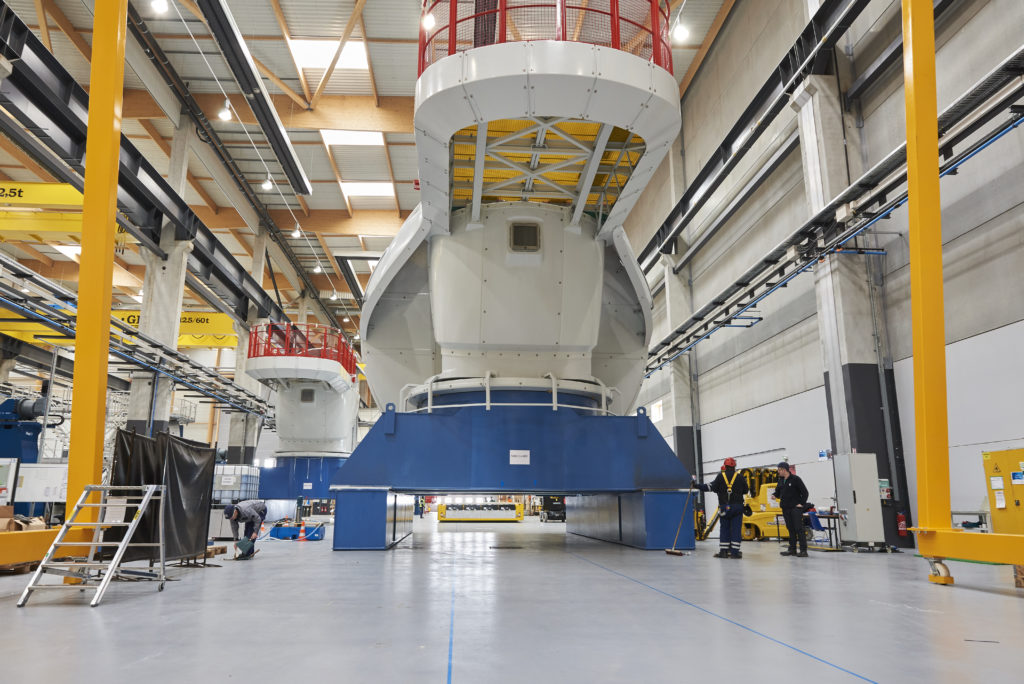
After attaching the generator to the front of the nacelle, the assembly moves on a multi-wheeler to a station down the line where another team attaches an orange helicopter winching area. Maintenance workers use it to access and leave the turbine when the seas are too rough to arrive or depart by boat.

Further down the hall, another group is assembling the hub of the wind turbine. The hub supports the rotor blades and controls their pitch and also the yaw of the turbine.
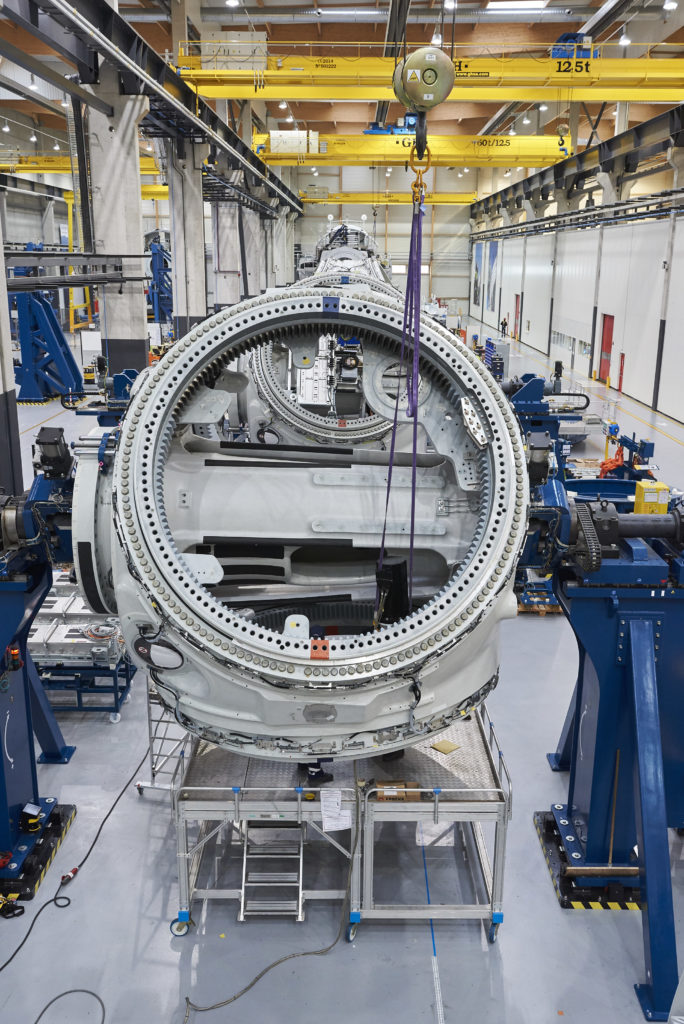
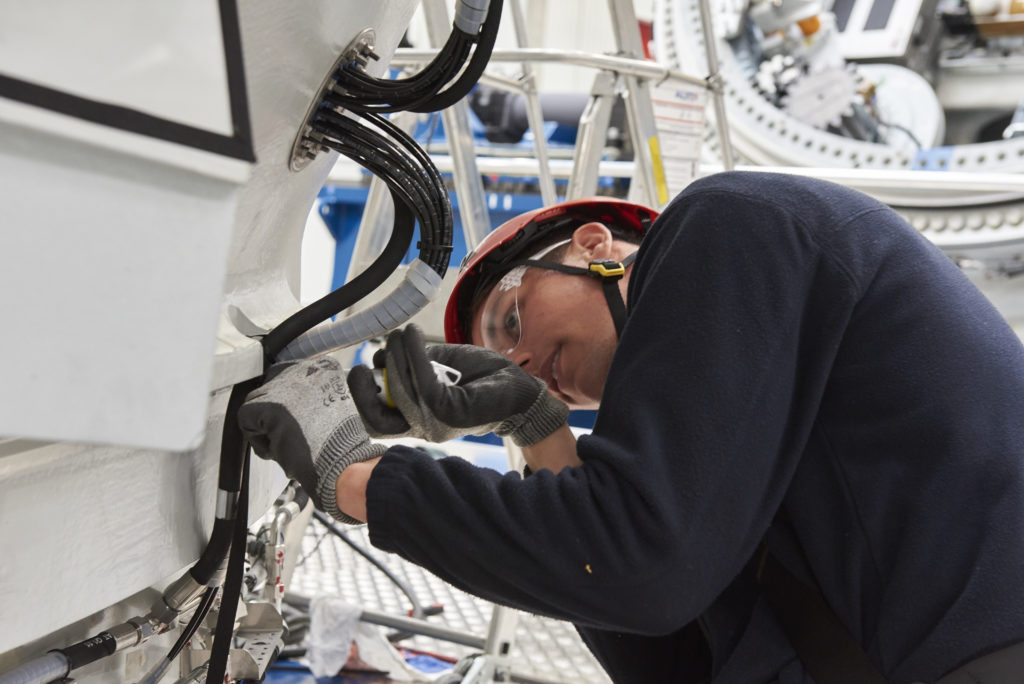
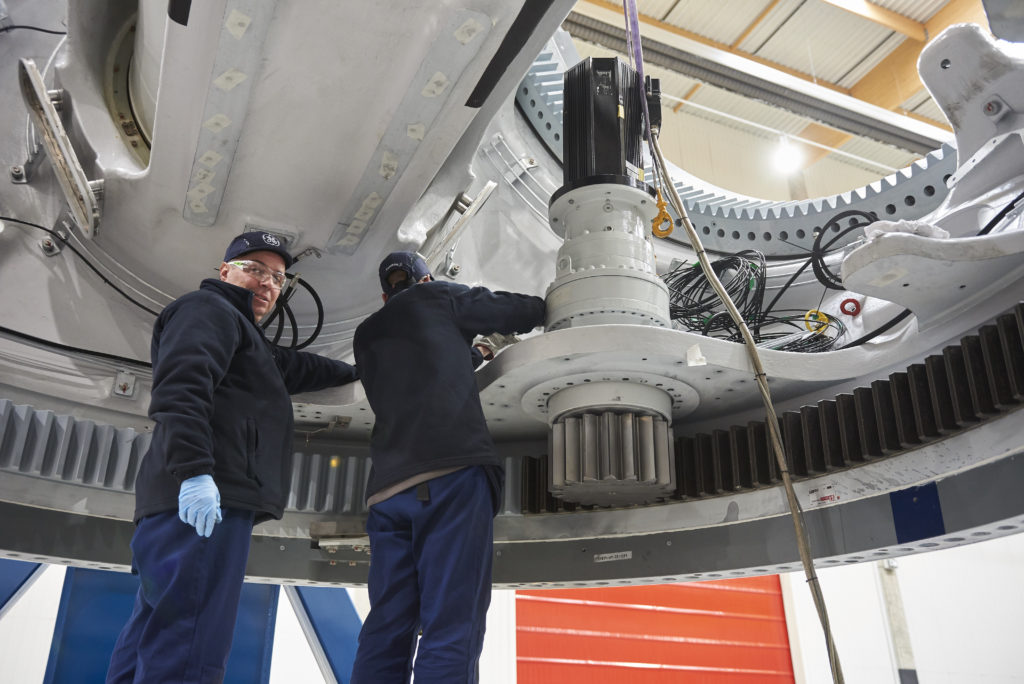
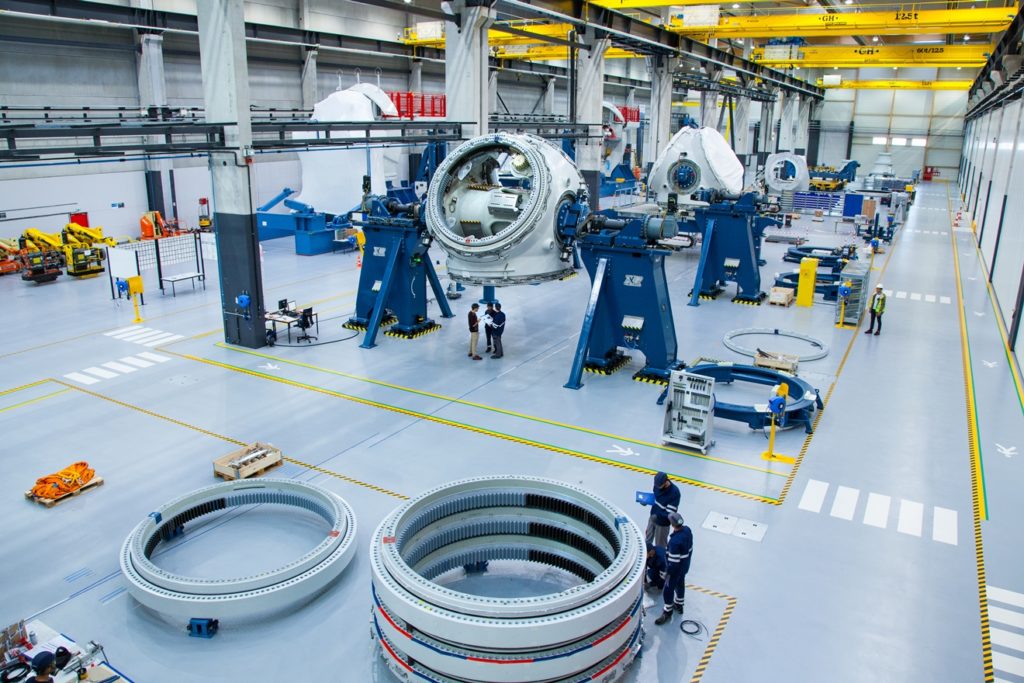
On this line, workers install large blade bearings and powerful electrical motors that further control the pitch of each of the three blades. The blades measure nearly 250 feet (74 meters) each. The motors set the blade angle and turn the area exposed to the wind to maintain high torque yield.
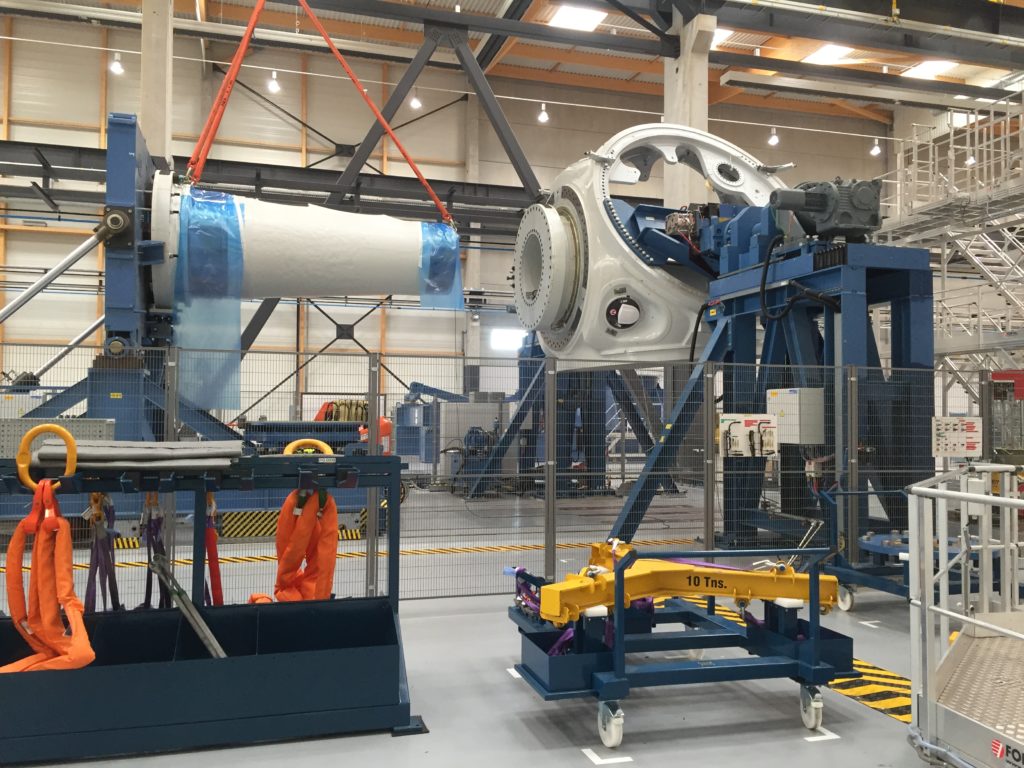
The team also installs special rotor bearings, which directly transfer unwanted forces, or load, from the rotor to the steel main frame of the nacelle and into the tower of the turbine. They bring the hub and nacelle together with a patented elastic coupling. The steel coupling includes rubber elements that also help deflect damaging loads and extends the life of the drivetrain. GE calls the whole system Pure Torque. It redirects as much as 90 percent of torque that can’t be used to generate power to the tower.
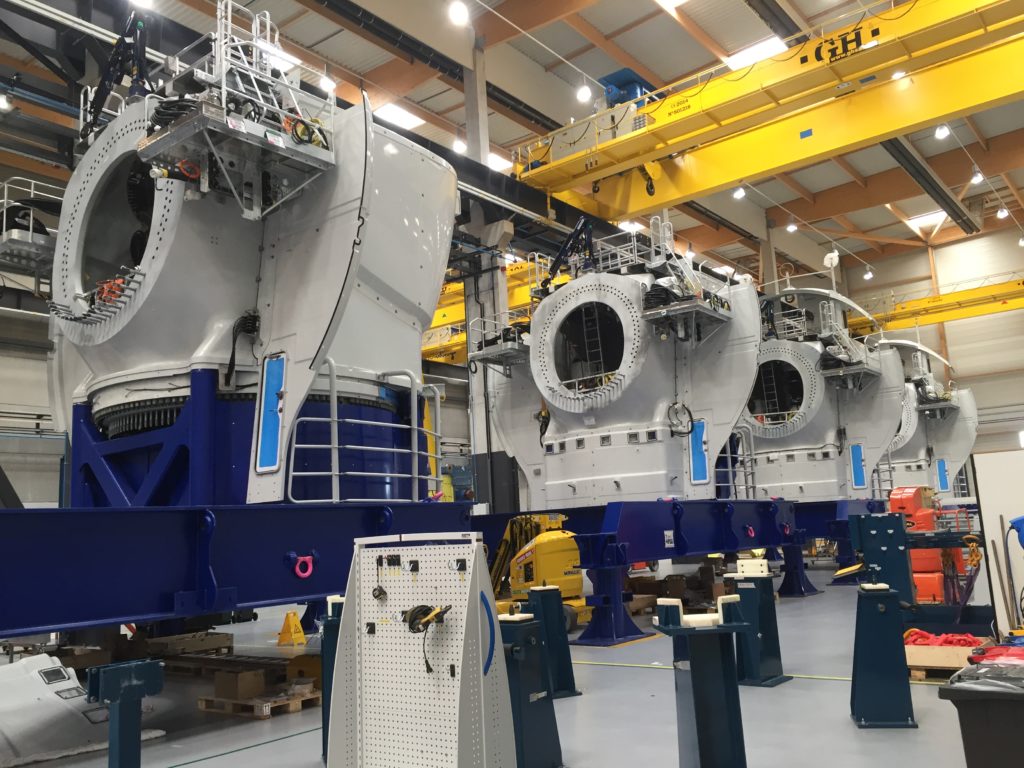
Workers complete the assembly by attaching maintenance and monitoring tools to the nacelle such as a small crane, an anemometer for measuring wind speed and direction and a webcam.
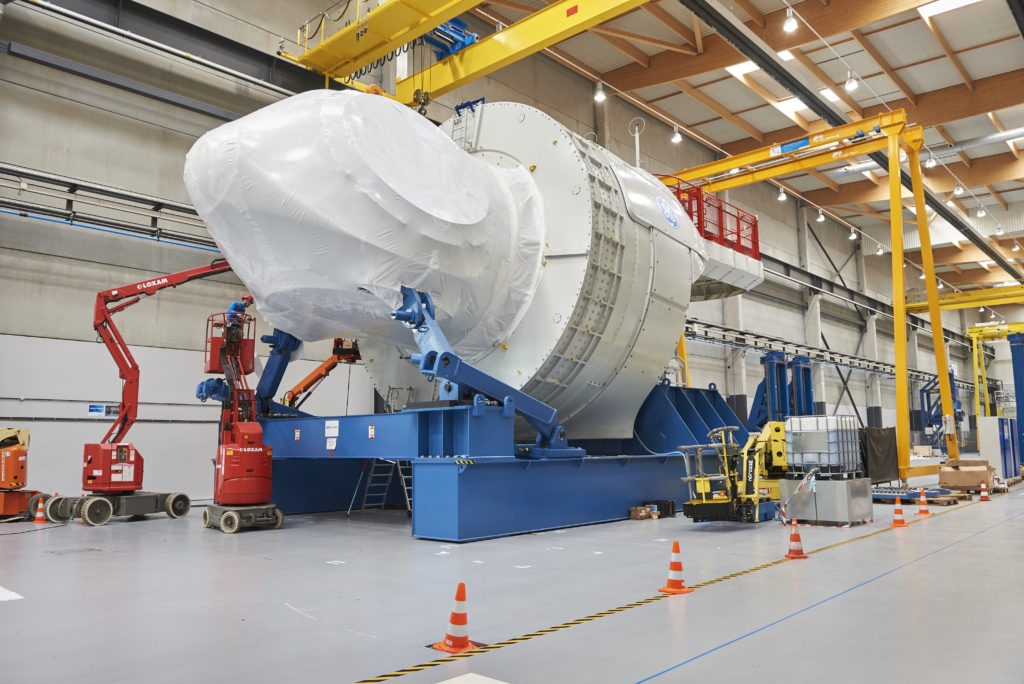
At the end, they spray the nacelle with recovered rainwater to make sure that it is water-tight and protects the machinery and electronics that connect the windmill to operators via the internet. Finally, they shrink wrap the machine, place it on another multi-wheeler and send it to the nearby Saint-Nazaire port.
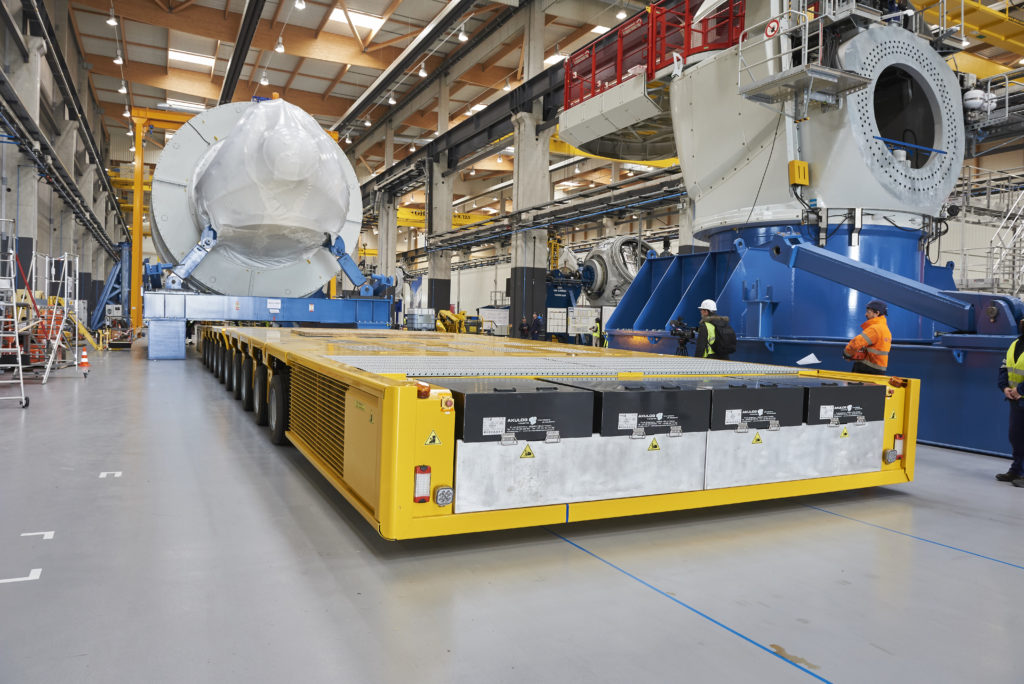
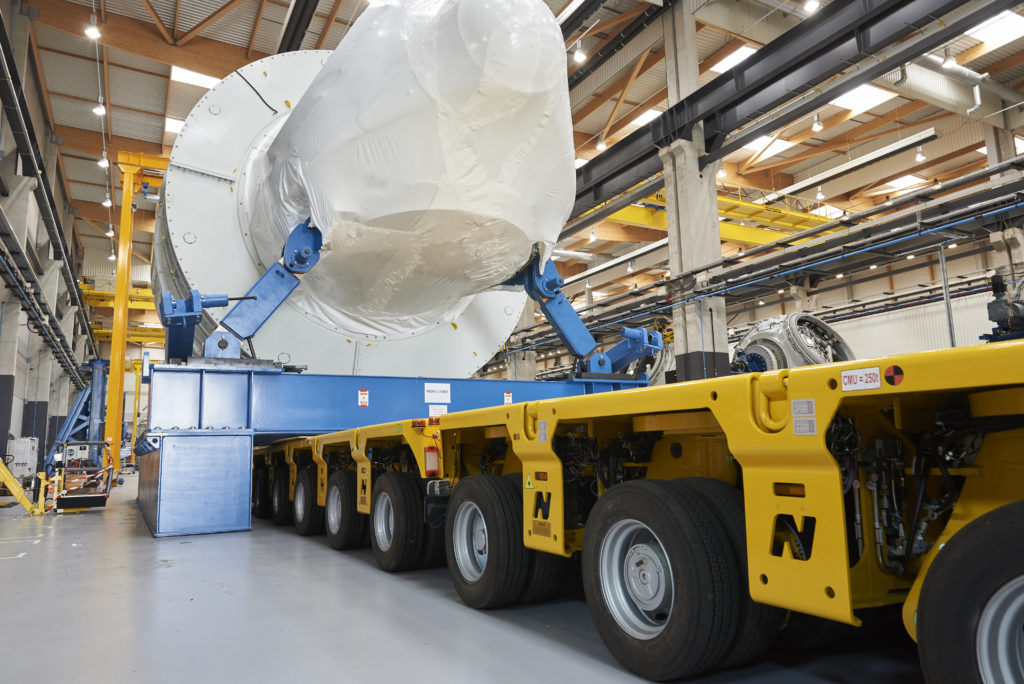

![_AND3842[1]](http://www.ge.com/news/sites/default/files/Reports/uploads/2016/04/13194615/AND38421-1024x684.jpg)

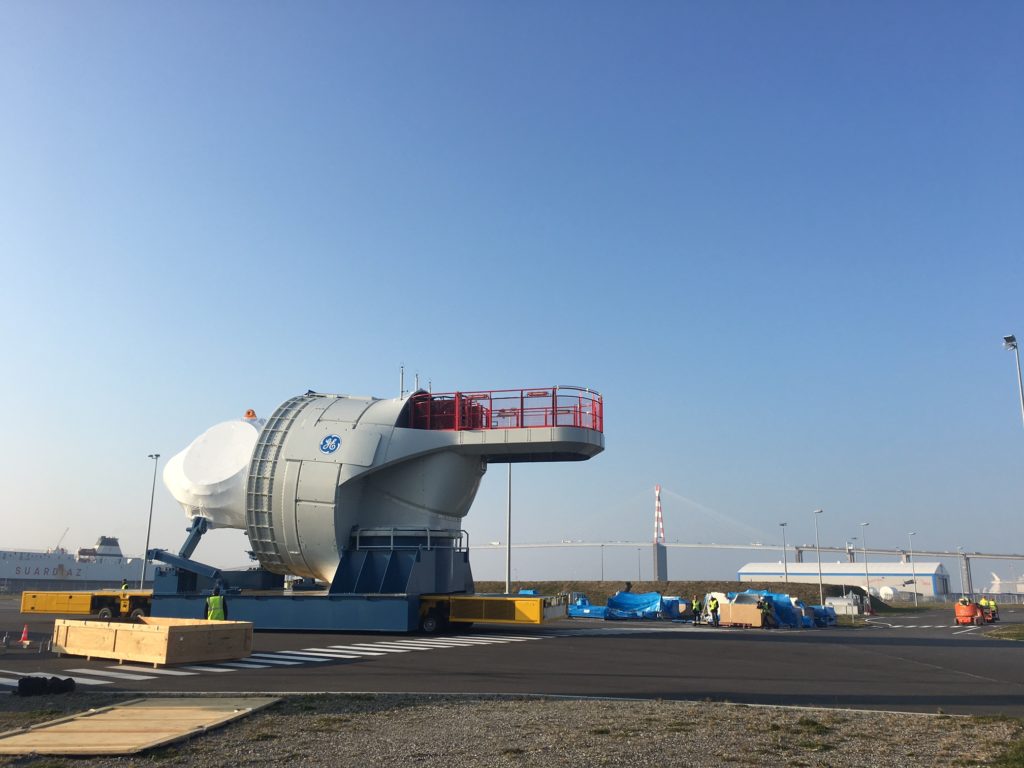
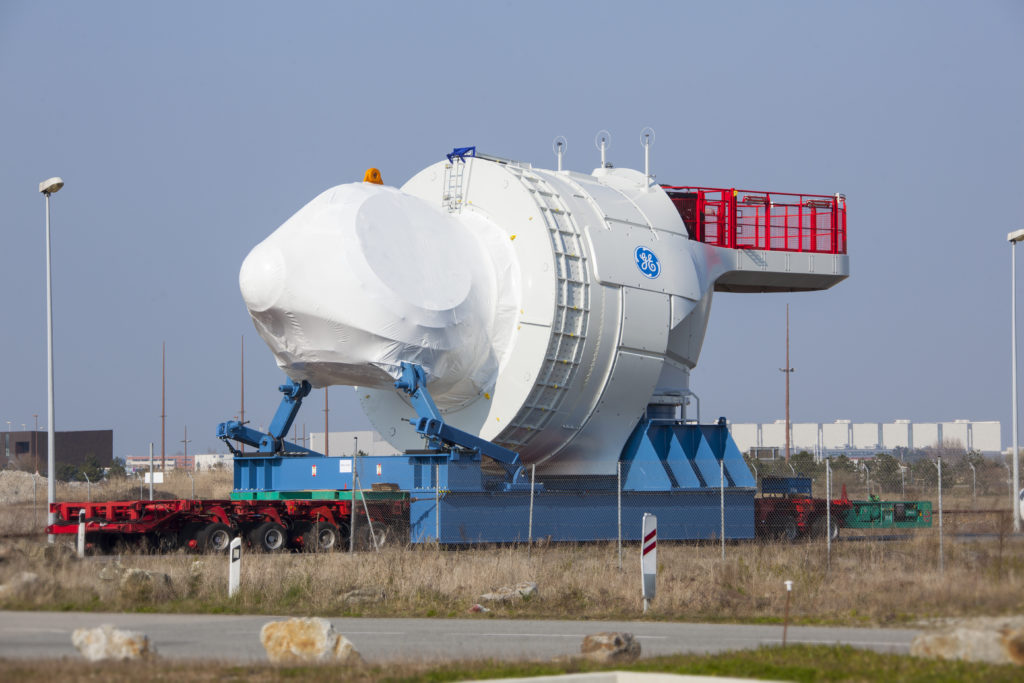
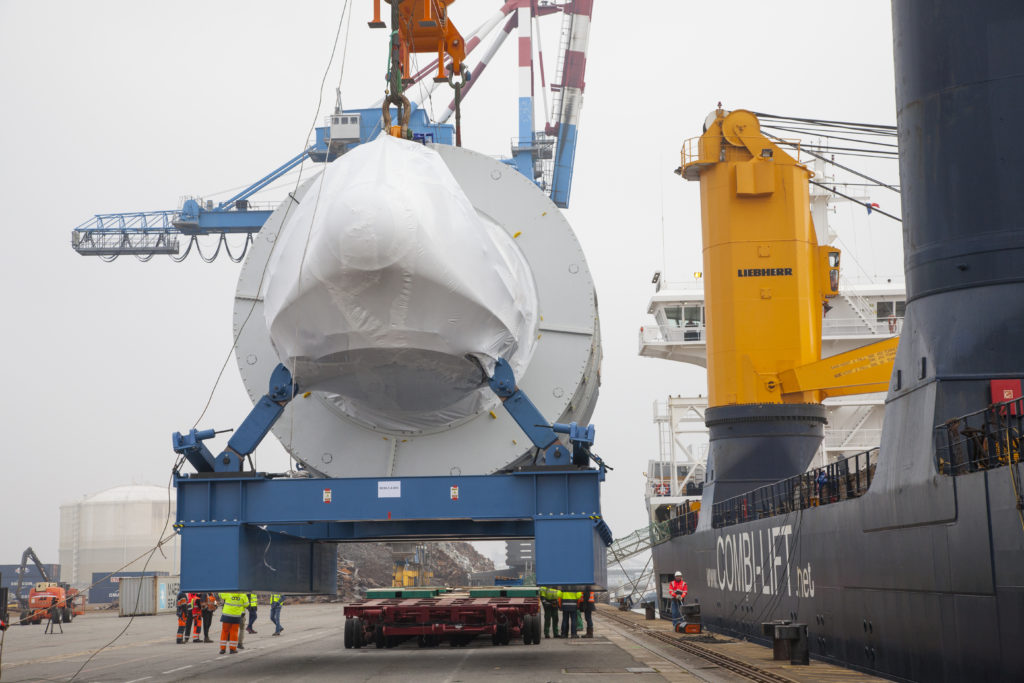
In the port, they load the nacelle onto a ship and dispatch it to its final destination. There are currently two Haliades operating in test mode: one on land in Le Carnet, close to Saint-Nazaire, and the other in the sea outside of Ostende, Belgium. A third test machine left in March for Denmark.

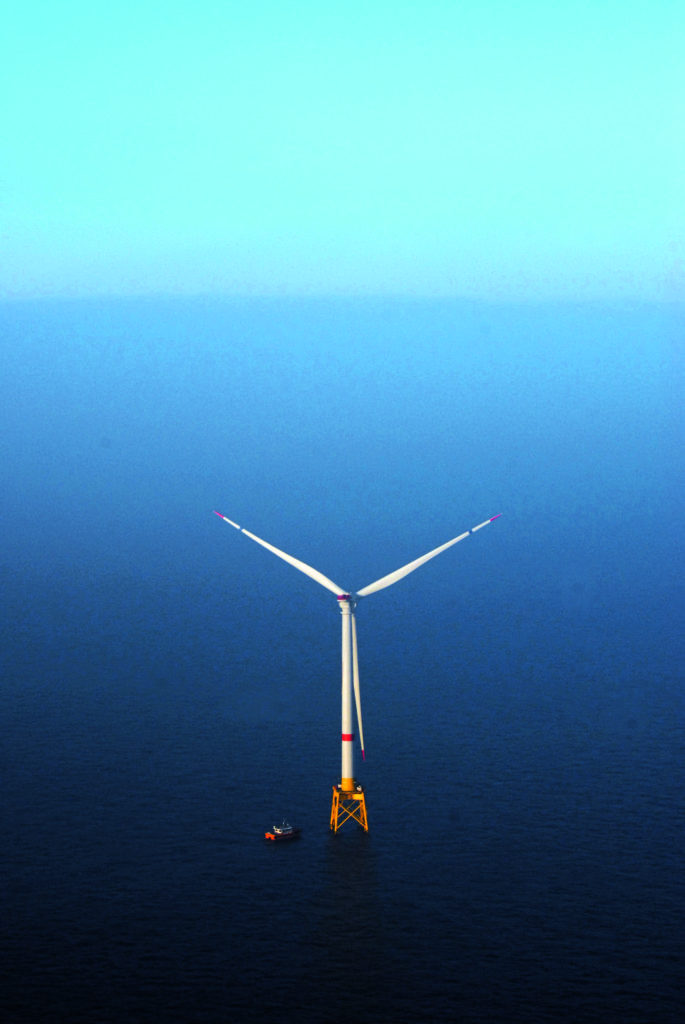
All images credit: A. Bocquel/GE Renewable Energy